Introduction: R2D2 Heels
These ARE the droids you're looking for!
Forget protocol, droid, and mash up everyone's favorite astromech with mid-heels and create the greatest footwear the Empire has ever seen. These R2D2 shoes are the hottest thing this side of Tatooine and they’re cooler than Hoth.
The wide heel of these shoes was removed and replaced with a steel bolt to provide strength and support, but at a fraction of the size. An R2D2 toy covers the heel bolt, and the toes have been decorated with lenses, blue accents, and a blinking red LED to let everyone know just how this droid rolls.
This project follows mostly the same process as Dinosaur Heels, but with a few more additions to take it to the next level. Whether you're dashing to Tosche Station for power converters or just going to the store, these R2D2 heels are sure to give you geek cred faster than you can shut down all the trash compactors on the detention level.
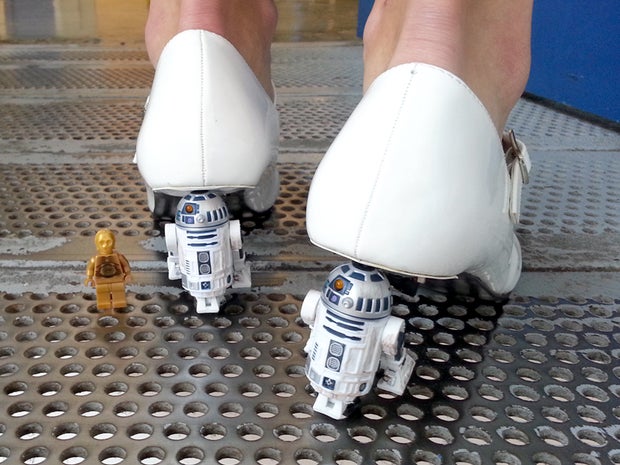
Here's what I used to make mine
Ready to save the galaxy in style? beep boop beep!
Forget protocol, droid, and mash up everyone's favorite astromech with mid-heels and create the greatest footwear the Empire has ever seen. These R2D2 shoes are the hottest thing this side of Tatooine and they’re cooler than Hoth.
The wide heel of these shoes was removed and replaced with a steel bolt to provide strength and support, but at a fraction of the size. An R2D2 toy covers the heel bolt, and the toes have been decorated with lenses, blue accents, and a blinking red LED to let everyone know just how this droid rolls.
This project follows mostly the same process as Dinosaur Heels, but with a few more additions to take it to the next level. Whether you're dashing to Tosche Station for power converters or just going to the store, these R2D2 heels are sure to give you geek cred faster than you can shut down all the trash compactors on the detention level.
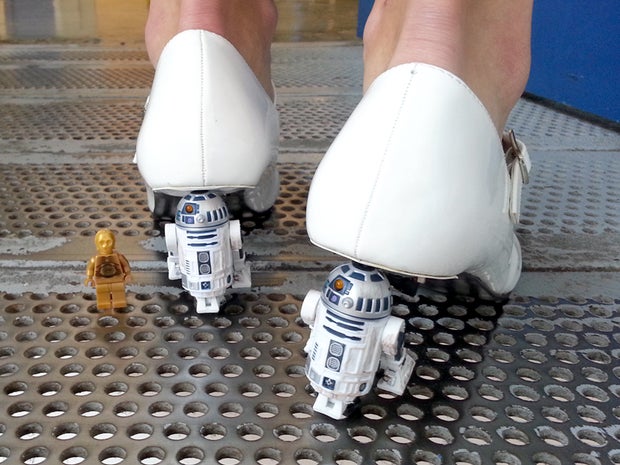
Here's what I used to make mine
tools:
| materials:
|
Ready to save the galaxy in style? beep boop beep!
Step 1: Materials + Concept
I followed mostly the same concept and process as with Dinosaur Heels.
The idea is to replace the standard heel with a slender support post, then hide that post witha hollow plastic dinosaur R2D2 toys. This will give the illusion that the dinosaur astromech is holding up the shoe.
R2D2: The toys I used had electronics inside that allowed them tolight up and make sounds when a button was pushed. Since I wanted to retain these features I could not drill straight through, rather a valley was made in the back of the R2D2 toys that would go around the bolt heel.
Shoes:I chose a crocodile skin texture for my shoes, as it looked the most dinosaur-esque and matched my dinosaurs
I found these brand new shoes for free outside my apartment. How perfect is that?! White shoes = R2D2 awesomesauce!
Bolts: Any 1/4" bolt will work, cut to height.
End Caps: I needed to protect the end of the heel spikes from damaging any floor surfaces when walking. I managed to modify the existing heel caps to work with my new design.
The idea is to replace the standard heel with a slender support post, then hide that post with
R2D2: The toys I used had electronics inside that allowed them tolight up and make sounds when a button was pushed. Since I wanted to retain these features I could not drill straight through, rather a valley was made in the back of the R2D2 toys that would go around the bolt heel.
Shoes:
I found these brand new shoes for free outside my apartment. How perfect is that?! White shoes = R2D2 awesomesauce!
Bolts: Any 1/4" bolt will work, cut to height.
End Caps: I needed to protect the end of the heel spikes from damaging any floor surfaces when walking. I managed to modify the existing heel caps to work with my new design.
Step 2: Heel Breakdown
...
I'm sure all ladies shoes are manufactured in a similar fashion. Your shoes may be slightly different in construction and may require a different method than the ones shown here for modification.
I started by removing the small plastic heel cap with pliers, then bisected the decorative leather sole at the heel and removed the sole portion that was glued to the heel. Making sure not to damage the heel veneer, the white heel covering was peeled back and removed. Set aside this scrap for later as we'll be using it in Step 6 to cover the underside of the shoe where the old heel used to be.
The heel of these shoes were held on with a large industrial cleat that mechanically fastened the heel to the sole and adhesive. The cleat was attached from the top of the shoe under the insole through the sole and embedded deep in the plastic heel. It was no small undertaking removing this cleat. I worked for about 20 minutes getting these heels off.
Once removed the old plastic heels can be discarded.
...
After the cleat and heel are removed it's time to prepare the shoe for welding.
This shoe has a steel shank under the insole for support, my shoe had the shank riveted to the insole, so the entire insole was removed from the shoe. The underside of the shank was abraded at the heel with a rotary tool, this will clear away any debris and prepare the surface for accepting a weld.
The heel cleat opening left a jagged edge which needed to be fixed. I easily cut away excess shoe around the cleat opening and then reinserted the shank-insole back into the shoe to approximated where I was going to weld my new steel heel spike, the new heel location was marked on the steel shank with indelible marker.
I'm sure all ladies shoes are manufactured in a similar fashion. Your shoes may be slightly different in construction and may require a different method than the ones shown here for modification.
I started by removing the small plastic heel cap with pliers, then bisected the decorative leather sole at the heel and removed the sole portion that was glued to the heel. Making sure not to damage the heel veneer, the white heel covering was peeled back and removed. Set aside this scrap for later as we'll be using it in Step 6 to cover the underside of the shoe where the old heel used to be.
The heel of these shoes were held on with a large industrial cleat that mechanically fastened the heel to the sole and adhesive. The cleat was attached from the top of the shoe under the insole through the sole and embedded deep in the plastic heel. It was no small undertaking removing this cleat. I worked for about 20 minutes getting these heels off.
Once removed the old plastic heels can be discarded.
...
After the cleat and heel are removed it's time to prepare the shoe for welding.
This shoe has a steel shank under the insole for support, my shoe had the shank riveted to the insole, so the entire insole was removed from the shoe. The underside of the shank was abraded at the heel with a rotary tool, this will clear away any debris and prepare the surface for accepting a weld.
The heel cleat opening left a jagged edge which needed to be fixed. I easily cut away excess shoe around the cleat opening and then reinserted the shank-insole back into the shoe to approximated where I was going to weld my new steel heel spike, the new heel location was marked on the steel shank with indelible marker.
Step 3: Cut and Attach Foam and Lenses
I wanted to give these shoes a toe treatment with some elements distinctive to R2D2, mainly his 2 lenses, blinking light and blue accents. All these elements are glued to the shoe toe. (tip: to ensure proper adhesion select areas of the toe were gently roughed up with sandpaper to remove the high-gloss finish). Here's how I made each of these elements:
large lens:
R2D2 has one large, dark lens. Since my heels will have one of these on both toes I used a cheap pair of sunglass lenses. The lenses popped out of the frame easily and I traced a large circle shape using a coin. The circular shape was cut using a rotary tool. I used a strong construction adhesive to affix the large lens to the toe, the adhesive is partially elastic and allows some flex which will prevent the lens from popping off when being worn.
blue accents:
I couldn't find any foam sheets in the blue hue I wanted, but they did have a foam cowboy hat that was the perfect colour. I cut off the flat brim and traced R2D2's head accents, then cut them out with scissors. The blue accents were glued onto the shoe toes using a "foam glue" I found at the craft store. This glue looks like white glue, but less viscus and sort of melts the foam a little to create the bond. This glue too about a day to completely cure, so masking tape was used to hold the foam in place.
small extruded lens:
I used the focusing lens of two small flashlights I got from the Dollar Store. The flashlights were broken down and the lens and black housing was glued to the toe using flexible construction adhesive.
blinky light: see next step
tip: adhering the elements to the toe was very time consuming due to long curing times and the delicacy of work. Each element was done separately and were individually taped or clamped down while glue was curing. Be patient with this part to ensure good quality results. I do not recommend using fast-set epoxy as the accelerated curing time reduces the effective bond.
large lens:
R2D2 has one large, dark lens. Since my heels will have one of these on both toes I used a cheap pair of sunglass lenses. The lenses popped out of the frame easily and I traced a large circle shape using a coin. The circular shape was cut using a rotary tool. I used a strong construction adhesive to affix the large lens to the toe, the adhesive is partially elastic and allows some flex which will prevent the lens from popping off when being worn.
blue accents:
I couldn't find any foam sheets in the blue hue I wanted, but they did have a foam cowboy hat that was the perfect colour. I cut off the flat brim and traced R2D2's head accents, then cut them out with scissors. The blue accents were glued onto the shoe toes using a "foam glue" I found at the craft store. This glue looks like white glue, but less viscus and sort of melts the foam a little to create the bond. This glue too about a day to completely cure, so masking tape was used to hold the foam in place.
small extruded lens:
I used the focusing lens of two small flashlights I got from the Dollar Store. The flashlights were broken down and the lens and black housing was glued to the toe using flexible construction adhesive.
blinky light: see next step
tip: adhering the elements to the toe was very time consuming due to long curing times and the delicacy of work. Each element was done separately and were individually taped or clamped down while glue was curing. Be patient with this part to ensure good quality results. I do not recommend using fast-set epoxy as the accelerated curing time reduces the effective bond.
Step 4: Blinky LED Circuit
These shoes also have R2D2's signature blinking light for added authenticity. The wiring is a simple circuit that has a switch to operate, one red blink LED, and is powered by one 3V coin cell battery.
switch + battery:
The battery holder has two prings on teh back, these prongs were lined up on the underside of the shoe next to where the new heel will be located. Small openings were poked into the underside of the shoe to facilitate wiring. The switch was connected to one terminal of the battery holder and then wires were soldered to the remaining battery terminal and one side of the switch. The wires were fed through the openings and the switch and battery assembly was then epoxied in place.
LED holder:
The LED holder I used was a polished metal, a perfect addition. However the threaded mounting neck was much too long and would be uncomfortable to the wearer when installed. The mounting nut was tightened and then the neck was shortened using a rotary tool. Backing off the mounting nut completely ensures the threads are retained.
A drill was used to drill through the foam and shoe to create an opening to mount the LED holder. After installing the LED holder the mounting bracket was threaded back on to secure the holder.
LED's:
I chose to flatten the top of my 5mm red LED's to they sat flush when inserted in the LED holder. Using a rotary tool the LED tops were shave down to about 2/3 their original height. The legs of the LED were bent at 90 degrees and wired to the circuit.
wiring:
After the elements have been installed the excess wiring can be glued down using small dabs of hot glue. I also chose to add a small scrap of soft fabric to the inside of the toe to cover the wiring and protect toes from rubbing against any exposed wiring.
switch + battery:
The battery holder has two prings on teh back, these prongs were lined up on the underside of the shoe next to where the new heel will be located. Small openings were poked into the underside of the shoe to facilitate wiring. The switch was connected to one terminal of the battery holder and then wires were soldered to the remaining battery terminal and one side of the switch. The wires were fed through the openings and the switch and battery assembly was then epoxied in place.
LED holder:
The LED holder I used was a polished metal, a perfect addition. However the threaded mounting neck was much too long and would be uncomfortable to the wearer when installed. The mounting nut was tightened and then the neck was shortened using a rotary tool. Backing off the mounting nut completely ensures the threads are retained.
A drill was used to drill through the foam and shoe to create an opening to mount the LED holder. After installing the LED holder the mounting bracket was threaded back on to secure the holder.
LED's:
I chose to flatten the top of my 5mm red LED's to they sat flush when inserted in the LED holder. Using a rotary tool the LED tops were shave down to about 2/3 their original height. The legs of the LED were bent at 90 degrees and wired to the circuit.
wiring:
After the elements have been installed the excess wiring can be glued down using small dabs of hot glue. I also chose to add a small scrap of soft fabric to the inside of the toe to cover the wiring and protect toes from rubbing against any exposed wiring.
Step 5: Welding + Painting
...
welding:
The original heel for this shoe had a wide flange at the heel which helped support the width and weight of the heel and foot. This new design calls for a slender, uniform heel spike and will require a platform to support the wearer's weight in lieu of a wide flange like the original.
A small heel platform was made from scrap 1/8" sheet steel. I used an angle grinder to cut out rough rectangles, then rounded the corners until I had a platform that fit inside the insole. The platform was then welded to the steel shank.
The 1/4" stainless steel bolts were then lined up and tacked in place to ensure position was correct. While the bold is tack welded on is a good time to make any minor adjustments to the angle of the bolt. It helped to put the insole and shank back in the shoe with the tack weld to ensure the heels are perpendicular to the ground. When alignment is ensured, weld the bolts in place for both shoes.
cut heel spike to length:
After welding the insole and shank was put back into the shoe with the dinosaur placed along side. The heel spike was then cut to be about 1/4" longer than the height of where the dinosaur back will meet the shoe.
painting:
After welding the insoles were masked and the heel was primed and painted with 2 coats of matte white
welding:
The original heel for this shoe had a wide flange at the heel which helped support the width and weight of the heel and foot. This new design calls for a slender, uniform heel spike and will require a platform to support the wearer's weight in lieu of a wide flange like the original.
A small heel platform was made from scrap 1/8" sheet steel. I used an angle grinder to cut out rough rectangles, then rounded the corners until I had a platform that fit inside the insole. The platform was then welded to the steel shank.
The 1/4" stainless steel bolts were then lined up and tacked in place to ensure position was correct. While the bold is tack welded on is a good time to make any minor adjustments to the angle of the bolt. It helped to put the insole and shank back in the shoe with the tack weld to ensure the heels are perpendicular to the ground. When alignment is ensured, weld the bolts in place for both shoes.
cut heel spike to length:
After welding the insole and shank was put back into the shoe with the dinosaur placed along side. The heel spike was then cut to be about 1/4" longer than the height of where the dinosaur back will meet the shoe.
painting:
After welding the insoles were masked and the heel was primed and painted with 2 coats of matte white
Step 6: Cover Rough Edges + Glue Insole
...
Remember the heel covering I asked you to set aside in Step 2? We're going to use them here.
Using the old heel covering I covered the underside of the shoe and trimmed to match. A small opening was then made in the covering for the new heel spike.
Using heavy-duty rubber cement the painted heel insoles were glued into the shoe form. They were clamped in place and left to cure overnight. These insoles neatly cover the installed wiring.
Remember the heel covering I asked you to set aside in Step 2? We're going to use them here.
Using the old heel covering I covered the underside of the shoe and trimmed to match. A small opening was then made in the covering for the new heel spike.
Using heavy-duty rubber cement the painted heel insoles were glued into the shoe form. They were clamped in place and left to cure overnight. These insoles neatly cover the installed wiring.
Step 7: Heel Assembly
Improving on my previous design I decided to try and reuse the existing heel caps. Since these heels started with a wide heel base and were transformed into a much thinner heel I was able to make two new heel caps from just one of the originals.
The heel cap was first bisected using a rotary tool. Holding the hex nut with pliers the nuts were heated using a propane torch, when red-hot the nuts were pressed into the plastic of the heel cap, making a cavity the exact shape of the hex nut. I inserted these nuts about 3/4 into the cap. The hex nuts were removed and the plastic and nut were set aside to cool. Using a rotary tool and hobby knife the edges of the heel cap were cleaned up and the small island in the centre of the cavity was trimmed down to allow the threaded heel to be fully inserted.
The hex nuts were then primed and painted with 2 coats of matte white paint.
While the paint was drying each heel hap was then trimmed down in size and shaped to a smaller, rounded cap, about 3-4mm (1/8") offset from the diameter of the hex nut.
After the paint was dry the hex nuts were epoxied into the heel cap and the assembly was then epoxied and threaded onto the heel spike.
The heel cap was first bisected using a rotary tool. Holding the hex nut with pliers the nuts were heated using a propane torch, when red-hot the nuts were pressed into the plastic of the heel cap, making a cavity the exact shape of the hex nut. I inserted these nuts about 3/4 into the cap. The hex nuts were removed and the plastic and nut were set aside to cool. Using a rotary tool and hobby knife the edges of the heel cap were cleaned up and the small island in the centre of the cavity was trimmed down to allow the threaded heel to be fully inserted.
The hex nuts were then primed and painted with 2 coats of matte white paint.
While the paint was drying each heel hap was then trimmed down in size and shaped to a smaller, rounded cap, about 3-4mm (1/8") offset from the diameter of the hex nut.
After the paint was dry the hex nuts were epoxied into the heel cap and the assembly was then epoxied and threaded onto the heel spike.
Step 8: Adding R2 Unit + Install Padded Insole
R2D2 is cylindrical and doesn't have geometry that lends itself to easily attaching to another cylindrical object (the heel spike). I made a valley in the back of each R2D2 by using the shaft of my soldering iron. tip: this is a smelly process, make sure you are working in a well ventilated area.
While the soldering iron is still hot make sure yo wipe off the plastic that has melted to it before it burns on there for good. I made these valleys as deep as I could before I hit the electronics and batteries inside. The valley doesn't have to completely conceal the heel but needs to be deep enough to allow good adhesion between the toy and the heel spike.
Each toy was then positioned in the correct spot on the heel, facing back, then epoxied in place. These were taped in place and the epoxy was left to cure overnight. After, the padded insoles were installed with a small dab of rubber cement.
While the soldering iron is still hot make sure yo wipe off the plastic that has melted to it before it burns on there for good. I made these valleys as deep as I could before I hit the electronics and batteries inside. The valley doesn't have to completely conceal the heel but needs to be deep enough to allow good adhesion between the toy and the heel spike.
Each toy was then positioned in the correct spot on the heel, facing back, then epoxied in place. These were taped in place and the epoxy was left to cure overnight. After, the padded insoles were installed with a small dab of rubber cement.
Step 9: These ARE the Droids You're Looking For
With the epoxy set and the padded insole inserted these shoes are ready for adventure!
All that's left to do is:
- flick the switch where the heel meets the sole to make the LEDs blink,
- press the button on the toy to make R2D2 make sounds and light up,
- save the galaxy.
Have you made your own shoes inspired by this project? I want to see it!
Happy making :)