Introduction: The Heavy Metal Hammock Frame
Have you ever tried to build something with no planning and no preparation? It's definitely not the best way to do things, but taking your time to properly plan a build is often a luxury that we don't have as builders and makers. So for this build, I wanted to set a challenge for myself, I wanted to build a hammock frame with zero planning.
In this post, I plan to talk about 2 things. First and foremost it's going to be all about how to build this bad ass, heavy metal, hammock frame, but at the same time, I'd also like to impart some of the strategies and techniques that I use to figure things out as I go when building something.
So join me as I go from doodle on my office window to reality. I promise you it was an interesting trip, to say the least haha.
Before we start a couple of quick notes. First, there is a YouTube version of this build available above for all of you video lovers. I feel it's the best way to see how this build was done, but don't worry, if you're more of a text and picture person I've got you covered too.
Second, in the interest of full disclosure Krylon sponsored the YouTube video of this build. They've got no idea I'm also making this Instructables post, it's just something I do for all my builds, but I think it's important to put that out there regardless.
Step 1: Cutting My Wood and Breaking Down the Build Into Manageable Steps
Starting this build was a bit overwhelming. As soon as I hit the shop I knew I had a million little details to sort out in my head. When faced with that many details it's really easy to become lost and overwhelmed, so much so that you can become paralyzed with indecision. One thing that I've found that really helps is breaking down a build into more bite-sized, manageable pieces.
So at this point, I decided to start by focusing on the wooden A-frame legs at either end of the hammock. I could figure out how I was going to link them together later.
Step 1 was cutting my wood to length and width. I decided to use Ipe for this build because Ipe is a fantastic wood to use outside. It's extremely dense (SO DENSE) and strong, so it holds up really well to all the abuse mother nature can throw at it.
However, it's not all sunshine and rainbows when you're talking about Ipe. Due to how dense it is, and its high silica content, you need to be careful when working with it. It will very quickly dull your sawblades, so if you've got to cut a lot of Ipe consider using some older saw blades you don't care about. Additionally, the dust it creates is highly toxic, so make sure you're wearing good lung protection!
I cut 4 lengths of Ipe that were 2.5" wide, 1.5" thick and 36" long.
Step 2: Figuring Out How Wide to Make My Legs
Next, I had to figure out how wide to make my A-frame legs.
My method for doing this was EXTREMELY basic, but it worked haha. It's good to keep things simple when you're working in uncharted territory.
I grabbed 2 of my Ipe legs and spread them out until they were the same width as my actual hammock (more on this later). My reasoning here was that if the feet were the same width apart as the hammock, no matter where you were in the hammock, the frame itself wouldn't be able to tip over. Once I had the legs in the position, I measured the interior angle using a digital angle finder.
Step 3: Cutting the Tops of the Legs
The measured interior angle was 118.3 degrees, which I then rounded up to a nice even 120 degrees. Because nice round numbers are much easier to work with. I then took that number, divided it in half, and cut a 60-degree mitre on the end of each leg.
With all four legs cut, I now had to find a way to join them together. I debated wood glue, some sort of lock joint, but at the end of the day, I didn't think any of those options was going to be strong enough for the tension that I planned to put on this frame. No, I would need something much stronger...
Step 4: Cutting the Steel Bracket
Instead, I went for some good old-fashioned steel!
I decided to make some custom brackets to sit right at the tip of my A-frame legs and join both sides together. I picked up a length of 3/16" x 2" flat bar steel and started cutting it into 12" lengths. I cut 8 in total.
Then, using my cordless angle grinder and a cut-off wheel, I cut that same 60-degree angle on the end of each piece of flat bar.
In order to clean up my free-hand cuts, I broke out my belt sander and sanded down the freshly cut edges. I also took the opportunity to slightly bevel those freshly cut edges as well. This would help with the next step...
Step 5: Welding the Steel Bracket
Which was welding. By beveling my welding seems I was creating a valley that would allow the bead of the weld to penetrate deeper into my steel, thereby creating a stronger weld.
I fully welded together the seem of my two bracket halves, then flipped it over and also welded the backside of the seem as well.
Once the welds had cooled, I took the brackets outside and ground down the welds until there were nice and smooth and rounded off the pointed tips of the brackets. No one wants a hammock frame with a sharp edge, that's a recipe for disaster.
In order to make sure that all of my brackets had the same profile I clamped them together and rounded them all off at the same time.
Step 6: Drilling Bolt Holes
Without a way to attach the bracket to Ipe legs, they'd be pretty useless right? So the next step was drilling some holes in them so that I could bolt them to the legs.
I marked out 6 holes on each bracket and then drilled out the holes using my drill press. In order to help cool my bit and keep it from burning out, I applied a little bit of cutting oil before cutting each hole.
Step 7: Adding a Hook to the Brackets
At this point, my brackets were almost done, but they were missing 1 key component: A hook to mount the hammock on.
Lucky for me I had some eye-bolts kicking around the shop that I was easily able to modify for the job. I zipped off the part I needed, flattened its bottom and then welded it directly to the center of the bracket.
I laid a good thick welding bead the whole way around the hook so that I could smooth it out later and make it look a little more elegant.
Step 8: Drilling Bolt Holes in the Legs
One thing that I was really worried about was that my bolt holes need to align perfectly. My margin for error was basically non-existent and I didn't trust my own ability to transcribe the coordinates of the holes from the brackets to the legs.
So instead, I clamped the brackets to the legs and drilled the bolt holes using the brackets themselves as a guide. This way there was no chance of me messing up!
Step 9: Mortising the Brackets Into the Legs
A quick test fit of the bolts into the freshly drilled bolt holes revealed my first major issue on this build (of which there would be a few more). The bolts I bought to secure the brackets to the legs were 2" long. As it turns out, 2" was just a little bit too short and there wasn't enough thread poking out the other side of the legs to properly attach a nut to. Damn.
My solution was to mortise the brackets into the legs. This would decrease the distance between the two plates just enough that my 2" bolts would fit perfectly.
Now the traditional way to do this would be with a hammer and chisel, but I'm not very skilled with traditional tools. So instead I used a trick I've used in the past and grabbed my cordless trim router with a cutting head on it to do the job. I set it to the same depth as the brackets and then slowly walked it across the legs. One cutting head width a time I mortised out an area the same size as the brackets.
This took a while and made quite the mess, but it worked and I also think it significantly improved the look of the hammock frame too.
Step 10: Compound Cutting the Bottoms of the Legs
I had one last thing left to do on these legs (other than finishing them of course) and that was cutting the bottoms of them so that they sat flat on the ground. However, I also wanted the legs to lean back at a 30-degree angle, so I had to do a compound cut on the bottom of each leg.
Compound cuts are a little tricky because instead of thinking in just 2 dimensions, you have to start thinking in 3. Anyone who has ever tried to cut and install crown moulding knows how quickly this can become confusing.
My miter sawhas no problem doing compound cuts luckily, so all this took on my part was a little bit of careful planning and a lot of double-checking my angles.
Step 11: Figuring Out the "V's" With Proxies
With the legs done I was ready to start thinking about how I was going to connect them together. I needed to build some sort of steel frame that would link the two together.
In order to figure it all out, I cleared some floor space in the shop and began taping out an approximation of what I wanted to build on the floor. Once I was satisfied with the shape I began trying to figure out all the angles and lengths of the pieces I would need to build it. I quickly realized that this was going to be a surprisingly complicated job.
I also quickly realized that I didn't have the brainpower necessary to use math to figure all of my measurements. Instead, I opted to use trial and error. Now trial and error isn't a particularly elegant way to get things done, but through the brute force of approximation you can figure out just about anything.
That being said, I wanted to build this connecting frame out of steel, and steel doesn't really lend itself to the trial and error process. It's hard to cut and it's relatively expensive. So instead, I decided to take a lesson I learned in the video editing world and I used a proxy to help figure it all out. Instead of mocking it all up in steel, I decided to use some scrap 2x4s that I had in the shop.
My wood proxies were much easier to work with, so it really sped up the process. I slowly shaved away at the pieces until I had exactly what I wanted.
Step 12: Cutting the Metal for the "V's"
Once I knew what I wanted, it was simply a matter of taking all the measurements from the wood and transferring them over to the 1"x3" tube steel that I bought to make the frame. Since I knew this frame was going to be under significant tension while I was using the hammock I opted for the thicker-walled steel tube. It cost a bit more, but it made the frame that much more rigid and solid feeling.
Again, since there were many complex and compound angles, I cut all of these pieces behind the shop with my cordless angle grinder instead of my metal saw.
Step 13: Welding the "V's"
Back inside I welded the V's together. Keeping them held perfectly in place while I welded was a bit of a challenge since there were so many different angles involved. What I ended up doing was using CA glue to join my wood proxies together and then using those as a brace to hold my tube steel in place while I welded.
CA glue is great because you can use it to join something like two 2x4s together and it sets in seconds.
A quick test fit later and I was ready to move on to the next step!
Step 14: Creating Mounting Plates (And Messing Up)
At this point, I was riding the euphoric high of someone who had just overcome a significant challenge. I pressed forward and started fabricating some mounting plates that I would use to mount my new Vs to the Ipe legs. The design was pretty simple, a 5" long plate with 2 bolt holes. I'd weld the plates to the Vs, bolt everything together and I'd be good to go.... right?
Well, not so much. As it turns out there was a fatal flaw in my plan
Step 15: Figuring Out My Mistakes
The plates I designed didn't really work. Or more accurately, they only half worked.
The lower of the two bolt holes was quite close to the ground, and because the bolts would have to go in at an angle, by the time the lower bolt exited out the backside of the leg it would be touching the floor. Which meant it would be impossible to get a nut on the other side of it. Crap...
This was not good and forced me to re-design how the Vs connected to the legs. Once I discovered the mistake I had made I got pretty frustrated and decided to hit pause on the build (read: I rage quit). After sleeping on the issue I hit the shop feeling renewed, with a new design and a much better attitude.
I think it's important to realize that if you're building something without a well-thought-out plan, you're almost guaranteed to encounter some sort of issue like this. If, and when, you do it's important to remain flexible. These issues will rarely completely derail a build, they'll just force you to make some tweaks here and there.
Step 16: Turning My Mounting Plate, Into a Mounting Shoe
My solution was to turn my mounting plate, into a mounting shoe. I went to the store, bought some more flat bar steel and cut some more 5" long pieces. I then proceed to wrap the steel around the leg, boxing it in on all 4 sides.
By fully wrapping the leg like this I felt comfortable using a single bolt on each leg. Most of the tension would be carried by the actual shoe and the bolt would act more like a cotter pin keeping the leg from sliding up and down. At the end of the day, I actually think this is a superior design. It took a bit more work to pull off, but I like how it looks and functions better.
And as for the lower bolt hole, I simply filled that in with the welder. That way, I wouldn't have to be reminded of my mistake every time I looked at those empty holes.
Step 17: Cutting the Stretcher
Finally, it was time to make the last major component of this frame. I had to cut a stretcher that would join the two Vs together. I cut a single long piece of 1x3 steel, lowered it into position and then realized I had yet another problem to overcome.
The straight cut left by my saw would not fit over the rather complex profile of my Vs. Thankfully a career of framing houses taught me everything I would need to overcome this particular challenge. What I needed was a birdsmouth.
A birdsmouth is a fancy way of saying that I needed to cut a corresponding profile in the ends of my stretcher piece. After a little bit of careful measuring and cutting with the angle grinder, I had shaped the ends of my stretcher so that they fit nicely over the V's, ready to be welded together.
Step 18: Welding the Stretcher
One of the things that I love about welding so much is that you're constantly adding material to whatever you're working on. Practically, this means that you're able to bridge small gaps between pieces you're welding together.
This was good for me because while my birdsmouth cuts were pretty good, there were still a few spots where they didn't make perfect contact with the Vs. In order to fill those gaps in I simply layered the bead of the weld over itself, slowly filling in any air gaps. This is a bit of an art, but as you practice more and more at welding it becomes easier to do.
It also takes a lot of the pressure off when you're cutting metal for a build like this. You don't always have to be super precise, as long as you're in the right ballpark with your cuts, you can usually make it work.
Step 19: Testing the Hammock
Before going any further I had an important test to do. I unboxed my hammock and made sure that it fit tightly between the two ends of my frame.
When you're working on the fly like this it's always important to be constantly testing your work. If I had gone through all the trouble of painting and finishing this frame, only to realize I needed to take make it an inch wider I probably would've been pretty upset with myself. Frequent "sanity checks" help to make sure you don't get too far off course.
Also, you may have noticed I said I unboxed my hammock. That's because I actually used a store-bought hammock. I figured I had my hands full with the construction of the actual frame itself and didn't want to add another variable into the mix. Maybe sometime in the future, I'll make my own, but for this build, I wanted to focus on the frame.
Step 20: Grinding My Welds
One job that I was not looking forward to was cleaning up all of my welds. I'm not a great welder, I think that much is evident from a lot of these pictures. So I had to spend a lot of time grinding away at them to get things nice and smooth.
Normally, I use flap discs on an angle grinder to do the majority of my grinding, but for this build, I tried something a little bit different. I got a die grinder along with a carbide head and used that to attack my ugly welds. This method is a lot rougher, but it does have its advantages. For one, the carbide head lasts a really long time, and because of it's shape it can easily reach tight inside corners and smooth them out.
So I did a lot of the heavy lifting with the die grinder and then I transitioned to the angle grinder with the flap discs to smooth everything out.
Cleaning everything up took a solid day of work in the shop. It was really time-consuming haha.
Step 21: Sanding
As a final step of prep prior to finishing, I gave everything a really good sanding. This just helps to remove a lot of tooling marks and make the metal look smoother. I polished the metal with my random orbital sander and while I was at it, I gave the Ipe legs a good sanding too.
I also used a block sander on the Ipe legs to round their corners and make them a little softer to touch.
Step 22: Painting All the Metal Components
Like I said earlier in the post, the Youtube video of this build was sponsored by Krylon, so when it came time to paint the legs I grabbed some cans of their Colormaxx paint in satin black and went to town on the frame and the brackets.
Normally I like to do my painting inside the shop because it's a climate-controlled environment, but this day was a particularly nice summer day. It wasn't too hot and it wasn't too humid. It was right in that perfect pocket for spray paint application.
It's actually pretty important to get both temperature and humidity right before applying spray paint, so always check the directions on the can or the manufacturer's website before applying!
I sprayed 3 coats on each component and then left them to dry in the shade.
Step 23: Oiling the Legs
Ipe is a tough wood. So tough in fact that you don't really NEED to apply anything to it in order to protect it for outdoor use. That being said, it will turn a silvery-grey color if left untreated. Some people like that look, but personally, I'm not a huge fan. So I applied and a coat of protective oil to my legs.
This oil has a slight stain to it and really made the color of the Ipe pop. I'm a huge fan of how it turned out.
Once the legs and frames were dry I packed everything up in the truck and took it all home to assemble!
Step 24: Setting the Hammock Up at Home
Back at home, I realized I had one last job to do. I installed a single felt pad on the bottom of each leg. These little feet would elevate the legs ~1/4" or so off of the ground and help to prevent the legs from potentially wicking up any moisture. This probably isn't a necessary step given how good Ipe is at resisting moisture, but hey, it couldn't hurt either.
Finally, I rolled out the hammock, hooked it onto the frame and it was FINALLY ready to be used.
Step 25: Enjoying It
With all of the hard work out of the way, it was time to kick back, relax, and enjoy my new creation. And after this build, I definitely needed a break. Even if I had taken the time to plan this build ahead of time, it still would've been really challenging build.
If there's any moral to this story its almost certainly that planning out your builds beforehand is the way to go. It'll save you time, money and a lot of headaches. But, it's not always possible, and I think it's important to have the skills necessary to improvise, build on the fly, and tackle challenges without a fixed game plan. So, I hope seeing some of my thinking and how I problem solved this build will help you if you ever find yourself in a similar situation.
Because honestly, I think we've all been there to some degree or another!
P.s. the hammock is extremely comfortable and makes a great spot to soak up some of the remaining summer sun.
Step 26:
Alright, that's it for this build every one. Thank you for reading! I hope you enjoyed it, if you did you might want to check out my Instagram (Instagram.com/ZacBuilds/) and the aforementioned YouTube channel (youtube.com/zacbuilds) to see the rest of my builds.
If you REALLY liked this build and want to get ad-free early access to all of my builds as well as behind-the-scenes content, consider becoming a supporter on my Patreon. I recently hired a video editor to help me out and create more content and my Patrons go a long way to keeping him employed!
Hope you all have a wonderful day and I will see you in the next build!
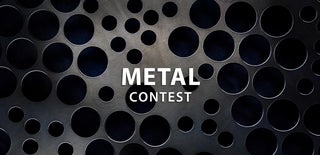
Runner Up in the
Metal Contest