Introduction: Almost Free Router Table
Every woodworker should have a router table as they make countless operations with the router both easier and safer. Unfortunately commercial router tables are often expensive and of fairly mediocre quality. In this 'ible I show off the router table that I built for almost nothing from pieces of scrap I had lying around the house.
When I built this router table I wasn't taking photos as, to be honest, I didn't think it would turn out very well but after serving me well for two whole years I think it now deserves to be shown off to the world. I'm going to include a materials and tools list but to be honest you're unlikely to be able to build exactly what you see here, this is more to show you what can be done cheaply.
Materials
- Wardrobe base
- Cupboard door
- Side of a desk
- Scraps of MDF
- Solid wood laminate flooring
- 100mm drain connector
- 50mm drain pipe
- Bolts
- Screws
- Glue
- Silicon sealant
Tools
- Mitre saw
- Circular saw with track
- Screw driver
- Router
This project along with loads of others is also available at Wobblycogs Workshop.
Step 1: Drawings
The router table itself is essentially just a box with a fold down front but the fence so I don't think drawings are really necessary. The fence is a little more complex though so I've put together the diagrams above showing it's construction. The opening front fence is in green, the main back fence is in blue and the dust extraction is in yellow. The first image is exploded to show how the dust extraction port goes together.
I've given nominal dimensions for the components I used. In reality I just used the boards I had on hand but the dimensions given here would result in a good sized fence (perhaps a little large for many router tables - scale to fit your table).
Step 2: Base and Overview
The base is made from a free standing wardrobe that one of our neighbours gave us. In it's day it was probably a very nice wardrobe but it's day has long since passed and it was time it moved on. The wardrobe came as two pieces and I used only the base which comprised one large draw.
For the top of the router table I found I used a cabinet door (white) from a cupboard that was in the house when I bought it and the side of a desk (black) that I had when I was a kid. The cabinet door is 18mm ply with a high pressure laminate of some kind, perhaps melamine.
I took the sides, back and bottom off the draw and used the hinges from the wardrobe door to make it a drop down draw-door. It's important that the seal around the draw-door are reasonably good and so I fitted some small strips of wood along the top.
I also fitted a baffle in the middle of the void. This reduces the amount of volume that the extractor has to work with and means that I can use the other side of the router table for storage.
Step 3: Power
Looking at the side of the almost free router table you see the simple solution for getting power to the router. I simply drilled a hole in the side of the cupboard and fitted a hinged flap. The bottom of the flap has a small notch to allow the power cable to pass through. When under suction this flap is pulled so tight to the side it's impossible to open by hand so the seal is good. Ideally of course you'd have a zero volt release on the power but as my old dad always said: safety last.
Step 4: Inside and Dust Extraction
Inside the cabinet you can see the bottom of the router lift and the piles of dust that build up. This is what built up after a mammoth day of routing so it's really not a problem but I'd still look at fixing it if I was keeping this table long term. I've sealed all the corners with silicon to help prevent leaks although I don't think that was really necessary.
At the back of the cabinet you can see the dust extraction port, this is just a standard 100mm drainage connector. The four bolts hold on a strengthening plate which I'll show again later.
At the back of the almost free router table you can see the other side of the dust extraction set up. I bolted a 12mm ply plate to the back of the cupboard in order to strengthen it. The drain fitting is just a tight fit in the hole and held in place with more silicon sealant. The flexible host is simply pushed into the drain connector with a piece of rag looped around it. The seal isn't perfect but it's good enough for me.
Step 5: Fence System
The fence is the best bit of this table and the one part that may yet make it into my next router table.
The front section of the fence is made from a piece of solid oak laminate flooring. There is a hard smooth coating on it, probably polyurethane, which makes it easy to slide work pieces along. Being made up from multiple pieces there's little danger of warping and it's perfectly smooth.
The back half of the fence is made from scraps of MDF I had from other projects. Using the mitre saw I cut a number of accurate right angled triangles and used them to join two two straight sections together with glue and screws. I then cut slots in the front piece of MDF to accept bolts from the front fence.
At this point I realized I wanted some through the fence dust extraction so I cut some more right angle blocks and fitted a cover over them. I drilled a hole in the cover and inserted a piece of 50mm drain pipe and used silicon sealant to hold it in place.
At one end of the table I drilled a series of 8mm holes 50mm apart. I then drilled two 8mm holes 40mm apart at the corresponding end of the fence. Through one of the fence holes I in pushed an 8mm drill bit. This acts as a pivot point for the fence.
The white board of the router table overhangs the end of the cabinet about 30mm which is enough to allow me to clamp down the other end of the fence. The nice thing about this fence adjustment method is that you can get a very accurate adjustment very easily. Your accuracy in multiplied by the ratio of the distance from the pivot to the cutter and the pivot to the adjustment point.
I would be remiss if I didn't mention the one downside of the pivoting fence method - some operations that require the use of a t-track running parallel to the fence are difficult to perform. Having said that they can all be performed but in slightly different ways. In my case I've built a routing sled which I run along the fence. Since shooting this video I've actually fitted a t-track but I only use it for clamping on feather boards.
As seen on the back of the fence the front part of the fence is held on by bolts that fit into slots to allow the fence to open.
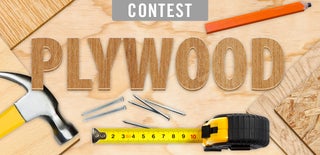
Participated in the
Plywood Contest
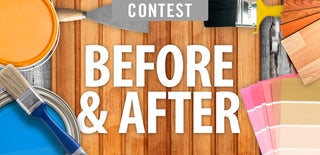
Participated in the
Before and After Contest 2016