Introduction: Tim's PET Bottle Strip Cutter
I have seen many people showing machines to turn PET bottles into PET filament for the 3D Printer.
Not many show how to make the parts in detail, I am currently working on designing and making my own.
I think I have come up with a good 3D printed design for cutting the bottles into strips.
The first step to turning the PET Bottle into Filament is to cut a bottle into one long strip.
I have designed this for the 2 litre bottle (100mm Diameter), but I may modify it to take other size bottles.
Supplies
Hot Air Gun, or some other heat source.
Metal Tubing, 10mm, 12mm or 1/2in. diameter, 350mm long. Copper or Steel, It's weight wants to be more than 1.5g. It's weight aides the process.
Screws M3 x 10mm long. Philips Pan head Flat Tail self tappers.
Screws M1.7 x 10mm long. Philips Pan head Flat Tail self tappers.
Two Roller Bearings. MR128ZZ 8mm Inside Diameter, 12mm Outside Diameter, 3.5mm Width.
An old Craft Knife Blade. About 8mm wide, 22mm long.
Step 1: Printed Parts
These are the part to be printed.
Two parts need to match the diameter of the tube you use. The metal tube that I used is what I had in my box of bits.
I have done three different versions of two of the parts, this is because they are bespoke to the size of the tube used. Gives some choice to what tube to use.
*They are named accordingly:
- If you are using 10mm tube then you need to print parts named for 10mm.
- If you are using 12mm tube then you need to print parts named for 12mm
- If you are using 1/2in tube then you need to print parts named for Half-Inch.
You do not need to print all versions of these two pieces.
One Guide_Cap*
One Bottle Guide*
One Cutter Base.
Two Bearing Cap.
One Bottle_Cutter_Handle (Print hols down)
One Small Washer (Use the printed one or a normal one)
One Line Guide Inner
One Line Guide Outer
Print Settings
I didn't go overboard with the amount of plastic use for this tool, the settings are quite minimal.
I have used PLA.
Layer Height: 0.2
Shell Thickness: 0.8mm
Bottom/Top Thickness: 0.8
Fill: 20%
Print Temperature: 200 deg.C
Bed Temperature: 50 deg.C
Attachments
Step 2: The Cutter
Fit the lower bearing first using a Cap and a M3x10mm self taping screw.
Fit the next bearing with the other Cap and M3x10mm self taping screw. Do not over tighten. I have allowed for slack in the bearing so that the two Bearings edges sit tight against each other.
Tighten it down so that the bearings still move, move stiffly but do move by hand.
I have used an old craft knife blade to be a skid plate in front of the bearing. any thin piece of metal will do. If there is nothing here, the bottle plastic will cut through the cutter base over time.
Use an M1.7 self tapper to hold it in place. Take care screwing in the self tapper, I usually screw self tappers back and forth, when I screw them in for the first time.
Step 3: The Handle
Fit the cutter and the bottle guide to the handle, using eight M3 x 10mm self tapping screws as shown.
There are more holes than needed in the handle, this is so I didn't have to reprint while experimenting.
Step 4: Bottle Guide
Fit the Bottle Guide Cap to one end of the Tube. (350mm long)
It should be a tight push fit. It's a permanent fixture
Step 5: Bottle Preparation
I have seen many ways to clean and prepare the bottle for cutting, this the way I do it.
- First I wash out any residue beverage with soap and warm water, I remove the label at this time also. I then rinse it out with clod water and leave about an inch of cold water in the bottle and replace the cap.
- I then place the base of it in boiling water. This boils the water that I left inside, which expands. I then shake the bottle, doing this heats up the air inside the bottle, which expands. With everything expanding inside the bottle, quite a bit of pressure inside the bottle has built up. (I have seen people adapt a cap with a valve and use a bicycle pump to pressurise the bottle)
- While it is pressurised I use an external heat source to remove any sharp creases. I don't try to do the base. If I put too much external heat in a place I can use the water inside to cool it.
Once I have removed the creases it time to cut off the bottom.
Step 6: Mark the Cut Line at the Bottom
To make sure that the strip of plastic we make is a fairly straight strip, we need to cut the bottom off in a spiral shape.
To do this I use a piece of the plastic strip from a previous bottle, and the Line Guide Inner and Outer printed parts.
These are held together using two M2.7 x 10mm self tapping screws.
But we haven't cut one yet, I here you say. For the first time we can use a sheet of A4 paper, wrap it around the bottle so the two ends are close together, and offset the ends by 10mm.
They need to be offset so that it looks like it is going to create spiral of a left handed thread.
With the guide in the first position draw a line, then rotate the guide in line with the line draw to extend the line so there is an overlap.
Step 7: Cut of the Bottom
I cut off the bottom roughly beyond the line, then cut the bottle following the line. This makes it easier to get a smooth line.
The reason I have made the line spiral with a left-hand thread is so the scissors cut easier. Try cutting the offcut one way then the other, you see what I mean.
You should end up as shown with a short piece of strip to feed into the cutter.
Step 8: Attach the Bottle Guide
The Tube for the bottle guide slides in the top of the bottle.
The bottle guide cap should screw onto the top of the bottle. Just like a bottle cap.
This Tube will keep the bottle aligned correctly with the cutter and also add some weight to keep the bottle held down against the skid plate.
The bottle thread may have a quick release system incorporated within the thread.
I have made the Bottle Guide Cap to utilizes this system. When rotated to the correct position, the cap will push on, then it just need a little turn to lock it in position.
It will undo in the reverse order. A small twist and a pull.
Step 9: Time to Make the Plastic Strip
Place the Tube in the bottle guide on the cutter assembly.
Feed the cut strip under the brings between the two bearing posts.
Turn the Bottle so the end of the cut is in front of the bearings and the bottle rests against the skid plate.
It should be just a matter of pulling the plastic strip through the bearings now.
Hold the cutter so that the bottle is upright, don't restrict the Tube as it comes through the Bottle Guide.
Pull the strip through in a slightly downward direction away from the bottle as it comes out of the cutter.
Step 10: How It Should Go
This is a video to try and explain it. (It may be a bit loud towards the end when I pull the plastic through the cutter)
Step 11: Next Steps
I am still awaiting parts to build the filament making machine.
As and when I get parts I will make an Instructable about the next part. The next part is a little complex so it will be some time until I do it.
But I thought this was a good design I came up with for the cutter and thought I would share it now.
In the mean time you could weave baskets. :)
Step 12: An Other Use for the Strip
If you know some good weaving patterns, it could be used to weave things.
I have done a mix of 3D print and plastic strip to make a little cup type thing to hold some pens and things.
I have seen lots of other uses for this strip on the internet.
Do a search for uses with plastic bottle strip, I was amazed at what other things it has been used for.
Step 13: Different Sizes
While experimenting I have made some different widths.
Also upgraded the previous.
There is now:
- 04mm
- 08mm
- 10mm
- 12mm
- 14mm
I have added the STL Files named accordingly.
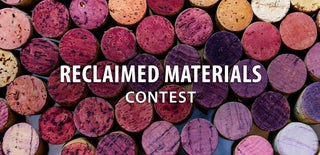
Participated in the
Reclaimed Materials Contest