Introduction: 1st Order Stormtrooper Helmet
Several months ago the the trailers for Episode VII were released, and a number of the new character designs were revealed, and what stood out for me were the redesigned Stormtroopers belonging to the 1st Order. I really wanted to make one, and fortunately some lovely 3D designers on the internet wanted them too and released a number of 'blueprints' for paper craft. I used the free files released by a 405th member Rundown for a base (not sure where to find the original anymore), and have strengthened it with fibreglass, sanded it down with car filler, and created a reusable mold using silicone products and cast a final product with plastic resin.
I planned on posting the whole process on here, so there are lots of pics to help you all out. I was able to get it done well before the premier night and was able to build a quick foam suit to were with it, I didn't originally plan on making a suit so I don't have many photos of that build process, but there are already several tutorials on this website on making cosplay with foam.
Edit: I realise that I've forgotten to put up sources for the Helmet and Suit files, here they are:
Helmet by a designer called Rundown: http://www.papercraftplaza.com/2015/10/02/stormtro...
Foam Suit: https://www.dropbox.com/s/gf4brbplc8qbmuo/EP7ST%20Foam%20PepMaster.zip?dl=0
Step 1: Supplies Needed
This is a somewhat lengthy process and to do it the way did you need a number of supplies. You need:
- A program called Pepakura Viewer/Designer. Basically it takes a 3D model, splits it up and formats it to be printed onto cardstock/paper (I used 140gsm paper). You can then cut out the individual pieces and glue them together with plain PVA glue. I used a file for the helmet done by a person called Rundown from the 405th forums, at the time it was the most accurate file available for free.
- Basic hobby glue, an Exacto knife and plenty of spare blades to cut everything out.
- Some safety supplies for when you are fibreglassing/sanding/painting everything up. I used some latex-free gloves (latex can mess with the silicone molding supplies), dust masks, and safety glasses. I also used a cheap rotary tool and a small 1/3 sheet palm sander to sand everything down and to dremel in details.
- Fibreglass resin, fibreglass matting or cloth (I found mat to be stronger but harder to apply neatly, and cloth the inverse), resin catalyst to cure, and car filler (often referred to as Bondo). The resin and fibreglass strengthens the paper model, and the car filler allows us to build up the outside shell, hiding the paper corners/edges and sand it down to a smooth surface. I went through a lot of car filler, sanding it from 80 grit to 600 grit sandpaper to get a good surface.
- Molding Silicone. I used some Australian brands called Pinkysil and CloneFX, the Pinkysil is very good for capturing details as it is very thin and runny, while the CloneFX goes on like a thick syrup allowing you to build up a thicker skin. These are both self releasing silicones, so I did not need a release agent but the 'industry standard' Smooth-On products may need one.
- Casting Material. I used another Australian brand called Easycast, fairly lighty weight and cures white to a Shore hardness of 73 (hard but a tiny bit flexible so it's not brittle)
- Paints. I just used some basic spray paints for the end, masking off certain parts for black and white. I did use lots of filler primer when sanding to close up some pinhole marks.
- Extra details. I bought a roll of thin PETG plastic to make the eye lenses (0.5mm thickness, super thin) and and some fabric dye to tint them.
Step 2: Building With Paper
This part is fairly easy, just a bit time consuming.
Basically to build a 3D object using paper I used a program called Pepakura, which imports 3D objects and converts them into smaller 2D shapes that can be printed onto paper sheets. You then cut up these pieces out and glue them together, which should created a final 3D shape. I ignored some of the smaller details on my build, as I was going to cover almost all of it up anyway and carve/cut out smaller details later on.
Step 3: Fibreglassing and Sanding
After lots of cutting, you should have a recognizable Stormtrooper helmet. Some people stop here and just have a thin paper helmet, but I wanted something awesome looking. The next step is to harden the inside, and you do this using fibreglass resin. Just take a small amount (I used 100ml batches) and add the required amount of catalyst to start the chemical reaction. Be warned, this gives off a toxic smell and is not safe for skin contact, so make sure you're using a mask/respirator and gloves, or at least in an open ventilated area to avoid fumes. I gave it 2 coats of resin so the paper was fairly stiff, and then mixed up something called 'Rondo'.
Rondo refers to mixing the resin and 'bondo' car filler to get a viscous liquid (more bondo means it's stronger but heavy, and more resin means lighter but more brittle), and if you add in the catalyst, pour it into the helmet and rotate it until it cures/hardens, you get a fairly thin, hard inner shell to work with instead of making a mess trying to fibreglassing small inner corners. I used this over a layer of fibreglass to give it extra strength, but you can do one or the other.
Once it's strengthened, you can apply the car filler to the outside. Doing small areas at a time, smear the filler on in thin coats until the entire helmet is covered. Don't worry if it looks bad, you'll be sanding 1/2 it off anyway. Give it a sand with some rough sandpaper and spray it with a primer. Keep repeating this until you have a smooth surface, using higher grit sandpaper every time. This part takes ages, and eventually you reach a point you're happy with it.
Now to cut out chunks of that smooth surface.
Step 4: Further Detailing
I got it all nice and smooth,and decided to ruin it...
I didn't like certain parts of the helmet (the cheek parts) and I needed to cut out various details, so I took a dremel and cut out various parts of it. The top holes are where the head clasps will go, and along the cheek the vents needed to be made. For the main cheek holes, I took some fibreglass and patched it up, sanded it down again and used clay to make them. For the top holes I took some scrap wood, cut and glue it into a 'puck' shape, covered it in petroleum jelly and held it in the hole while I smeared some more car filler. The petroleum stops the filler from sticking to the wood and hardens into the pocket shape. I cut out the small holes along the cheek, and saw I needed to build up the lip to be sharper with some filler, and generally fixed up various parts of the helmet.
Eventually you should get a final product seen above, and you could stop and paint it from here, but I want to be able to reproduce it. On to the molding process!
Step 5: Molding and Casting
[I've written about the Pinkysil, CloneFX and Easycast products in my previous instructable here, but I'll summarise it here. Note that these products are self-removing, as in they don't need a release agent, and I don't need a silicone thickening agent like Smooth-On might need. Research materials before using them.]
The Pinkysil silicone is a two part mix with a 1:1 ratio for volume, so pour equal parts and mix until it turns a light pink. It pours very thin, so simply pour it over your helmet and 'paint' it so it covers the whole surface (I wore some latex-free gloves and used my hands to smear it). Once the 'detail' coat is safe to touch (doesn't stick to your hand), you can apply the CloneFX. It goes on much thicker and works the same way, so its an equal volume mixture and layer it on about 2-4mm thick. Another thing to do it to stick on some registration keys, which are to help make sure the mold stays in the same place when inside the mothermold. I poured some Easycast into small mixing cups and attached the cured pucks onto the mold.
Once the mold is cured, take your plaster and start layering it on. I builds a small dividing wall down the middle of the helmet so the shell is easily removable, and I put the cloth on each side. Small tip, I use some clingwrap and put it between the two halves of the plaster shell to keep them separate, otherwise they stick together and defeats the purpose of the wall. Totally didn't learn that through experience, not that stupid... Once its dry, take everything off and you can remove the mold from the original master helmet. The mold can be removed 2 ways, either carefully peel off the entire mold as 1 piece (possible as the shape is fairly smooth and round, I did and it worked), or cut a jagged line up the back and peel it off (the jagged line makes sure everything lines up when you put it back in the mold).
Now we can cast it in resin. EasyCast is really easy to use, just mix it up in a 1:1 ratio and stir for 15 second or so (you should see the different coloured parts blend properly), and pour it into the silicone mold. Once poured in just keep rotating and swishing it around, getting into all the cracks and along the edges of the mask. Once it cures, keep doing thin coats until you think everything looks strong enough in certain parts. I did 3-4 coats and made sure everything was covered and the lip was fairly thick and strong before finishing it. Leave it for a couple of hours and you can remove the plastic cast, being careful not to rip the silicone mild. Mine came out fairly good, not that much needed to be cleaned up and I drilled out the eyes and certain parts, and gave it a decent sand over with some higher grits (180+).
Now you have a wearable blank helmet, time to paint and finish off the smaller pieces!
Step 6: Painting and Making Small Pieces
Time to finish off the helmet, it's only taken me 3 months on/off, you?
I worked on several things at once at this stage, so I'll explain smallest to largest. I needed to make the small clasps on the helmet top, so I took some scrap wood again and cut it into shape. I made a small mold using the Pinkysil and cast a dozen or so copies (the suit need several of them, only need 4 for the helmet). They came out off-white, so I sprayed them with a gloss white spray paint and super glued them into place.
The eye lenses were a bit tricky, as I hadn't done this type of thing before. I found a few decent tutorials online on how to do this, and tinting a flexible plastic called PETG seemed to be the best fit. I bought a cheap roll of 0.5mm PETG and some black fabric dye, cut out the plastic to size and used a heat gun to shape it to a 'bubble' lens (it thermoforms super easy, good material to work with). I then took the dye, mixed 2-3 packets in near boiling water, cooled it down until I could put my hand in it (still hot though), and submerged the plastic in it. I left it in for about a minute, took it out and quickly dunked in in cold ice water to lock the dye to the plastic. I repeated this until I was happy with how dark the lens was. Warning, the dye can stain the pot/bucket so use a cheap metal bucket to use to avoid ruining pots. The lenses were then cut down and glued over the eyes.
Finally painting is fairly straight forward. I used some acrylic paints (carbon black), masked off various parts and painted using a small brush. Some people use airbrushes or spray paint cans, I thought I would mess it up with them so I used a hand brush, but whatever works for you, works. There's a second helmet their are I sold one to a friend of mine for the premier, very happy with it.
Step 7: Done!
And there you have it, your very own stormtrooper. Now this one isn't 100% accurate, at the time the base file was 'accurate' to the trailer and you can buy/commission a more accurate file or even helmet, but for a cosplay or display piece it is pretty good. I had enough time to build a suit from foam as well, using the same principles as step 2, cut out the paper pieces, trace them onto EVA foam (I used 5mm and 10mm thick mats), glue them together with contact cement (hobby or hardware stores have it), painted them with thinned PVA glue to seal it (1/2 water 1/2 glue), and sprayed with white Plasti-dip. Everything was held together with elastic straps and velcro, and turned out pretty well.
The final suit was ready for the midnight premier, some friends got all dressed up as various characters as well (one worked as a prop builder for Episode 2 in Sydney) and the local news/radio were there to get some pictures as well, and everyone loved the photo op. Movie was fantastic by the way. Overall the helmet itself was a bit expensive to make this was, but with the mold you can technically make your money back by selling it if it's good enough. However I did make some expensive mistakes, my first mold was too thin and caved in when I tried casting (binned it) and I wasted some materials with experiments.
Hopefully you enjoyed this, and are well on your way to making your own helmet :) Merry Xmas!
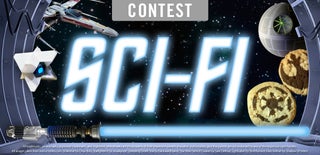
Fourth Prize in the
Sci-Fi Contest
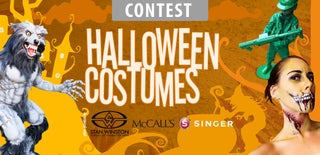
Participated in the
Halloween Costume Contest 2016