Introduction: Linear Direct 3D Printer Extruder Drive. Fusion 360.
Designed to directly replace NEMA17 in any 3D printer
High Force to Weight Ratio
High continuous and peak forces
Weight 4.2oz (119 grams)
High Accelerations
Halbach Array magnetic system
Scotch Yoke mechanism
Step 1: Linear 3D Printer Extruder
An extruder with a stepper motor is used in my Pusa I3 and also in
almost all 3D printers. I decided to develop a lighter extruder drive based on a 3-phase linear actuator with a magnetic Halbach array. It is designed to directly replace NEMA17 in any 3D printer.
Normally a linear drive (like VCA or similar) requires metal parts, so I've focused on the applicability of 3D prints with a minimum of metal parts. Such a drive can be made practically at home.
Step 2: The Device
The device has a weight of 119 grams, that is, almost 2.5 times easier than the NEMA17 that is used in my Prusa I3.
This drive requires a 3-phase PWM driver and an ARM microcontroller. The drive seat coincides with the NEMA17 31 mm square and M3 screws. The assembly of the entire device is also M3 screws behind. In the same place is located the shaft of the optical encoder of the feedback.
Step 3: Principle of Operation
Like any electric machine, this drive operate on the principal of the Lorentz force equation. Simplified, this force is directly proportional to the current strength, the length of the conductor, the induction of the magnetic field, and the sine of the angle between the magnetic induction vector and the conductor.
To increase the magnetic flux, the Halbach array was applied.
This will increase the magnetic flux from the conductor and reduce it on the other non-working side. Halbach array does not require an back-iron behind the magnetic system, this is good for the weight parameters of the device.
Step 4: Modeling in Fusion 360
I made all the drawings and animation of the principle of operation in Fusion 360.
As can be seen from the video, the linear movement of the magnetic assembly is converted into a circular movement using the Scotch yoke. This is a very simple and reliable solution that is used in many devices.
Step 5: Components
The body of the drive, as well as the holder of the Halbach array and the details of the Scotch yoke mechanism, are made using the 3D printing method. In addition, we use 3 bearings 625ZZ and pin 2mmX 10mm for the Scotch yoke.
Magnets are an important part of the design. We need 5 Neodymium Rare Earth magnets 5X5X25mm N42 magnets
You can use compound magnets, they will need 10 pieces.
https://www.indigoinstruments.com/magnets/rare_earth/
Shaft D5 X30mm, copper wire AWG28
Step 6: The Coils
The coils are wound on a 3d printed base. The cross section of each coil is 4mm x 6mm. After winding, the coil is wrapped around the coil by PTFE tape.
Two coils are formed in the auxiliary part in such a way that the nested coils are produced.
After forming, all the coils are located in the grooves of the housing.
Step 7: Assembly
The assembly of the magnetic system is very simple, follow the direction of the polarity of the magnets. The direction "north-south" does not matter, the electronic driver will switch the original polarity of the coils in the desired direction.
The Scotch yoke also has no difficulties in assembling, but the shafts of the gear and the encoder must be firmly fixed. To do this, apply a good adhesive when assembling. Next, we collect the device completely. When turning the shaft with your fingers, there should be no mechanical resistance. Otherwise, it is necessary to grind the surface over which the magnetic system slides. As an electronic driver, any 3-phase driver with optical feedback can be used. It should be designed for a current of at least 15 amperes per phase and a voltage of 12 volts.
Step 8: Materials and Files
All the files are listed here.
Filament ABS. Do not use PLA and similar materials, since the drive coils heat up to about 60 degrees, which can lead to deformation of the entire structure and wedging of the extruder.
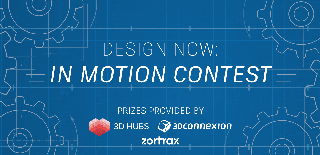
Participated in the
Design Now: In Motion Contest