Introduction: Concrete USB Charging Hub With Storage
This project is one of the most successful tutorials on my YouTube channel. It uses concrete as a solid and very heavy base material. As a desk accessory, it's probably heavier than it really needs to be, but it sure isn't going to get moved or tipped over accidentally! Functionally I see it having four main purposes. First, it's a USB charging hub for mobile phones, cameras, battery packs, etc. Second and third, it's a pencil/pen cup and storage for charging cords. Lastly, it has served as an interesting conversation piece in my home office.
The original inspiration for this project came from a video on the MAKE YouTube channel, where Giaco Whatever builds a USB hub with concrete as the main element. His version is a lot simpler than mine. Reflecting back, I think I got a bit carried away with enthusiasm.
Please take a few minutes to watch the full build video. I'm sure you will find some of the smaller details that I may have missed in this instructable.
Supplies
Some of the tools and materials I used:
• Quikrete Concrete Mix
• Plywood, 3/4"
• Foam insulation, 2" thickness
Camera and Video Gear:
• Main Camera - http://amzn.to/2iGbWqP
• Main Lens - http://amzn.to/2zbMboA
• Camera Frame - http://amzn.to/2mRPzmX
• Secondary Camera - http://amzn.to/2Bav3B7
• Tripod - http://amzn.to/2hLnRTu
• Lighting Setup - http://amzn.to/2hJioMT
• Magic Arm A - http://amzn.to/2hKvSIq
• Magic Arm B - http://amzn.to/2Bd3NC3
• Video Monitor - http://amzn.to/2zWoJ1T
• Mic - http://amzn.to/2iEucAY
Step 1: Hack the USB Hub!
If you are planning to make your own concrete USB hub, you have many choices to start with. I started with a four port charging hub. There are some six port versions that would probably work just as well. I had to practically destroy the case in order to get to the guts on mine. Once it was apart, I could look it over and take measurements that I needed so that I could start some sketches. As they say, "form follows function".
Step 2: Concept Sketches and Real Dimensions
This is where the two ideas came together. I had imagined what I wanted the thing to look like, but it also had to fit the electronic components inside.
I find grid paper to be very helpful when working like this. I made a 1:1 drawing of the cavity area where the charger parts had to fit. I then worked outward from there. I knew that I had to somehow attach the parts together, but wasn't quite sure yet how that was going to happen. For the charger mount, I figured that I could attach a small piece of wood to the flat side, giving me a surface for fasteners.
I had to make some slight alterations to the wiring. The unit had a removable power cord. I changed that by soldering the mains directly to the circuit board. I wanted to keep the green LED power indicator, so I added a larger LED with extended wires to reach the top of the new housing. You can see what I did in detail in the full video.
Step 3: Getting the CAD Model Built
I really enjoy CAD! This USB power station needed an organic look, so I decided to use the T-Splines modeling environment in Rhino3D. Please note that the T-Splines modeling tools are now available within Autodesk Fusion360. Freeform shapes are a breeze, when working this way.
After the sculpting was finished, I converted to a standard NURBS solid. This allowed me to continue to refine the object, including cutting the top and bottom apart using a sweeping curve. Once I had two pieces, I proceeded to add details like fillets and screw holes.
Step 4: More CAD Details!
Once the main shapes were finished I had to get practical. I added registration "bumps and dents" that would align top and bottom in a secure way, allowing the whole enclosure to be held together with only one screw!
After triple checking everything, I proceeded to create the CAM operations. The top wooden part had to be carved top and bottom sides. The concrete section had to be inverted into a negative form that would be the cavity serving as the concrete mold.
Step 5: Brainstorm! Let's Try Foam Insulation As a Concrete Mold!
Spoiler alert! The foam idea actually worked!
I needed 3" of thickness, so I glued two layers of 2" foam together. I cut them into squares slightly larger that the mold shape. Once the glue setup, I cut off 1" on the bandsaw. The foam is very soft and delicate, but the router did a nice job on the finished surfaces. It almost looked too good to fill with concrete, but I did anyway.
Step 6: Time to Mix Up That Concrete!
I mixed the concrete per instructions on the bag. The stuff I used had fine gravel in it. At first I thought that was going to be a problem, but as it turned out the finished surface was way better than I expected.
I knew that I was going to need a channel on the bottom for the power cord to travel from the front charger unit all the way to the back end where I wanted it to exit. I cut some small scraps to push into the surface to foam those voids. Another last minute decision... I stuck some wood screws into the wet concrete. I thought if they formed threads in the hardened concrete, maybe I could screw them back in during final assembly(?).
I did NOT plan to destroy the mold, but there was no way that it was coming off as one piece. Oh well!
Step 7: Prepping the Wood Brick
I had a small piece of Birch veneer plywood leftover from another project, just enough for this one!
I cut the strips on the bandsaw, then glued and clamped them. Once the block had dried, I drilled some holes for hold-down screws. Because this is a two-sided CNC project, I programmed the CAM to include holes for registration dowels. This allows me to carve the first side then flip it over to cut the other side without losing the accurate position.
Step 8: CNC Router Time!
I loaded up the CAM program, crossed my fingers, and through the switch. I cut the bottom side first, the flipped it over and did the top. I came out pretty clean. I had a few minor issues, but nothing that a couple hours of sand paper couldn't fix.
Step 9: Time for a Test Fit, and Oil
The two parts mated together just as I had planned! No sweat! (well, no more sweat). I moved on to add some Teak Oil finish. The oil really made the stripes in the plywood show up well. Love that contrast!
Step 10: Mounting the Electronics
I found two spots in the aluminum heat sink plates where there was a void behind it. This allowed me to drill and tap two holes. I cut a small piece of 1/4" plywood to act as a mounting board. All that time I spent planning ahead really paid off. It fit together just like it did in the CAD drawing! I added two tiny screws at an angle to secure the board in place.
Step 11: Final Assembly!
Top and bottom went together smoothly, and the USB ports lined up with the holes! I cut two small pieces of black plastic and drilled holes for screws. Very gentle I was able to screw the wood screws back into the holes in the concrete. That was a long-shot, but it worked! The last little detail was to put three rubber feet on the bottom. DONE!
Step 12: Finished!
This has been one of my favorite projects that I have completed over the last few years. This device is used daily by every member of my family. In hindsight, I should have gone with the six port version!
Step 13: Now, Go Watch the YouTube Video to See More Details!
Many of my plans, drawings, and 3D models are available for FREE download on my web site here: https://www.worksbysolo.com
I hope enjoyed this Instructable!
Do you like my work? You can also find me on other social platforms!
• My Website: https://www.worksbysolo.com
• Patreon: https://www.patreon.com/worksbysolo
• YouTube: https://www.youtube.com/worksbysolo
• Instagram: https://www.instagram.com/worksbysolo
• Twitter: https://twitter.com/WorksBySolo
We are a participant in the Amazon Services LLC Associates Program, an affiliate advertising program designed to provide a means for us to earn fees by linking to Amazon.com and affiliated sites.
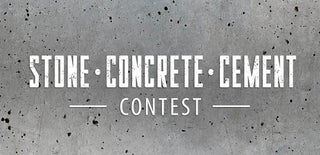
Second Prize in the
Stone Concrete and Cement Contest