Introduction: An Electric Violin
As an architect I find the process of making, particularly working with wood, extremely cathartic. In my day to day job, it may take years to see a building come to fruition, from a blank piece of paper... that's if it even gets built at all. When working with wood, one can see the results of ones labour instantly and in real time! Fantastic!!!
I am no craftsman, but I have dabbled in making musical instruments over the last 2 years. Mainly this is because these projects are:
1) Fun... subjective I know:
2) relatively quick, i.e. will not take me a year
3) A test of my abilities or lack there of & an opportunity to Learn new skills.
4) Small work, which will suit a very small working space.
5) Does not require BIG Machinery.
6) You get something to "play with" at the end
7) You get an excuse to buy new tools.
So get making :
This is not so much a how to: but more of an inspiration for how to make your own "how-to"!
Supplies
This is a guide only - anyone who takes on a project like this, will no doubt research to the hilt, these are the products that I used on this project, they are not an endorsement for the products, I am no Luthier, and I am certainly no violin player. All products available on Amazon.
TOOLS:
You are working with wood here, ideally you'll have the basics, a tenon saw, a mallet, a couple of chisels of varying width, a hand plane, screwdrivers etc.
The most specialist kit used on this, were a drill press and a bandsaw. The drill press, could easily be removed from the equation, with a cordless drill, and a Square. The bandsaw could be removed and replaced with a number of saw types & MORE elbow grease.
Dont Forget - Thin Mechanical Pencil & Steel Ruler.
The Wood:
Approx 1000mm(l) x 200mm(w)x~20(d) Maple**
Approx 1000mm(l) x 200mm(w)x~20(d) Mahogony**
** As this is an electric violin, the timber is not imperative (to my knowledge) at all - in fact much of this is superfluous decoration. As such, I chose two contrasting hardwoods... these could in fact be any species, I chose Maple and mahogany, as I had off-cuts from another project. Make no mistake - this is a project MADE FOR OFF-CUTS & Salvage. A table leg / table top / bed post etc... perfect!
The Bits & Bobs
Chin-rest Screws= 2Pcs Violin Chin-rest Screw - Sold By Seenheu ~3€
Brass Fine Tuners = Violin Tuners Adjuster,Alloy Violin Tuners Fine Adjuster for 4/4Violin - Sold by Bnineteenteam ~10€
Strings = Adagio Pro - Violin Strings - 4/4 Classic Silver Violin String Set / Pack With Ball Ends For Concert Tuning ~10€
Electric Violin Pick Up & PreAmp & batt Pack = Electric Violin Fiddle Silent EQ Piezo Pickup Preamp String Instrument Parts Black Sold by: Highly One ~15€
Peg Hole Reamer = ULTNICE Violin Peg Hole Reamer with Wood Handle, Sold by: Karminna ~15€ -Including in list of materials, as it's highly unlikely that you have one... & I feel the fit of the peg is important enough to justify it.
Nrpfell 4Pcs 4/4 Size Violin Fiddle Tuning Peg Set Jujube Wooden Replacement For 4/4 Size Violin
Sold by: Jo11nadab ~5€
Bridge Blanks = Violin Bridge By Zest x 2 Plain 4/4 ~4€
OPTIONAL
The Gauges - This is the cheap kit - that I used to copy my chinrest and Tail piece!! - Andoer® 4/4 Violin Chin Rest Chinrest with Tuning Peg Tailpiece Fine Tuner Tailgut Endpin Violin Accessory Kit Sold by: Mutell ~10€
Step 1: An Electric What?
Research, Research, Research :
I dont get a lot of free time, but when I mess around on my phone, when I take the train etc. I may just be thinking about my next project.
I may be watching youtube videos...
I may be reading forums... (not so much for this one...I dont think violin people like Electric violins!!)
I may be filling an Amazon basket with Bits and Pieces.
Interestingly, though I was making an electric Violin, most of my reading was about making real violins (definitely a project for another day). This just gave me the right vibe.
You Start with drawings :
You cannot build Musical Instruments without drawings, well at least I cannot!
Here I wasnt so much worried about the design, but of the technical stuff.. The scale length, the the distance from Nut to Bridge, the width of the fingerboard. Very important stuff to me, particularly as I do not play violin. I found a plan for a full size, known as 4/4 violin. I satisfied myself that this had all the dimensional information I needed.
If you're not familiar with printing out to a perfectly correct scale, I suggest, Autocad / Similar / Illustrator etc. a piece of software that you can scale, "measure" and print 1:1. I usually piece plans together from A4 or A3 with some "pritstick" or tape.
I dont know what precise plan I used as a base.. however If you simply google "violin plans" or "violin dimensions", you will find one. To my untrained eye, they are all fine, once you verify a few dimensions
..And you tweak your design :
Electric violins have components, a battery pack, an amp thingy, and inputs, and a pickup. Where are all of these going to fit. Well quite simply, it depends on what components you choose, and it depends on your design. Simply put an electric violin is a STICK. you just need to find somewhere within the STICK to fit the STUFF... and make sure that THINGY A, can connect to THINGY B. Simple.
Then you may or may not decide to stick some superflous stuff onto the STICK. You can see from the plan above, that I clearly have notions of "evoking the sense of a violin".
..And then you go back to your drawings:
Design is an iterative process. The art is in turning complexity into simplicity. How the heck would you make an electric violin... well its just a hell of a lot of small simple steps.
...And then you order the stuff :
...And then you wait :
Particularly for the electrical components - you want to get a size check on these before you start building anything. I can tell you, that the cheap electronics, I purchased, did not contain instructions, data sheets, nor were any available online, yet once you physically hold any componentry.. you get a feel for things.
...And then you take the obligatory photo, of all the "stuff" on your workbench : See above
...And then you start Building!!
Step 2: Making a "STICK"
As I Mentioned, an electric Violin, is just a glorified stick.
So Lets Make the Stick
Ok so my stick started out as a plank... but you could avoid this step completely, if you have a piece of timber suitably dimensioned.. genuinely 3x3 stock or a table leg, amy well make a good stick.
On the basis that hardwoods are more readily available in 18-20mm planks , and also this is more likely to be the type of timber that is laying around (as it was for me) - I simply laminated the plank together, so that it could handle the body of the electric violin.
CLAMP IT
The more clamps the better for this step. You want a good bond. with zero air gaps.
CLEAN IT UP
Now clean up the "stick", get the smell of maple shavings & feel like a big man with a plane. What we're doing here, is getting a decently flat surface for..
STICK ON YOUR PLAN & YOUR ELEVATION
See the last image above. I use spraymount to temporarily stick on my drawings to act as a cutting template. No scribing onto timber. Now for the tricky part.
Step 3: Cutting the Stick
Drill The Peg Holes
Before I cut anything, I drilled the Peghole guide holes, while the stick was still perfectly true and flat, to ensure best chance of holes being true. I undersized the peghole by ~1mm for the guides. Just enough to allow the tip of my "peg hole reamer - see supplies list" to fit in. We'll get to the peghole reamer at a later step.
I used a Drill press. I have an Aldi 69€ Drill press, which is tempremental, wobbly and lacks torque. Equally on could carefully do this with any drill, and usual efforts one takes to ensure right angle drilling... You just really dont want to skew these holes basically... so worth doing this early.
Cut the Stick out.
So here i used a Bandsaw... and I mean a small hobbyist bandsaw. (Charnwood W750 - A fine benchtop saw for this type of work) If you dont have access to a band saw, for a once in a lifetime cut, is it worth an hour or two of elbow grease with a coping saw -ABSOLUTLEY. Could you give it a shot with a jigsaw - Yes - Stay outside the lines - it will be fine.
So you cut out the "Elevation" first... and then cut out the plan... so you've basically roughed out the body of the violin.
Try to cut out in as close to a single cut as possible..ie. keep the offcut pieces as whole as possible. They are very useful later on to steady things, and assist in carving.
Make a Mistake
I naively tried to rough out more of the scroll than i should have - a band saw is no place to be roughing out something as delicate as a violin scroll - After we make mistakes, we dont start again, we adapt.
Step 4: Carving the Stick
Images above work backwards abit.
SCROLL CARVE
I made a complete mess of my scroll by taking away too much material during the roughing out. My challenge here was to carve something resembling a violin scroll, capturing the essence of it, with the constraints that I had. Here I started out with a half inch chisel, then a 1/4 inch chisel, and then mostly files and sand paper.
I just carved by eye, moving the piece around in various positions as I eyeballed it.
Now remember, to my knowedge, this is going to have no effect on the sound of the violin. The scroll could be redesigned to suit anyones skillset. It could even become a guitar style head, with guitar style tuners... again maybe for another day.
NECK SHAPE
Once the scroll, was thereabouts, I rounded off the underside of the neck with a 1/4 inch round router bit. (I have a KATSU Palm router - it seems to be based on the same Makita model) - I would genuinely just as easily and cleanly do this with a rasp and sandpaper. It is proably too finicky for a spokeshave.
Step 5: Hollowing Out
This was the step that worried me the most. There are two stages to it.
STAGE 1) HOLLOWING OUT THE PEG BOX
Now this is daunting chisel work, not for the fainthearted. First step is accurately marking out. For this type of work, I use a thin mechanical pencil. Once marked out & satisfied, I crosshatch out the waste, so there can be no confusion. After this, I used a Stanley Knife / Similar to deeply scribe around the visible edge of the peg box. This gives your chisel a haunch to live in, and to not go past.
Now a big concern of mine here, was the lack of support, for drilling and hammering and chiseling a fairly narrow piece of wood. Note: I have made a temporary support out of scrap plywood. A haunch of sorts, for the neck and scroll to sit into. This means you can drive a chisel a lot easier.
So to make this a bit easier, its obviously a good idea to drill out as much of the waste as you're comfortable with. Refer to the profile image. I taped some insulation tape to my drill bit.. my SHALL NOT PASS Point, and drilled away. No mistakes this time.
After that its gingerly cleaning up with a chisel. keep your chisel sharp. I found Maple quite nice to work with here, it takes a chisel well. I cut out thin strips of sandpaper, and used a file and a scalpel, and basically anything i could get in there to smooth it out, particularly the base. Just to note, the base is not particularly visible once the pegs are in place. But certainly worth treating this as "front of house".
STAGE 2) HOLLOWING OUT FOR ELECTRONICS
After doing stage 1, this part is simple. You will have marked up the placement of your electronics, using the actual kit, to draw around. - and start hollowing out for it. For this I used a suitably sized forstner bit, with more red tape as a depth stop. After this, the chisel simply tidied it up.
Step 6: Electronics Dry Fit
This is the point where I really tried to ensure that after all this, it was going to work. I also spent an amount of time, paring back the opening, cutting away a little bit more etc.
You will essentially need 3 chambers.
CHAMBER 1 (Connects to Chamber 2)
Battery Pack
CHAMBER 2 (Connects to Chamber 3&4)
Volume Controls
CHAMBER 3 (Connects to Chamber 2)
Inputs
CHAMBER 4 (The Tiniest Chamber - The Pickup Recess - Connects to Chamber 2)
Pickup
First, you need to check that each piece of kit, fits in its chamber. Next you need to ensure that the wires can get from chamber to chamber. You will have placed them as close as reasonably and aesthetically possible, during the early design process, noting that you always need to be thinking of "skew drilling" a hole from one chamber to another. I over-sized the connecting tunnels between the chambers as much as possible.
a) made it easier to thread the wire
b) I figured, the lighter this thing is the better... every little bit helps
AESTHETICS
Cheap or Expensive, this kind of stuff is usually ugly & plastic. I made a decision to put the plastic components on the base of the violin - out of sight out of mind.
1) A late addition to the design was a thin mahogany sole plate to the base of the violin. You'll see from the first picture, when i fit the battery pack, something just felt wrong about the base. This step obviously would have been better placed during the original glue up. Hence the importance of really thinking everything through, but part of the fun is also doing things on the fly.
2) The inputs for standard headphone & amp jacks : These were located on the side of the violin, the cover plate for these deserved to NOT be plastic. They are more visible, and more utilized. I used a thin piece of brass push plate from a door, cut out with a junior hacksaw, and shaped with a file, to create a new cover piece. Note for things like this, I discovered Step type drill bits to be fantastic.
3) For cutting the recesses for the pickup and the input cover plate, take extreme care. Basically, these were the only "chambers" where bad workmanship would be visible. I used a Dremel with 1/8" router bit, and a clamp on guide (2nd image) to get a perfect cut out, however- a thin chisel and Stanley knife would have done this also.
TURN IT ON
Oh yeah, you need to check that it actually works... In fact you should check the electronics, as soon as it comes out of its box. In this case, with the electric pickup, i satisfied myself that hearing a thud in the headphones, when I pressed it with my finger, meant that it worked.
Step 7: Fingerboard & Tailpiece
TAILPIECE
I understand that most luthiers buy these off shelf - there's nothing really to be gained by making this... except in my case there was.. The visual connection of the mahogany components were important, to the feel of the instrument.
I had to buy a tailpiece, to make a tailpiece. In this case, the cheapest one I could get. Examining it let me understand how to make it.
This was essentially a carving exercise.
1) Cut out shape on band-saw/scroll saw/coping saw etc.
2) Shape it - here i put a plane in a vice, and ran the piece of wood over it, to rough out the shape. The hollowing of the underbelly was done gingerly using a belt sander, and then a Dremmel with sanding drum. it was all over in maybe 10 minutes, before I had even started thinking about it... Maybe because I knew, that if it didn't work out, I had a shop bought back up. There's a little threaded nylon tail piece, that connects to a "button peg" at back of violin, this is required. I used the one that came with my cheapo tail piece, you can actually buy these individually also (Don't ask me the name of it, but if you google you will find!)
FINGERBOARD
This is where I cant get technical, suffice to say, this was "eye-balled" with a plane, and sanded until it felt right, and looked right. As far as I know mahogany is NOT a good material for a fingerboard, they are classically ebony, they need to be hard, to resist the metal strings digging into it.
If you are making this again, you need to make a call, you can buy perfectly good / better than you would make finger boards made of appropriate material, for very cheap.
For me, its about the challenge and the fun, I wanted to make as much as possible on this violin, sometimes, certain musical instruments can feel assembled rather than crafted,mainly "electric" instruments.
POP THE GRAIN
I cant wiping down, with some water, to get a momentary feel for what the finished article will look like.
Step 8: Making Wings
THE FUN PART
A feature of the design here, is the evocation of a violin, with some semi superfluous decorative wings. This is not an unusual design for an electric violin, and if anything, I've discovered, helps one use a standard shoulder rest with the violin.
Cut out
I screwed two pieces of timber together, so that i could cutout both sides at the same time, and ensure that they were perfect mirrors. Some of the curves are tricky, you'll see in the second image, the numerous relief cuts I made. There is a good bit of sanding in cleaning up the curves.
Notch The Body
Simple.. cut out notches in the body, so the wings can mortise in to the body. Be careful, get this perfect, again these are highly visible.
Router Time
I shaped the wings using a rounded router bit, taking my time, keeping the piece fully clamped, wearing goggles, cleaning every few minutes. This generates a lot of dust!! Take care to mark where the route should stop and start, where the wings mortise into the body. This is something that I didn't quite get perfect, and I find it incredibly annoying.
Sanding
I've had no training with anything, beyond YouTube. I end up with router burn oft times, you can see from the photos. These wings took a lot of sanding to clean up - I sanded from 80 through to 120 through to 240 grit. Resulting in smooth and organic shapes.
Step 9: Chin Rest
This is a step that is avoidable, should you wish to purchase a chin rest.
Again, partly for learning process, partly for aesthetics, I made the chin rest. But i did cheat a little, as I had to buy a chin rest, to copy it, in order to make it!! You can see it partly in the first photo!
I cut out the rough shape first, then essentially started to carve it away, mostly with files and sandpaper. I did use this as an excuse to buy a Spoon Gouge (see second photo) not essential, but great fun to use.
After that, its simply more sanding. Essentially I was matching the shop bought chin rest as close as possible, again I understand that real violin makers don't waste their time making these, when they can buy perfectly good ones.
Step 10: Assembly Part 1 : Forever Fixings
So, after painstakingly whittling each single element out of wood, using various methods.
You are left with:
A) THE BODY - OR THE STICK AS I CALLED IT
B) THE FINGERBOARD
C) THE TAILPIECE
D) THE CHIN-REST
E) THE "WINGS"
Throughout the process, it is psychologically impossible to avoid dry fitting everything together. You can see a musical instrument being made from nothing in front of your eyes - it's fantastic.
Part C & D - are pieces that can be added at the end, with non permanent fixings.
However, at this point the wings needed to attach to the body, likewise the fingerboard.
Prior to gluing up, I put one coat of shellac sanding sealer on the wings, and gave them a good rub down with fine grit paper.
I used 2 part epoxy resin (cheap dual tube stuff) to fix the wings. You'll see from the image that it was awkward to clamp these in place.
The finger board is tricky to glue on and clamp due to "glue-slide" - there are lots of ways around this, none of which I took, I simply fiddled around with the clamps until it was perfectly in place, and tightened. Note my clamps have some soft velcro on the pads. This is to avoid leaving marks on the timber.
Step 11: Finishing
A) This is as complicated or as simple as you make it.
B) The most difficult thing is to know when to stop.
I had a bottle of Rustins Sanding Sealer. Its not really used for finishing, I wanted this to be Glossy, as such I wanted to fill the pores... but guess what, I liked the look of it, and made a big decision... to leave it as is!
Really, I had no idea what I was doing. I did a lot of research on finishing violins, it is not an understatement to say it is an art. The best finishers, TEASE out a colour to the natural couloured maples and spruces. It's a beautiful thing.
Anyway, this is your Violin, so do what you will, but don't ruin all your hard work.
My biggest fear on a project like this, is that you'll apply a finish, and not be happy. That's why, TEST, TEST, TEST...keep your off-cuts & TEST.
Step 12: Assembly Part 2
So You've applied the finish, now its time to put all the bits and pieces together.
Some Notes:
The ELECTRICS
The easy part...we know everything fits, now that the violin has received it's finish, we simply screw the electrics in.
The TUNING PEGS
So it turns out, those Ebony Tuning Pegs I bought on Amazon were Not Ebony. - A black marker, turned them back into ebony once they were cut off. This is an important step & a step where it's possible to mess everything up.
I purchased a peg hole reamer. I reamed each hole turn by turn, test fitting after each one. I wanted an equal consistent length and spacing on the pegs, & I wanted the perfect friction fit. I am still fascinated as to how tuning pegs, stay in tune, relying only on friction.
So after all that, why didn't I make the tuning pegs.. It was just a bridge too far. If I was to make them, I would essentially have to make a paring tool, like a glorified pencil parer, to get that tapered peg just right.
No doubt lots of trial and error, and another couple of weeks.... At this point, your staring at a nearly complete violin, and maybe its time to just do it, its too damned exciting, not to put it all together.
The CHIN REST & TAIL PIECE
Easy peasy - Little brass adjustable fittings from the shopping list, will fit the chin rest perfectly. The tail piece, just fits onto another glorified tuning peg - fitted in the same way as above.
The BRIDGE & The NUT
Once could spend an eternity it seems learning about violin bridges. This is what transfers the sound from the strings into our electrical pickup. EVERYONE USES BRIDGE BLANKS - ABSOLUTELY EVERYONE - I could see no point starting from scratch with a jewelers saw on these. Bridge blanks require alot of working. Note: see my shopping list - be careful a lot of blanks have super curved feet for fitting on an arched violin top - This bridge sits on a flat Electrical Pickup - you will have to eyeball your blank, to ensure that if you flatten the feet, you will not remove too much material! The Bridge needs to be thinned out, and the kidneys and heart need paring back - I had no clue what I was doing - Just google " preparing a violin bridge" it is the science of precision.
The nut, here is a piece of Walnut off-cut, shaped with a file, the important thing is the 4 little recesses for the strings. One has to be super accurate - I used the corner of a very small triangular file, to make these V shaped divots in the nut.
The STRINGS
Fitting the Strings and Fitting the Bridge are symbiotic operations. One cannot fit the bridge without strings, and vice verse. I used the 2 outer strings, and their position above the finger board - from this you strike a line, to see how much material to remove from the top of the bridge, and just what type of asymmetrical arch to cut.
By the Way, using Brass Fine Tuners (See Shopping List) Made connecting the strings to the Tail Piece super easy. Not all violins use Fine Tuners, some use only on the highest string, but what do I know about it!
YOUTUBE, YOUTUBE, YOUTUBE, GOOGLE - When fitting strings. It is at this point, that the fact that I don't play violin, became a problem... What the hell was I doing?
Step 13: Epilogue : It Works
This project, from inception to completion, took me a couple of months of pottering around . Half hour here, half hour there. The idea with a hobby, is that you look forward to doing it, while some tasks are more chore like (sanding!) this is all about having fun, and an end product that you can be proud of. Working with Wood is Sensual in the most innocent sense. You can touch it, smell it and after 30 minutes of sanding, even with your mask on, you can taste it. You can see it turning from nothing into something, & depending on your project you can hear it.
I can HEAR the string vibrating through the maple bridge. I can hear the click of the tuning peg in its overtight hole... It's a wonderous thing.
Oh, and one more thing, to play a violin, you need a BOW! We forgot about it the whole time !
Luckily, my sister plays a little, and took this violin for a test run. This was an important part. Here I discovered.
a) I had strung up incorrectly - easy fix
b) bridge needed adjusting - a bit of reshaping of the top- easy fix - only really discoverable when playing.
Would I Ever make one again... NO WAY, lifes too short.
Would I Encourage someone to make one - of Course - lots of fun to be had, and lots to learn about a lot of things. Working with wood, finishing wood, types of wood, stringed instruments. Its relatively simple and could be a gateway into further adventures in luthierie.
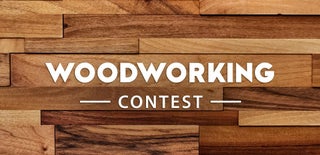
First Prize in the
Woodworking Contest