Introduction: LED Light Painting With 3D Printer
Google "light painting" and you'll find some amazing things. Light painting is the process of using lights (like LEDS) to make artistic photos.
In this Instructable, I'll share my process for making light paintings with the assistance of a 3D printer (or other CNC machine)
Things you'll need:
1. A camera capable of taking long exposure photos (I'm using a Nikon D5000)
2. A 3D printer (or other CNC machine)
3. An LED
4. A battery to power the LED (I'm using a 3V coin cell battery)
5. Some electrical tape
6. An image you'd like to turn into a light painting (higher contrast images work better)
Software you'll need (all free):
a.Inkscape (or other image editing software capable of making .SVG files)
b.Fusion360(free for hobbiests)
c. Repetier (or other 3D printing software)
Things I'd recommend:
i. A tripod (you'll need to keep the camera very stable for a few minutes at a time)
ii. A remote to trigger the shutter of the camera
iii. A sewing needle
Step 1: Prep Your LED
Picture 1: Take a bit of electrical tape and make a small hole in it (I've used a sewing needle to do this). Different sized holes will give different effects for your photos. Depending on how far your camera is from your printer and your camera settings, you may not need to cover any of the LED.
Picture 2: Cover the top of the LED with the piece of tape you just put a hole through.
Picture 3: Connect the LED 'legs' to the battery and wrap with electrical tape. The longer leg of the LED (anode) touches the positive side of the battery. The shorter leg of the LED (cathode) touches the negative side of the battery.
Picture 4: If you like, cover the hole thing in tape, making sure light is still coming through the little hole at the tip of the LED.
Picture 5: Find a good location on your printer to secure your LED then find which direction it should be facing. Usually on or near the hotend is the best place to put it. The direction your light should face, depends on your printer. If your printer is similar to mine, in that its Y-axis arm moves back and forth, as well as up and down (when Z-axis is controlled), then you'll want to point your LED perpendicular to the Y-axis.
if your printer is different: If your Z-axis moves independently from your X or Y-axis, point your LED up. Or you could try pointing the LED down, and use a mirror under it on a 45 degree angle. With this type of printer, you probably won't get the same layered effect I have in my photos, but I'm sure you'd still be able to do some neat things. If you do put a mirror under your hotend, be careful not to home your printer into the mirror.
For some machines like delta printers and some CNC routers, you can make light paintings from 3D scans that make use of X,Y, and Z axis, as they are all 'connected'
Picture 6: Now let's quickly confirm we've picked a good spot for our LED by framing up a shot. Place your camera perpendicular to your LED and move the printer around. The LED should be able to move in 2 axis, as we expected from picture 5.
Picture 7:Tape the LED to your printer. There are more secure ways of doing this, but this was easy and seemed to work alright.
Step 2: Find and Prep an Image.
Picture 1 - Choosing an image: When taking a photo or looking for an image, keep in mind that it will probably turn out better if it's high in contrast..
Picture 2 - Scaling image:Scale your image so it fits on the page, first, click on it once with your 'select and deform tool', then while holding the 'ctrl key' (windows PC) on your keyboard (to keep length and width ratios equal), drag a corner to until it's the size you'd like.
Picture 3 - Trace bitmap: After clicking on your image with the 'select and deform tool,' select Path >> Trace bitmap from the top drop down menu (or press 'shift' + 'alt' + 'b' for windows users). Then uncheck smooth and check stacked scans (not sure if this is important), and remove background. Then click ok.
Picture 4- Delete original image (but keep new black and white bitmap): now, again, with the select and deform tool' selected, move your overlapped image over, then delete the one that isn't black and white.
save as .SVG: go to File >>Save as, then make sure under "save as type" you select "inkscape SVG (*.svg)."
Step 3: Convert to .SVG Image to .STL Printable File
Picture 1: Open fusion 360, make sure your in 'model' mode, and then select the 'insert' drop down, followed by 'insert svg.'
Picture 2: Select which axis you'd like your image to be on (you can later adjust this with your printing software), then click the folder icon and find your SVG you just made
Picture3: Your SVG should now look something like this.
PIcture4: Select extrude from the create drop down, and start clicking on portions of the image you'd like to put emphasis on.
Picture 5: In the distance tab type in 1mm, then press ok.
Picture 6:Your 3D model should now look something like this.
Picture7: Making sure to right click the top directory of your 3D file, select "save as STL."
Step 4: STL to Gcode
Picture 1 - Add object to Repeiter: Open up Repeier and press the 'Add object' '+' button. Then find the .SVG you made and select it.
Picture 2: We'll now need to adjust the scale and orientation of our object.
Picture 3 - Adjusting orientation: Make sure to position your STL so it is parallel to your cameras lens.
Picture 4 - Adjusting Scale: Adjust scale of X and Y so it fits in your printer. Click on the locking icon so you can adjust the depth of your .STL. I found a 3 works well, but experiment with other thicknesses.
Step 5: Setting Up Your Slicing Profile
Picture 1 - Slicing tab in Repetier: In the Repetier slicer tab, select 'configuration.'
Picture 2 - Layers and perimeters: save a new 'printer settings' and name it "Light show." Decide how spaced out your layers should be. Too far spaced and you'll reduce the resolution of your print, too closely spaced, and you won't get the same layered effect.
Picturer 3 - Infill: If you don't want any of the interior of the print to be picked up, set fill density to 0.
Picture 4 - Speed: Adjust 'perimeters' and 'travel' to desired speed. Slower perimeters will thicken the light lines of the body of your .STL. increasing your 'travel' speed thins the lines of white space between your .STLs body. Making either of these too slow, and it'll take longer to capture a photo of. Making either too fast, and your printer will start skipping steps and you probably won't get the image you were expecting. I set me travel speed to 500mm/s, but I think it was limited to 200mm/s by the max print speed at the bottom of the window. My 'perimeters' speed were set to 15mm/s.
Picture 5 - Filament tab: I haven't played around with different diameters of filament. If your printer doesn't have a, prevent extruding under low temperatures feature, you may want to make sure you don't have filament loaded in it, or you may want to unplug your exturder stepper motor. I've set my printer to 25 degrees as a fail safe in case I forget to edit the g-code in order to prevent it from getting hot.
Picture 6 - Extruder settings: Save a new printer settings tab as "LED_LIGHT_SHOW. I set my nozzle diameter to 1mm. Unfortunately, you can't have it set to any thing smaller than the layer height (you'll get errors if you try slicing it this way). I probably should have set retraction to 0.
Picture 7 - G-code: Once you've made your slicing profile, try slicing it and see if you like the results. If so, great. If not, play around with it a bit more. When you are happy, (from the print preview tab) click on the 'Edit G-Code' button. Then delete "M104 S25; set temperature" and "M109 25; ...." so your extruder doesn't need to heat up before you "print."
Step 6: Setup for Your Photo
The right location: Pick a spot that's dark, like in a room without windows, or wait for night.
Framing the shot: Move the printer around and look through your cameras viewfinder (or screen), making sure the LED will be seen by the camera at your printers min and max points.
Camera settings - Manual mode: Set your camera to manualmode.
Camera settings - ISO: Set to low.
Camera settings - Fstop: Set on the higher end (let less light in).
Camera settings -Shutter speed: Set to "time" (or "bulb" if you're not not using a remote).
Camera settings - release mode: change to remote.
Step 7: Take Some Photos!
Now go to the manual control tab and print.
Press your shutter button on your camera remote to start, then press it again to finish your photo.
If you're not happy with the way your photo turned out, change some settings and try again.
To recap the main variables that I found to change the outcome of your photo are
1. size of hole you make to expose LED light
2. LED brightness
3. slicer settings (i.e. speeds of print, layer height, and nozzle/filament diameters)
4. camera settings (i.e. ISO, F-stop, length of time you'll have the shutter open for)
5. brightness of room
6. steadiness of camera
A couple of other things that might be interesting to try.... using another machine that can capture a 3D image, connecting an RGB LED to an arduino and program a colour shift at various points in the print.
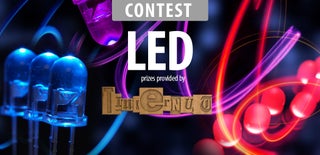
Participated in the
LED Contest
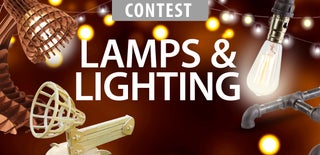
Participated in the
Lamps and Lighting Contest 2016