Introduction: Making an Audio Mixer
This simple passive DIY stereo audio mixer demonstrates resistors in use. When I say stereo, I am not talking about your home entertainment signal, but an audio track with a separate left and right channel.
This mixer will allow us to combine two stereo tracks into one single track, while adjusting the volume of both tracks individually and together.
We will also go over techniques for mounting electronics in an enclosure. Since this is primarily a lesson in electronics and not building enclosures, it is not necessary that you mount your electronics in exactly the same way I do. However, I recommend trying to follow along.
To learn more about resistor or electronics in general, check out the Electronics Class.
Step 1: Lesson Materials
In this lesson we will be making a Simple Stereo Mixer. I will also be demonstrating how resistors work by making a paper resistor.
For the Simple Stereo Mixer project you will need:
(x2) 10K dual log potentiometers
(x4) 1K resistors
(x3) 1/8" stereo jacks
(x2) Knobs
(x1) 4" x 2" x 1" project enclosure
(x3) Stereo cables
(x1) Split back sticker paper (for printer)
(Note that some of the links on this page are affiliate links. This does not change the cost of the item for you. I reinvest whatever proceeds I receive into making new projects. If you would like any suggestions for alternative suppliers, please let me know.)
Step 2: Mixing the Signals
A stereo signal is two channels (left and right) which are actually two separate audio signals with a shared ground.
If we want to combine two stereo signals into one, we will need to mix together the left channel of each stereo signal, and the right channel of each signal.
The easiest way to do this is to combine them together using resistors.
If you connect each respective left channels to a 1K resistor, and the other end of each resistor together, then you have effectively mixed the left channels together. The right channels can be mixed in identical fashion. You are left with a two channel stereo mixer.
This schematic shows the left channels and the right channels being connected together through resistors.
The three boxes that look like strange renderings of potted flowers are actually audio jacks with their barrels connected to ground. The triangles next to each jack represent a channel. Also, notice the strange half-loop to the right of the 1K resistor that is third from top? That loop represents a 'hop' in the schematic and means not to connect those wires together. Otherwise, any time lines intersect, they should be connected together.
This is the simplest audio mixer you can make, but hardly the best one.
Step 3: Volume Control
Simply combining the signals though does not give you any volume control.
To add volume control, we use potentiometers.
The potentiometer is connected in such a way that it functions as a voltage divider between the incoming signal from each channel and ground. Thus, depending on how much the potentiometer is turned will determine how much voltage the signal will be allowed to have when it passes through the center pin to the mixing resistors. The output voltage from the center pin is basically the volume of the signal.
Keep in mind, the input signals volume can always be decreased in this manner, but never increased, since it is only adding resistance to the signal and no additional power.
Step 4: Dual Potentiometers
You may have noticed that by using a potentiometer for each channel, the right and left channels of the same stereo track were being controlled individually. Since you likely want each track to maintain equal volume levels on both the left and right channels, you will need something to control both channels at once.
To do this, you will need a dual (or "ganged") potentiometer. This is essentially two potentiometers built into a single package and controlled by a single shaft.
By using a dual potentiometer, we are able to control both tracks at the same time. In fact, dual potentiometers are largely manufactured exclusively as stereo volume knobs, and typically have logarithmic tapers.
Ours is logarithmic and you can tell this because it is labeled with an "A" instead of a "B" in front of its printed value rating.
Step 5: Label
Before you start, download and print out the attached files onto a sticker sheet.
Sticker sheet with split-back perforation is ideal (as you will see in a moment).
Step 6: Label the Enclosure
Typically enclosures are made as after thoughts for electronics projects. In most of these projects throughout this class we will be starting with the enclosure. Not only that, I am going to show you how to build them well. There will be no soap dishes with wires sticking out of them in this class. If you want to ignore my methodology and go your own way, that is your business. However, I intend to show you how to do it correctly.
First of all, aesthetics are important and you should always make things that look reasonably good. Why invest a lot of time making something if it's hastily jammed haphazardly into a travel soap dish as an afterthought? The nicer you can make this, the less likely it will be to get thrown away some day.
Secondly, understanding the constraints of the enclosure means that you have clearly planned ahead and know what needs to get done. This actually makes it easier to build and debug the circuit.
To begin, trim the labels down with scissors and peel the top label such that the far ends still have their backings on. This is where having split-back sticker paper comes in very handy because you can peel only a little bit of the label at a time.
The reason for doing it this way is because the enclosure's mounting screws will ultimately be hidden under the label. At the end, you will need to be able to get underneath the corners of the label to fasten the case shut. It is only at this point that the label will be fully applied.
Stick this partially peeled label to the enclosure's lid.
Also, while you're at it, stick the input and output jack labels to the sides of the enclosure.
Step 7: Drill
Now it is time to drill holes in the enclosure for the potentiometers and jacks using the label's drilling guides.
Find the cross hairs on each of the labels and make drilling guides by tapping them on center with a hammer and nail. When working with metal enclosures, you will want to get a proper center punch, but for soft materials like plastic (and possibly aluminum), this is good enough.
Drill pilot holes in each of these indents using a 1/8" drill bit.
Next, widen the holes for the potentiometers in the lid with a 9/32" drill bit (the unofficial drill bit of most potentiometer mounting holes).
Widen the audio jack holes on the sides of the enclosure with a 1/4" drill bit.
Step 8: Positioning Holes
Notice how the potentiometers have little rectangular tabs protruding upward on one side. This tab is meant to be inserted into a hole in the enclosure which is to prevent the entire body of the potentiometer from turning when the shaft is rotated. In order for this to work, we need to make these holes in the enclosure.
To figure out where to drill these holes, insert each of the potentiometer's shafts into the mounting holes upside down. Make note of where the tab is.
Drill in the spots where the tabs are positioned with a 1/8" drill bit.
Step 9: Shorten the Shafts (optional)
This part is optional, but recommended if you are overly concerned with aesthetics like I am.
If you mount the potentiometers and place the knobs onto the shafts, you will notice they are riding a bit high. On account of this you can easily see the tab mounting hole and parts of the label which are supposed to be hidden. In order to hide these things, you will need shorten the potentiometer shafts to lower the heights of the knobs.
Doing this is easy. Measure to figure out how much the knob needs to be lowered, and then using a hacksaw, cut that much metal off of the potentiometer shaft.
You will immediately notice an appreciable difference.
Repeat the process for the second knob.
Step 10: Wire the Input Jacks
Connect a black wire to the tab on the stereo jack to the terminal electrically connected to the barrel.
Connect a red wire to one of the tabs connected to an internal connector.
Connect a green wire to the other tab.
Which tab the red and green wires get connected to are less important than that both jacks are wired exactly the same. So long as the green and red wires are always connected to the same tabs on all of the jacks, the left and right channels will not get crossed.
Step 11: Wire the Output Jack
This jack should be wired similarly to the input jacks, but instead of connecting one red and one green wire to each of the terminals, we will be connecting two of each.
Step 12: Wire the Inputs
Now we will wire each input jack to a potentiometer.
The ground wires should go to the bottom left tab of each respective potentiometer.
The red wire should get connected to the top right tab.
The green wire should get connected to the bottom right tab.
Step 13: Resistors
Solder 1K resistors to each of the center terminals on the potentiometers.
Trim away the excess lead on the side of the resistors soldered to the potentiometer, but leave the other leads connected on the side of the resistors that has yet to be soldered.
Step 14: Attach the Output Jack Signal Wires
We are going to start attaching the output jack by connecting the red and green signal wires.
Slide 1" of heat shrink tubing onto each of the jack's signal wires. The color is not remarkably important.
Solder a red wire to one of the resistor leads coming from the 1K resistor connected on the top center of the potentiometer. Then, attach the other red wire to the other 1K resistor connected to the top center of the other potentiometer.
Solder the green wires in a similar fashion to the 1K resistors connected to the lower center pins.
When all of the wires are connected to resistors, trim the excess leads and insulate them with shrink tube.
Step 15: Wiring Ground
Connect the ground wire from the jack to any of the pins on the left side of either potentiometer.
Finally, use another black wire to solder together all of the pins (top and bottom) on the left side of both potentiometers. These are all ground pins, and should all be connected with one another and the black output wires on all three jacks. If you miss connecting any of the ground wires together, this likely won't work right.
Step 16: Test It Out
Once all of the ground wires are connected, the circuit should be complete.
Before you mount it in the enclosure, test it out fully and make certain it works.
Step 17: Mount the Components
Remove the all of the mounting nuts from the potentiometers and jacks.
Insert the components into the enclosure, and then twist back on all of the mounting hardware to lock everything in place.
Step 18: Seal the Deal
Use the enclosure's mounting screw to fasten the lid firmly shut.
Finally, peel the remaining back off the label, and stick it down over the mounting screws.
Normally, we wouldn't cover the mounting screws with the label because it will prevent us from reopening the case later.
However, in this case it is okay because this is a passive mixer. Being passive means it uses no external power source. The only electricity is coming from the audio signal themselves. Thus, we will never need to open the case to replace a battery, nor will we likely ever need to repair anything.
Step 19: Finishing Touches
Twist the knobs entirely to the left.
Line up the knob's indicator marks with the appropriate marking on the label, and then fasten the knob in place using it's set screw.
Step 20: Give It a Go
You should now be done, and able to mix together to separate stereo tracks.
Keep in mind, this is one way to make a mixer using resistors, but not the best way to make one. The resistors result in some loss of volume. This is particularly problematic if you decided to build one with more tracks.
This method also might result in cross-talk between the tracks, which can become a problem if any of the audio is going through a special effect circuit. There would be nothing stopping the effect from getting applied to all tracks.
The best way to make a mixer is to make an active one using Op Amps. This method both prevents volume loss and cross-talk. This is far beyond the basic circuit we made here. However, should you want to learn the knowledge and skills to tackle that project, check out my Electronics Class.
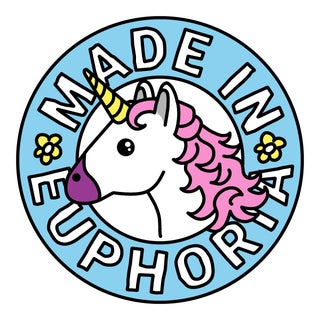
Did you find this useful, fun, or entertaining?
Follow @madeineuphoria to see my latest projects.