Introduction: High Visibility Vest
It’s always a good idea to wear high visibility clothing when biking or running around at night. But traditional reflective vests aren’t always the most stylish of garments. Many cyclists or runners I see are wearing attire that looks fit for a construction site. These construction-like vests get the job done but they seriously lack style.
My local library has a maker space with a really awesome laser cutter; I’ve been learning how to use it and have been experimenting with different materials. Last week I decided to try cutting fabric and this is what I ended up making; a stylish alternative to a traditional safety vest.
You will need:
- Safety Fabric/ Utility Fabric (Polyester)
- Iron-On Reflective Tape
- Iron-On Adhesive Tape or Needle and Thread
- Knit Elastic
- Fire
- Iron
- Scissors
- Laser Cutter
- Inkscape
Step 1: Designing in Inkscape
You’ll need a vector image of the vest that can be used for laser cutting. I provided a .svg file of the vest I made (Vest.svg) and you can just use that and skip Step 1. But if you want to design your own I’ll show you how I made mine.
You will need Inkscape. It’s a free and open-source vector graphics editor, you can download it here if you don’t have it. You’ll also need a pattern that you’d like to use- I provided the pattern I used in my example.
- Download and open VestDesign.svg in Inkscape
- If you want to change the size of the page: I wanted the size of my page in Inkscape to be the same size as the cutting area of the laser I was going to be using. I went to File> Document Properties. Under the Page tab, in the Custom Size area, I changed the units to inches, the width:20, and the height:12.
- In the file there should be a circle pattern and the outline of the vest.
- Click on the vest. Go to Path> Linked Offset. A little box will appear by the upper left corner of the vest outline. Take that box and drag it toward the center to create a margin- this is the area along the outside of the vest where nothing will be cut out. Make it as thin or as thick as you’d like.
- Select the smaller vest (It was red but I colored it green) and go to Path >Object to Path.
- If you have a design/pattern that is not in vector format (like this circle design I created) and you want to use it, you’ll have to convert it. The circle pattern needs to be converted from a bitmap image into a vector image. Select the pattern go to Path> Trace Bitmap. Under the Mode Tab, select Brightness Cutoff, Threshold: 0.45. Select Update to see what it will look like, and then press OK.
- Take the pattern and drag it over the vest. Go to Object> Lower to Bottom.
- Delete the original circle pattern (select it and press delete or backspace).
- Select the smaller vest (green) go to Edit> Duplicate.
- With the green vest still selected, hold down Shift and click on the circle pattern. Both of them should be selected now.
- Go to Path> Exclusion
- Hold Shift and click the green vest. Go to Path> Intersection
- Go to Object> Fill and Stroke. Change: Stroke Paint>Flat Color. Change: Fill> No Fill.
- Zoom in to see details. Delete lines and points that you don’t want by clicking or double clicking on the line to reveal a bunch of little squares. Click on each square to select and press delete or backspace to get rid of it. Or click and drag to create a box, that will select multiple points that can be deleted all at once.
- You’re done! Just go to File>Save.
Attachments
Step 2: Cutting
For this project I used the Full Spectrum H-Series desktop CO2 laser (40w). Vector cut, Speed: 100, Power: 50.
- I started off by grabbing a pair of scissors and cutting out a rectangle of fabric slightly larger than the cutting area of the laser (20x12).
- The laser had a honeycomb bed (I think that’s what it’s called) inside. It was pretty dirty so I placed a piece of cardboard between the bed and the fabric. I’m not sure if this step is necessary but the cardboard did create an even surface that it made it easy to smooth out any bumps or folds that were in the fabric. I also tried using wood instead of cardboard and that worked just as well.
- Do whatever you have to do to prepare your laser for use. Once you have everything set up go ahead and run it.
- Keep an eye out for any pieces of material that might blow around after they’ve been cut out. When I cut mine there was one piece that ended up blowing over onto an area that hadn’t been cut yet. The cut had to be paused in order to remove that piece.
- When it’s done you should have a cutout for one half of your vest. Cut out one more so that you can have two pieces, one for the front and one for the back of the vest.
I did each piece of fabric separately. I didn’t try but since the front and back are identical does anyone know if you can just layer two pieces of fabric and do both at the same time?
Step 3: Reflective Tape
Reflective tape/material is great because it doesn’t really look like anything special until light hits it. I came across this roll of iron-on reflective tape and it was super easy to use.
All you have to do is:
- Cut out pieces/shapes
- Place them into your fabric
- Apply heat with an iron (wool setting, 25 seconds)
- Let cool and peel off the protective top layer.
You can add reflective pieces to your vest anywhere you want. I cut out a bunch of small 1cm circles and placed them where the circles in the pattern intersect. This creates a really neat polka dot pattern in the dark when a beam of light hits the reflective material.
Step 4: To Sew or Not to Sew
When I made this vest I didn’t feel like sewing so I used iron-on adhesive to hold everything together. Steam-a-Seam 2 got the job done. It's an iron-on adhesive that lets you bond fabrics without having to sew them- it's like a step above using a glue gun on fabric. You have to pull really hard to break the bond so I don’t think there will be any issues with the vest falling apart. If it does, I’ll only take a minute to reapply and repair. A needle and thread should hold everything together just as well, if not better. If you don’t want to use iron-on adhesive just sew a few simple stitches in its place.
Step 5: Elastic
I added elastic shoulder straps to connect the front and back pieces of the vest.
- Cut (6) 3.5-inch pieces of elastic (I cut mine to be 5” and it made the vest hang too low).
- To prevent fraying, burn the edges of the elastic by holding them over and open flame.
- Cut (12) 1cm pieces of Steam-A-Seam adhesive.
- Steam-A-Seam has a glue side and a paper side. Lay the glue side down (paper side up) onto the end of a piece of elastic and with an iron apply heat for a few seconds. Do this until all of the ends of the elastic pieces have a piece of adhesive. When they are cool enough to touch, remove the paper pieces so that you’re left with just the adhesive.
- Start by attaching elastic to the shoulders on the front half of vest. Lay the vest down, outside (side with reflective tape) facing up. Slide 3 elastic pieces under the strap and tuck them in just far enough so that all of the adhesive is under the fabric (a little more than 1 cm). Space them out evenly and apply heat with iron. Use the same method to attach the straps to the corresponding sides of the back half of the vest.
- Now you can try it on and see how it fits. Use to above method to add a pieces of elastic to the sides (around the waist area) to keep the entire thing from flying around in the wind
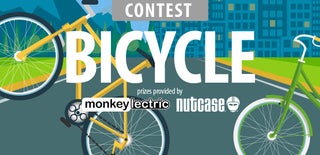
First Prize in the
Bicycle Contest 2016