Introduction: Noctis' Engine Blade - 3d Printed - Final Fantasy XV
Hello there! This Instructable will guide you along the way of making a replica of the Engine Blade from Final Fantasy XV with a 3d printer, as well as giving a general overview of post-processing of 3d printed parts and painting them. I will be your guide. My name is Brian, aka Power Up Props. When you're ready to begin, scroll down to step 1. Thanks for following along!
Step 1: 3d Modeling/3d Printing
In terms of the overall project, step 1 involves gathering references (oddly enough, Pinterest is our best friend here). For the sake of this instructable, I'll combine several parts together. Once you have your folder overflowing with reference photos it's time to take a deep breath and open Fusion 360 (or your 3d modeling program of choice). I made two Engine Blades (one with the Ultima paint job) and over the course of both projects a rough estimate of 3d modeling time probably came in at 100+ hours, with various edits to parts in the "trial and error phase". I don't mean to gloss over this step, as it took longer than the rest of the project combined, but if you're following along at home I already did this for you. Click here: Engine Blade Files on MyMiniFactory.com to download the STL files. If you're interested in learning more about Fusion 360, head on over to their official website that is full of tutorials and information about how to use their software. It's free for hobbyists and has a great community surrounding it.
Alright, so you've downloaded the files and unzipped them into a folder on your desktop. There are a lot of parts, don't let it scare you off. Fire up your 3d printer/slicer of choice and start printing!
Step 2: Initial Part Prepping
Here's where the fun begins. Once you have all of your parts (or enough to start working on them) you need a few supplies to get started. The Blade needs some extra support and has holes for (1) 1/4 inch x 4 feet long steel rod, and (2) 3/16 inch x 3 feet steel rods. These can be found at most hardware stores.
Start with the first part of the blade and glue them into place. My go-to adhesive is Bob Smith Industries Insta-Cura+ super glue and their Insta-Set accelerator/accelerant. If you have two connections, put the super glue on one piece and spray accelerant on the other. When the two substances meet, they bond almost instantly. A word of caution; if you need some time to align it, only use the super glue. That gives you a few more seconds of working time before it sets.
You might be really excited and want to start gluing everything together. Resist that urge because sanding is extremely difficult if you do that.
Step 3: Filler Primer
Everyone has slight variations in their post-processing rituals for 3d printed parts. Personally, I like to do a coat of Rust-Oleum Filler Primer before sanding anything. I primarily print in PLA and raw PLA does not sand well. A quick pass of filler primer gives you a nice sand-able base to work with. I may have gone a little heavy on the coat shown above, but don't be afraid to cover the part in filler primer. The key here is to let it completely dry before sanding. If you had the patience to print the parts, you have the patience to wait at least 24 hours before sanding. I usually let the parts sit in the shop overnight and bring them inside in the morning to finish curing and then sand at night. Rust-Oleum Filler Primer can be found at most hardware stores, like Home Depot or Lowes. I usually keep 5-10 cans on hand at all times. Since you will be using a lot of it, I highly recommend picking up a comfort grip handle.
Disclaimer: I have a spray booth that vents outside of my shop and I still use a rated respirator and eye protection when using spray paint and airbrushes. Spray paint and other chemicals are no laughing matter, be safe, be smart, and use caution. Filler primer is even more potent than your average spray paint.
Step 4: Eat. Sleep. Sand. Repeat
I often get asked how I get 3d prints so smooth. My answer to you: wet sanding and filler primer. It takes time and it takes effort, but if you're patient (I'm sensing a theme) the results will follow.
If you aren't familiar with the concept of wet sanding, I'll give you a breakdown.
Step 1: Get yourself a tub that's at least 6" deep. You don't want it it too tall or too shallow, your wrists will thank you.
Step 2: Fill previously mentioned tub with a reasonable amount of water. Add in a tiny splash of dish soap. Splish splash.
Step 3: Gather your sandpaper. I am a Minnesotan, so it goes without saying, but 3M makes the best sandpaper (Change My Mind). Make sure the sandpaper you are using is approved for wet sanding. If it isn't, it will shred and degrade quickly.
Step 4: Sand away. Start with 120, anything less has a tendency to make a mess of your parts. If you're ambitious, move up to 220 after the next coat. If you're like me, jump to 320. I also like to wear latex gloves while sanding. I made the mistake once of wet sanding without them and couldn't use the fingerprint scanner on my phone for over a week. Learn from my mistakes. Harbor Freight often has sales on their 100 count boxes of latex gloves. Stock up, you'll need them.
Step 5: Repeat this several times until you think your part is silky smooth. If you think you're ready, move on the to the next step.
Step 5: Filler and Primer. Different Than "Filler Primer"
If you've hit your part with filler primer several times and sanded up to 320, you are ready to graduate to the next step!
Now, reading the title of this step you may be confused. "Brian, we already used Filler Primer." Yes, you are correct, you did. Filler primer usually gets 90% of the parts smooth, in my experience. For the other 10 percent and for deep grooves and joints, I like to use another wonderful product by 3M, Bondo Glazing and Spot Putty! This comes in a tube and has the feel of rubbing peanut butter on your 3d printed parts. After approximately 20-30 minutes it hardens and can be wet sanded smooth. Note: Bondo has a strong odor. Only use with proper ventilation and respiratory protection.
Another technique I like to use is a thicker bead of super glue, hit with the accelerant. It hardens and can be sanded smooth to fill in gaps. This takes a bit of practice and sanding but can be a very useful tool. I like to refer to this step as "Filler". Once you think you're done with this, you're ready for primer!
Primer comes in all shapes and sizes, or more so, colors. I like to use a matte black primer. When held up to light, all of the imperfections are very apparent. Make sure the primer you are using works with plastic. I usually do two coats of primer, one wet sanded at 400 and one before applying the top coat, not sanded.
Step 6: Under Coat. Top Coat.
Once your part is primed, you are ready to apply either your undercoat, or top coat, depending on the look you are going for. For the Engine Blade I went with a metallic matte silver undercoat and a gold or gunmetal topcoat, depending on the part.
Depending on the prop, a metallic undercoat allows you to weather your topcoat with sandpaper to reveal the "metal" underneath. This can create a more realistic weathering effect.
On the Engine Blade, I used the undercoat as a light base before applying the top coat. This isn't necessary, just something I like to do.
Time for the top coat. I'm still getting used to an airbrush, so for this project I used spray paints, specifically various Rust-Oleum metallics. When doing your top coat, take your time and do very light passes. You do not want the paint to run on you. As mentioned before, let your paint dry before masking and doing additional layers. Nothing is more disappointing than ruining an entire paint job by being impatient.
Step 7: Assembly and Weathering
Your top coat was a success! If you've made it this far, you're in the home stretch. Time to assemble your prop. Once you've done that, it's time for weathering.
Weathering is my favorite part of every project. The important thing to keep in mind with weathering, is situation. Think about your "weapon." What kind of conditions has it been through? What type of environment has it survived? Does the owner clean it often or has it been dormant for years? When dealing with rust or other heavy weathering techniques, look at pictures of actual rust. Use that as an influence to your weathering.
For the Engine Blade, it has seen some battle, but is owned by a Prince. We want to achieve minor weathering with metallic accents.
On props, the basic go-to weathering technique is a color wash. This involves basic acrylics, mixed with water. Depending on your environment, the grime on your prop will either lean more brown or black. When using more earth tone washes, I like to make custom browns using the primary colors; red, blue, and yellow. It takes some practice to get the ratios correct but you can make various shades of brown using this technique. You can also buy acrylic paints that are already made in various browns. For black washes, I use "Mars Black" acrylic paint.
Once you've selected your paint for the color wash, it's time to dilute it with water. Getting the ratio correct takes practice, but I usually start with a 2:1 mix, using twice as much water as paint. The goal with a color wash is to wash the part, not cover it. Take your mixture and dab on your prop in areas that would naturally gather grime. Let it sit for several moments and then wipe it away with a paper towel. Repeat this as necessary, but don't get too carried away. Be realistic with your weathering. It's easy to do too much, but it takes practice to do just enough.
Another method of weathering is referred to as "dry brushing." I like to do this with Liquitex Heavy Body acrylics and chip brushes (Iridescent Rich Silver and Iridescent Bright Silver are great for this). The goal is to spread out the paint before applying and dab your brush until it's almost dry. You then apply it to your prop in light strokes, giving the prop highlights where it would naturally see weathering.
Step 8: Electronics
LEDs can add some extra flair to a project. For the second Engine Blade I added Neopixels by Adafruit. These are digital LEDs that run off of an Arduino board. I won't get too in depth with this, but refer to their official guide if you are interested. Kamui Cosplay also has a wonderful ebook on advanced LEDs that helped me learn the process. I highly recommend it. Take your time and practice soldering before attempting to install LEDs. Practice. Practice. Practice.
Step 9: Cosplay.
Congrats! If you made it this far, you are ready to show off your finished prop to the world! There were a lot of steps involved, probably some cuts, bruises, and tears, but remember that cosplay is meant to be fun. Crafting and making is a passion of mine, and I want to share my skills, experiences, and failures will all of you. Have fun with your projects and remember to take breaks and enjoy the process. If you have any questions, leave them below or shoot me a message on Instagram or Twitter. "Brace yerself fer power!" Until next time.
Brian
Power Up Props.
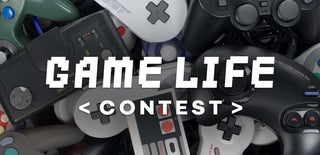
Second Prize in the
Game Life Contest