Introduction: Folding Candelabrum
This candelabrum looks like an unprepossessing block of wood when folded up, but opens out into an interesting array holding 9 tealights (or, with the means of some inserts, 9 regular candles). You can also make a version of this project out of a single piece of 2×4 lumber: see the last step.
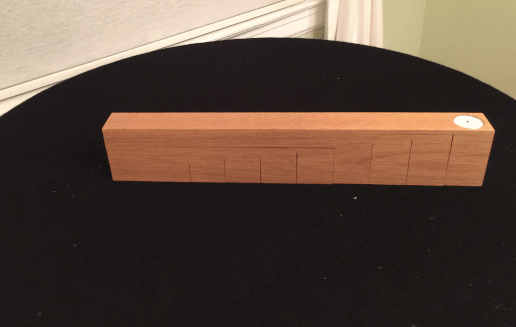
Step 1: Design
The design evolved as I constructed it. I wanted it to be easy to make - just simple straight cuts on table saw and miter saw - but had a shape that was unusual and surprising and did not waste any material. The idea was to have a whole lot of nested L-shaped hinges that contained wells in each elbow. It required a series of cuts in a piece of wood of appropriate size, starting with a rip cut, then a cross cut at 2 degrees, another rip cut, a cross cut at 4 degrees, and so on. The pairs of pieces would then be glued together in L-shapes, holes drilled for the candles, and a dowel inserted to act as a hinge. I prototyped it in poplar (shown above) before making the final version in white oak.
Step 2: Dimension the Wood
I took a piece of 8/4 rough sawn oak and jointed and planed it to a thickness of just under 2" (48 mm). I'm currently spoiled with access to the Pier 9 workshop, and they have an awesome Martin jointer and thickness planer. This was the first time I'd done either operation; very satisfying for someone used to building everything from construction lumber!
I'd actually resolved that during my residency I wouldn't make anything I could have made just as easily at home, but after taking the Advanced Wood class I had a hankering for some analog making, and this project is what resulted. Many thanks to all the shop staff: Trent, Josh, Mei, and Mary-Elizabeth were all great sources of expertise on this project.
Step 3: Rip and Crosscut
Make the following cuts sequentially on a single block of wood (at least) 1 7/8" × 20" × 4" (50 × 500 × 100 mm). Make sure the block is oriented the same way for every cut!
1. Rip a 1/4" (6 mm) strip off the long edge.
2. Crosscut a piece 2" (50 mm) wide with the saw at a 2 degree angle off vertical (i.e. at 88 degrees to the board).
3. Repeat steps 1. and 2., increasing the angle of the saw blade by 2 degrees each time. Do this 7 times (the last block of wood does not need cutting).
Sand each piece to the level of finish you want. It is more difficult to sand the interior parts once glued into L-shapes. A sheet of fine sandpaper placed on a flat surface is ideal; power-sanding is liable to round edges.
Step 4: Glue
Glue pairs of matching pieces together in an L-shape using wood glue and a clamp. Line everything up as best you can. Be sure to use enough glue and not starve the joint (i.e. don't over-tighten).
Step 5: Drill Holes
Drill a 1 1/2" (38 mm) hole 3/4" (18 mm) deep down into the thick part of each L-shaped piece with a Forstner bit. This is much easier with a drill press, but probably doable at a pinch with a cordless drill or a hand drill. Clamp everything firmly either way.
Step 6: Trim and Sand
Because of the kerf of the saw blade, nothing will line up. Wrap the block in masking tape making sure that all pieces are tightly held together. Trim both irregular edges square using the miter saw and table saw. Sand the saw marks off the new edges.
Remove the tape, and wrap tape around the largest perimeter. Sand the untaped surfaces flush and smooth (by hand or preferably with belt or drum sander).
Step 7: Hinge
Remove the masking tape and treat each piece with several coats of mineral oil or whatever finish you like.
The candelabrum uses a pivot hinge. You will need a dowel almost as long as the block is tall and a washer of larger diameter than the dowel. Drill a washer-sized hole 1/4" deep in the bottom of the block, centered where the dowel will go (i.e. equidistant from the sides and the end. Now drill a dowel-sized hole from the bottom of the block ALMOST to the top, as shown. Don't break the surface if you can help it. Dry-fit the dowel. If everything closes up properly and moves smoothly (if it doesn't sand down the dowel until everything fits), glue the dowel into the top hole and leave to dry clamped up.
Cut the dowel so it matches the depth of the washer-sized hole. Drill a hole in the block for a screw to hold the washer - I used a pocket hole screw.
Step 8: Inserts
3D print the attached STL file 9 times if you want to also be able to use regular candles in your candelabrum. The idea of these is that they're able to catch at least some of the wax that dribbles down as well as holding the candles securely. They can be printed without supports.
To fold the candelabrum up again, remove the candles with holders attached.
Attachments
Step 9: B(H)andsaw Version
It occurred to me while doing this that a candelabrum designed for regular candles could easily be cut out of a single piece of 2×4 lumber without gluing if you had a bandsaw handy and you were prepared to have a seven-candle version (a nine-candle version could easily be cut out of a 2×6). So I did, because unusually... I had a bandsaw handy. If you have a plentiful supply of elbow grease, you could use a handsaw. Anyway, here's a one step explanation of this build:
- clean up the board on all sides using a sander or plane.
- mark cross lines 1.5" (38 mm) apart. Then run lines lengthwise 3/8" (10 mm) apart.
- make a series of cuts 1.5" apart at increasing angles at decreasing depths. I used 5 degree intervals because that was what was marked on the bandsaw table. This is a little hard to explain in text but easy if you look at the pictures.
- rip the board to join up with the top of the cut. Use a handsaw to finish off the small angled piece that remains.
- repeat for the remaining pieces.
Sand each piece and drill a candle-sized hole in the top of each piece. Treat with mineral oil. Add a dowel just as for the fancier version. Add candles and you're done.
It will be harder to get a perfect finish on this version, but it is easy and quick. I hadn't used a bandsaw before, so I cut a little deep in some places and doubtless my lines aren't as straight as a pro's would be.