Introduction: Dawn of Justice Inspired Batarang
Time for another Batman themed Instructable. Felt the need to make the batarang that was shown during the new Justice League trailer and started this back in the beginning of August. Now this particular version is not 100% accurate, as when I started it I didn't realise that the trailer version is the same as the BatmanVSuperman prop, which has detailed photos online. I worked off of this screengrab, so yeah.
Step 1: Materials
The materials used for this particular replica are the following (note some are Australian versions of other popular products):
- Base material for prototype: I used some scrap plywood for this, but something like acrylic would work better.
- Dremel: Not required, but very helpful in cutting and sanding out the actual shape. I mainly used the sanding drum and cutting tool, but you can use a hacksaw, files or normal sandpaper to shape it out.
- Sandpaper: A variety of grits, I started with 80/120 and worked up to 800 before molding. Up to 400 is fine for painting prep.
- Wood Filler: If you use wood like I did, the grain is not something you want. Spakfilla, Bondo or wood filer can fill them in.
- Foam Core sheets or a 'wall' material: When doing a 2-part mold, it helps if it is in a easy to handle shape (you'll see later), building a wall around the model keeps the silicone in 1 spot.
- Clay: to surround the model when doing a 2 part mold. I use Monster clay because that what I have, but its fine to use any non-airdrying clay
- Molding Silicone: I always use PinkSil, a self-releasing silicone in Australia (cheaper for me than SmoothOn). It is fairly runny so I sometime have to use a thickener agent.
- Release agent: While PinkySil is self releasing (which means it doesn't stick to resin/objects), it does stick to itself. You can use a spray mold release agent, I just used petroleum jelly.
- Casting resin: I used EasyCast polyurethane resin, a 2 part resin which is mix in equal volume and cures to a rigid bone white. It cures in about 5-10 minutes and can be tinted in various colours (I used black tint so it came out grey).
- Paint, Brushes, and Other Stuff: I also needed some paint brushes, paint (silver and black), some latex-free gloves for handling the silicone and resin, and rubber bands to hold the mold together when casting.
Step 2: Prototype With Wood and Plastic
So first we need a base template and initial prototype. I took the screenshot from the trailer, drew out the batarang into a line template, printed it to what I thought was a scale I liked (19cm tip to tip), and cut out 1/2 of it. This was done so I could just tape down the paper to some 6mm plywood, sharpie the outline of 1/2 and flip it over so I could draw a mirror image for the other half. Once you have the outline drawn, you cut out your batarang using a dremel or other cutting tools, and you can sand out the blade edges. I used the sanding drum bit at a 50-60` angle to do this, but a file or something wrapped in sandpaper works fine as well. You can also do all this with acrylic sheets which would probably be better, as the wood was very fragile at the tips.
So I only planned on doing one side of this, casting a double and gluing those together so everything was mirrored but you can probably just use an extra piece of plywood to do the second side of the batarang all at once. I'll go into more detail on the process for the master mold, but essentially I surrounded the wood with clay, built a wall with foam core sheets, poured in silicone and cast 2 resin copies to superglue together. Now that I have a resin base, time to refine, yay...
Step 3: Refining a Master Base
Now we need to add some details to this copy. I used a ruler to draw out the grooves on the faces, and lightly cut them out with an exacto blade. Once I had a guideline I used a pointed clay tool to carve it out a little deeper on each side, and then used some sandpaper to smooth everything over. I believe I went to about 800 with wetsanding to prep for a mold.
Now this is where I decided to redo a chunk of this. I went ahead and did a somewhat messy mold and got some raw casts out, but they felt very thick and didn't seem like something you would throw at criminals (was 11mm thick). I bit the bullet and took my hand powersanded and sanded the faces until it felt thin enough. It ended up being 6mm thick, which felt a lot more 'blade like' to me. Redid the above carving, sanded the blade edges to be a bit wider, and used increasing wetsanding grits until 1200.
Now it's time to make a proper 2-part mold and cast some copies.
Step 4: Molding a Master
So you have your master prop, and it's technically finished/ready to paint. But I wanted multiple copies of it, so I had to make a mold.
Surround the model with some clay like the picture above, and using a blade carefully make the edges where the model meets the clay horizontal , as this will stop the resin from seaping out at the seams or making a bad seam line you will have to clean up later. Once thats done, you need to create some registration keys in the clay, this is so the 2 halves of the silicone mold can lock in together and the final cast is all lined up properly. Just take the end of a pencil/pen/exacto handle and press in a dozen or so holes across the clay, make sure they are not too deep (mine were probably 1cm on average). We also need to make some surrounding walls so the silicone stays put, just cut out 4 lengths of the foam core, stick them into the clay into a rectangle and seal up the corners with tape. Finally we need some vents for excess resin and an entry spout to pour in, I used some scrap craft wood as the pour in spout between the 'ears', and added some vents at the wing and ear tips so air bubbles wouldn't get trapped.
Now to actually make a mold. Silicone is usually packaged into 2 parts, A and B. PinkySil is a bright pink for A and a white for B, and when mixed in equal volume it turns to a pale pink colour which has about a 5 minute working time. Mix up a small batch of whatever silicone you have and make a detail coat of the whole surface, which should stop any bubbles on the surface of the model (which can ruin/cause more work on every cast), and once that cures make a larger batch and pour that in. Let that sit until it sets, and flip the whole think over while removing the walls. Carefully remove the clay and clean off any that is stuck to the model, and apply a release agent to all of the silicone to stop it from sticking to itself. I smeared petroleum jelly across the silicone, but a spray agent would have been easier.
Once that's done, do the same again, a small detail coat followed by a larger layer and let it cure. Once that sets you can carefully peel it apart and take out the original model and there you go, a ready to use 2-part mold. Take something solid like foam core, cut that out to the rectangular shape of the mold and use some rubber bands or clamps to keep the mold shut and it's done.
Now to cast a copy.
Step 5: Casting and Cleaning Up
Now to actually make a resin copy. I used EasyCast, a 2 part polyurethane resin which is mixed in equal volume and cures to a rigid white plastic (Shore hardness of 70, so SmoothOn 300 is essentially the same). I've got a early picture of how it actually cures, as it mixes as a clear liquid and the curing plactic 'spreads out' from its thickest point. I tinted it with some black tint, so it came out a dark grey colour when it cured so if it gets scratched it doesn't show a bright white under the dark paint. You can actually cast this in to methods by either mix up a batch of about 70ml (35ml of A and B) and pout that straight into the mold, or mix up a tiny bit and pour it into each half of the open mold and brush it around. This gives it a thin detail coat of resin that won't capture any air bubbles along the ears or face of the cast, and once that cures tacky/semi solid you can close the mold up and pour in another batch to fill it up. For me this method worked better as the straight pouring method kept catching bubbles.
Which ever methods works for you, you end up with another resin copy of the batarang, with some excess resin on the sides and/or vents. You can just use a knife to carefully cut them off. Take some higher grit sandpaper (I used 240) and lightly sand it to remove any seam lines and the areas where the vents were, you may need a lower grit to remove that. Sand everything over with some 400grit and it should be ready to paint.
Step 6: Painting and Done!
Now you can go about this a couple of ways. I attempted to use some flat black spray paint on a copy, but I think the one I bought was cheap as it would dry properly/kept coming out badly, so I went with just using hand brushes and acrylics. You could also use an airbrush if you have one. I took a very thin brush and painted the grooves silver, taking care to wipe away any that got on the faces. Then taking a larger brush, lightly paint some black acrylic on each side of the batarang, covering everything except the grooves. Now to add the metallic effect with a technique called Dry Brushing. Take a rougher brush, pour out some silver and dip the tip of the brush into it. Take a paper towl and wipe off most of the paint, and lightly brush the edges of the batarang. Each stroke should only leave some 'scratches' of silver, and you can keep doing this until it looks appropriate. You can also do this for the faces to add some battle damage weathering, just remember you can always add more so it's best to add small amounts at a time.
Seal everything with some matt clear spray paint and you are finally done, you have your own Bat of Gotham weapon, good as a display piece or a prop for cosplay costumes.
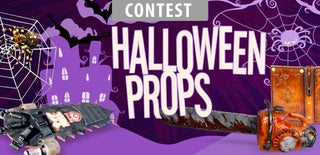
Participated in the
Halloween Props Contest 2016