Introduction: 3d Printed Manual Test Stand
3d printing is awesome. Period. It changed my life. Although many times it is used to do things that are already done, which is perfect to me. This is one of those cases. In my quest to learn more and more about 3d food printing, I needed to fine a way to measure the "strength" of different printed tests.
For that I bought a force gauge, but that alone was not enough. I founded a few manual test stands online that I could buy but budget was not there. So... FUN TIME! Make my own.
This build has been part of being part of the science sandbox fellowship at New Lab. It is been a great experience being part of their first cohort!
Well, so... this is an instructable on how to build a manual test stand. I use it for compression only and for parts that require less than 5 kg of force. Lets get going~~~
Step 1: Parts
This is not obviously only made with 3d printed parts. but it has a few. There are three main blocks. Force gauge, lift system and DRO. IF you are curious to see or download the model here you have the A360 link, I modeled it using Fusion360 (represent!).
- Force gauge measures the force needed to crush candy
- Lift mechanisms supports the force gauge and moves it up and down manually controlled
- DRO measure the position of the force gauge
Parts:
3d printed:
- Wheel
- Force gauge holder
- Lower bearing holder
- Top rails retainer
Out the shelf
- Force Gauge
- Rail kit
- DRO
- Base
- Lots of nuts. I honestely dont have a list for this because I was using whatever I could find. Although the only specific one needed is the M4x10 for the bearings
STL's are attached to this step. Although I recommend to go directly and mess with the model.
BTW all parts were printed with and Ultimaker 3 at New Lab and that thing rocks!
Step 2: Assembly
Assembly is not hard but you need to follow certain steps otherwise you wont have access to some screws. That being said I ended up not using all the possible screws because the hole system felt sturdy enough.
Tips
- You can either install the force gauge add the very beginning or at the end. If you choose to do it at the end, like me you will miss one screw. (totally find by me)
- Force gauge holder. Attach first the DRO sliding unit, after that the linear bearings.
- Insert the rail into the base, and run through the force gauge holder assembly
- Attach the rails top retainers including the upper leadscrew bearing.
- Align the leadscrew
- Secure the lower bearing holder to the base
Following these few tips and common sense this is a pretty easy thing to put together.
The base is just a piece of wood where I inserted the rails and did a couple of holes to keep the lower bearing in place.
An important note is related to the base. The distance between the rails is quite critical to make the force gauge movement (up and down) smooth. Take the time to measure and remeasure the distance between holes before drilling.
Step 3: Testing & Conclusions
As I said the purpose for this manual test stand is to literally crush candy. The goal is to have compression forces values for 3d printed sugar test cylinders. What makes this so exciting to me is that it allow me to compare and build a library of materials and recipes. At the same time having numbers to iterate towards the right choice!
I am super excited about this and hopefully soon I will have results.
This is the first version for the manual test, in the future I would like to add dynamic tracking force/position so I can map compression or texture values to each recipe. But hey, step by step.
I hope you enjoyed. If you made it this far maybe you would enjoy too subscribing to my youtube channel.
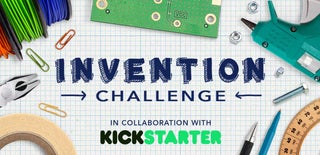
Participated in the
Invention Challenge 2017