Introduction: The Zero Wood Black and White Concrete Outdoor Table
Have you seen the price of wood lately?! That's a stupid question. Of course, you have. Even if you aren't into building things, you've probably seen all of the news reports in the last couple of months. Depending on the type of wood you're looking for you can expect to pay anywhere between 200-300% more than you normally would.
This is bad timing for me, since, for the first time in my adult life, I actually have quite a bit of outdoor space that I'd like to furnish with some furniture. And I LOVE to build things out of wood. So as the weather starts to slowly improve and the need for outdoor furniture increases by the day, I found myself in a bit of a pickle.
But I'm nothing if not adaptable, so I gave up my beloved wood and started searching for some alternative materials that are suitable for outdoor builds. My search lead me to concrete. It's still cheap as the day is long, and if modern cities are anything to go by it's the perfect material for outdoor applications. So join me as I do my first no-wood build.
Full disclosure: The YouTube video of this build was sponsored by Concrete Countertop Solutions. However, they have no idea that this post exists and I was under no obligation to create it. It's just something I do for all my builds. They were actually really cool about this build, they originally approached me about doing concrete countertops (as the name of their company might imply) but I didn't really have any use for new counters, so I pitched them on this concept (which I already had floating around in my head) where I'd use their products in a more creative way and they told me to go for it!
Step 1: The Video
If you were hoping to see this project in video form, well then don't worry I've got you covered. Here's a link to my YouTube video that documents the whole build:
If you're a little more old school and prefer to read, then I've also got you covered there as well. Just keep on scrolling down :)
Step 2: Assembling the Form
Thankfully melamine sheets are still relatively affordable because the first step of this build was creating a form to cast my concrete table in. Melamine sheets have definitely gone up in price, but not nearly to the same extent as raw lumber.
After cutting the sheet up into some smaller pieces using my track saw and table saw, I assembled them into an open face box that was 32 by 48 inches and one and a half inches deep. Which is approximately the same size as the finished table, but as you’re about to see, it’ll end up being a little smaller than that.
Also, as a quick note: Make sure you screw together your form really well. Concrete is quite heavy and will exert a decent amount of force on the walls of your form. And, if it were to break, it'd make a big mess.
Step 3: Prepping the Form Liners
Form liners are rubbery noodle-like pieces of polyurethane plastic that are typically used to texture the outside edge of a table, countertop, or any other concrete casting.
However, I decided to use them in a slightly different way. I wanted to create the illusion that my table was actually made from a single slab of concrete that had been dropped and then split in two. In order to create that look, I had to take two form liners and join them back to back.
I started by cutting them to length and mitering both ends. It felt a bit wrong to use the miter saw to cut something so soft and flexible, but in the end, it got the job done and that's what matters.
In order to join the two form liners together, I used CA glue. I laid a bead of glue on one of the form liners, sprayed the accelerant on the other liner, and pressed them together. A few seconds later and I had a nice double-sided form liner.
I swear I keep finding new ways to use CA glue on each build, it's so handy to have a glue that bonds to basically everything and sets in few seconds
Step 4: Installing the Form Liners
Then it was time to install the form liners inside the form. Imagine that!
Again, I used, you guessed it, CA glue to secure everything in position. I started in one corner and worked my way to the other corner.
You can see here I’m actually forcing the form liner to twist and contort as I glue it down and that’s because I wanted that center split to look organic and natural. I figured a perfectly straight 45-degree line would’ve looked too artificial. I think these twists and turns help to sell it as a real split.
Step 5: Installing Reinforcing Steel Mesh
Technically this step is probably unnecessary since the concrete I was using is self reinforced with acrylic fibers. But I decided to play it safe and imbed some reinforcing steel mesh. A lifetime of working in residential construction has taught me that you should almost always reinforce concrete and that’s a hard habit to break
No fancy measuring and cutting here I just clamped my mesh in position and zipped off all the unnecessary bits using a cordless angle grinder.
Step 6: Mixing the Concrete
Mixing the concrete turned out to be a little trickier than I initially expected but after doing it a few times I’ve definitely got some tips to share
First off, you want to carefully control the amount of water you use. Each of my bags was designed to be mixed with no more than 3qts(2.84L) of water. Anything more than that and your risk impairing the strength of your concrete. For maximum strength, make sure you follow the specific mixing directions of your concrete.
For my first mix I started with 1 quart of water in the bucket and then slowly added the dry mix along with more water to it. This was a complete waste of time. By the end I was starting with 2 and a half quarts of water in the bucket and keeping a half quart on standby in case I wanted to loosen the mix.
It also became very clear to me that I should’ve used a smaller mixer based on the temperature of my poor cordless drill. The giant paddle I was using created a ton of drag in the concrete. Not only would a smaller mixer have been easier to spin, but it would’ve been better for digging out the corners of the bucket as well.
Step 7: Dumping, Screeding, Troweling
The nice thing about the concrete I was using is that it flows really easily, it is a purpose-made casting concrete after all. With just a little bit of agitation, it will really quickly find its own level in the form. I’ve seen a lot of other concrete builds where people end up adding all sorts of chemicals and additives to their concrete in order to get similar results. The nice thing here is that all that stuff is baked in from the factory so all I had to do was add water
I poured out two bags worth of concrete into my form and then started screeding the concrete. Screeds come in many different shapes and forms, but for this build, I just used an off cut of the melamine from earlier. By gently sliding the board back and forth along the walls of the form I was able to level out the concrete.
I did this a few times while carefully watching for any low spots and used the excess spill over to fill them in. And for all the areas I couldn’t reach with the screed I just went in afterward with a diamond trowel and touched them manually.
Then it was time to start on the second half of the table. The black side.
Step 8: Mixing the Black Concrete
The procedure for the black side was basically the same except I had the added step of mixing a pigment into the concrete. These powdered pigments are used for getting different shades of grey and black in the concrete. You can do actual colors, like red, green, and blue, but in order to achieve those, you actually apply a liquid stain to a partially cured white concrete.
On this build though I found that a half cup of black pigment got me a really nice looking shade of dark grey.
For a nice even distribution of the pigment it’s best to mix it into the water before adding any concrete. You could definitely still add your pigment after mixing the concrete, but it might end up looking a bit uneven and marbled... Which come to think of it, sounds pretty cool, but that’s not what I was going for here.
After the mixing was done, it was back to the same game plan as before. I dumped out some concrete, took a quick break to add my reinforcing steel mesh, and then dumped out some more concrete on top of that. Before I knew it I was screeding the second half of my table, and setting up to do the last, and most important, step of the casting....
Step 9: Vibrating the Forms
Vibrating the forms.
Concrete has the nasty habit of trapping air bubbles in it while it’s still wet. Once the concrete dries those air bubbles can become weak points that compromise the strength of your slab, and they can also look kind of ugly.
So, in order to encourages all of those air bubbles to float on up to the top of my concrete soup, I went around the entire perimeter of the form and gently tapped it with a hammer.I also did the same thing on the rubber form liner as well.
I probably could’ve done a bit better of a job here, but more on that later!
Step 10: Cutting the Metal
Next up I started cutting all the metal I would need to build the base of the table. In order to help myself work as quickly and efficiently as possible, I actually took the time to create a 3D model of this build before I ever hit the shop. From the 3D model, I created a cut list and worked my way down that list. As a result, I was able to batch out all of these cuts really quickly.
Now look, I can already hear all of your collective groans and protest that you don’t know the first thing about 3D modeling, but honestly, it’s not rocket science. I taught myself how to use SketchUp in just an afternoon by following along with some YouTube videos. And it's like I'm creating the 3D model equivalent of the Mona Lisa either. I just made a rough approximations of what I wanted to build that was good enough for me to pull critical measurements from and plan my material purchases.
BTW I’ve started making Sketchup models for all of my builds available on my Patreon page as yet another bonus for patrons.
As I worked my way down the list I placed each freshly cut piece on the underside of the table in its approximate location. This doubled as a quick sanity check on all my measurements and prevented me from accidentally cutting more than I needed.
Step 11: Welding
Once my upside-down bizarro world table looked complete, I slid out the welding table and fired up the old MIG welder
All of the steel I used for this build was an eighth of an inch thick, which is a pretty heavy gauge for furniture but it’s a lot easier to work with. Thinner gauge steels have the nasty habit of melting away on you while you’re welding them.
And while we're at it, I’ve also got a couple of tips to share that I’ve recently learned from more experienced welders. One is to push the tip of the welder away from you as you’re working, this gives you nice even penetration without as much risk of melting through the steel.
Another tip is to make small circular motions with the tip of your welder that look something like the example photo. This gives you a nice clean-looking welding bead and ensures both of your pieces are well stitched together.
Oh and one more tip that I ALWAYS forget to do on my builds. Tube steel usually has a seem on one of its faces, which sometimes can even show through paint. So a good habit to be in is just to take that seem and face it in a direction where no one will ever see it.
Unfortunately I only ever seem to remember that tip while I’m reviewing photos and editing videos.
Step 12: Grinding
Outside, behind the shop, I set up a little grinding station and went to town on all of my welds with a cordless angle grinder and a flap disc. Slowly flattening them out and making them look nice.
This actually reminds me, there is one thing I really wish I changed about the design of this table. I used 2” flat bar steel laid on top of inch and a half tubes. I thought that extra little flange would be a nice detail, but in retrospect, I wish I had just used inch and a half flat bar as well. It would’ve created a flush look that was a lot easier to grind smooth.
All of those those inside corners created by the flanges were a real pain to smooth out.
Step 13: Priming and Painting
When it came time to coat the legs with paint I really wanted to do things well because this table is going to live outside all year round. I live in Canada and we get some pretty dramatic swings in temperature that can really push finishes to their limit.
I started by priming the steel with a white Krylon metal primer. I found that this particular primer is really thin, so the key to getting good results with it is to spray it on lightly in a few coats, otherwise you risk getting some unsightly drips
Even knowing that going in I still got some decently sized drips here, which I had to sand out between coat. But that’s ok, because sanding between coats also helped me to remove some of the leftover grindings marks, so I wasn’t too mad about it.
Once the primer dried it was time to spray on some Krylon's outdoor paint. Which I'm hoping will hold up long term. I bought 2 cans and sprayed on more coats than I care to count. My theory here was that more layers of paint would enhance the long-term durability, but only time will tell if that theory pans out. The color I picked was called midnight sky, which as it turns out, is just a grandiose way of saying black. Besides the name though I was pretty impressed with this paint. It went on a lot thicker than the primer and evened itself out really well.
Once I was done spraying I left the legs to dry, and the concrete to cure, overnight
Step 14: De-Forming the Concrete
72 hours after the initial casting I returned to the shop and started stripping the forms.
This was actually a lot easier than I thought it would be. After casting the concrete I was kicking myself for not using some sort of release agent on the melamine, but as it turns out this concrete, and maybe concrete in general, doesn’t stick to melamine. The black side was a little trickier to release than the white, but I eventually got it by just ripping off the form liner.
Once I flipped the concrete slabs over and revealed their nice smooth finish surfaces it was love at first sight. That being said there were some things to note. Along the outside edge of the slabs, there were still quite a few bubbles trapped in the concrete. They didn't bother me since the tops of the slabs were so smooth, the rough edges were a nice reminder that the material was in fact real concrete. But if you're going for a completely smooth look at home, I'd advise you spend a lot of time vibrating the forms and working the edges to prevent this.
There were also a few small bubbles on the surface of the slabs too. Similar to the edge roughness I decided to leave these as a reminder of the materials involved. However, they could've been easily filled by just mixing up a small bit of concrete and then rubbing it in with your finger.
Step 15: Sanding the Concrete?
This might be the first time I’ve ever sanded concrete and surprisingly it sands pretty easily. I didn't want to sand it too much since I really loved the smooth texture of the concrete left from the forms, but a little bit of sanding was necessary to help the finish properly adhere to the concrete.
I sanded all the surfaces of the slabs using 220 grit sanding pads on my random orbital sander. And then using a soft sanding sponge, I very lightly broke all the hard edges.
At this point I thought I was clear to start applying the finish, but just to be safe I decided to double-check the instructions and it’s a good thing I did...
Step 16: Finishing the Concrete
As it turns out the minimum amount of time you want to wait before applying your finish is 96 hours after the initial casting. This is because concrete cures slowly over time and is constantly releasing moisture. If you seal the concrete before it has a chance to cure sufficiently you risk trapping all that moisture in the slab and impairing its strength.
So I went home and waited for another 24hrs before starting to apply the finish.
The finish I used is a 2 part polyurethane called Aquathane M35 and it's specifically formulated for applications on concrete that will live outside. Some polyurethanes (and other finishes) will yellow with UV exposure so you want to be careful what you use.
This is actually the first 2 part polyurethane I've ever seen, which was kind of neat. I mixed the A and B components together at a 4:1 ratio and then rolled it on using a little mini roller. Like I always do with any new-to-me finish, I started with the underside of the table to get a bit of practice run-in.
Once that dried I flipped the slabs over and did their tops. I did 2 coats up top and back rolled each coat perpendicular to the original application to help smooth out any nasty roller marks
Then it was just a matter of playing the waiting game until the satin finish dried.
Step 17: Attaching Felt Feet
Back at home, I had one last job left to do and that was attaching felt feet to the bottom of the legs.
I did this for two reasons. First, I don’t want these steel legs to scratch up the pavers on my terrace. And second I didn't want the pavers to scratch the paint off my steel legs and create a spot where rust can start forming
Makes sense right?
In order to attach the feet, I just used some self-tapping metal screws.
Step 18: Setting It Up and Enjoying It
Being that each one of these slabs weighed about 100 pounds, getting them home was no small feat. Luckily I managed to do it without throwing my back out and got them set up out on my terrace.....
Where it became immediately evident to me that my existing seating was quite lacking haha.
My plan is to build out this outdoor area with a couple of loungers as well as a couple of outdoor couches. So basically as soon as I dropped the table off, it was back to the shop to get cracking on my next couple of builds.
Step 19: Thanks for Reading!
Alright, that's it for this build everyone. Thank you for reading! I hope you enjoyed it, if you did you might want to check out my Instagram (Instagram.com/ZacBuilds/) and the aforementioned YouTube channel (youtube.com/zacbuilds) to see the rest of my builds.
If you REALLY liked this build and want to get ad-free early access to all of my builds as well as behind-the-scenes content, consider becoming a supporter on my Patreon. I'm trying to get enough patrons together so that I can afford to hire a video editor and create content faster. Hope you all have a wonderful day and I will see you in the next build!
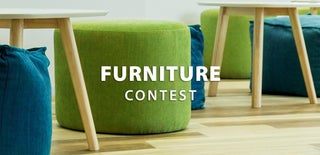
First Prize in the
Furniture Contest