Introduction: Breathing New Life Into a Tired Old Toy Chest (And How to Refinish Wood)
The first piece of furniture my wife and I ever owned was this old used chest we picked up at a thrift store. Needless to say, we didn't have a ton of money at the time, needed a table of some sort, and for 25 bucks, this one worked perfect at the time for our small apartment!
Over the years, our taste in furniture has become slightly higher end, and while it had quite a bit of character, this chest has slowly become a bit of an eyesore in our living room, so had become delegated to being a toy chest for our son.
Well, he also no longer had any use for it, so I decided to see if I could make it "fit in" with our furniture, and was really pleased with the result. I thought for my first instructable, I would share the process, and maybe see what some of you could do with older items of your own!
Step 1: Tools & Supplies
Tools & supplies:
Protective Eyewear (always a must when working with wood, metal, or anything else in the shop!)
Respiratory Mask (needed for sanding, especially when getting all that old varnish off...)
Screwdriver (depending on your types of screws for the hardware, you may have need of different bits)
Rotary Sander
Sanding Block
Sanding discs and paper - 80 grit, 120-150 grit, 220 grit
Bench Grinder with either a sponge sanding disc or a wire brush disc
Power drill with wire brush insert
Sponge Brush
Latex gloves (makes for easier cleanup)
Stripping scraper
Painters rags
Paint stripper
Varathane Gel Stain (your choice of colour)
Varathane Triple Thick clear finish
Varathane wood conditioner
Tack Cloth
Step 2: Prep Time!
Tools and supplies: Screwdriver, and if needed, scraping tool
Using your screw driver, remove all hardware from your item. In my case, some of the hardware was actually stuck to the wood from years of things being spilled on the chest, rust, etc...
Step 3: Stripping!
Tools and supplies used: Paint stripper, scraper
So, I didn't realize how much shellac had been used on the trunk prior to getting it cleaned to bare wood, and skipped this step just going right to the sanding. After going through about four sanding discs, and having them keep clogging up, I realized my mistake, and got out the paint stripper. WAY easier!
This stuff can be a little noxious though, so a) be careful not to get it on your skin, it will burn! and b) use that respiratory mask (a painters mask will still help if you don't have one of these on hand or the cash to get one)
Cover all surface areas with old stain or shellac with about a dime's thickness of the paint stripper, and let sit in a shaded area for about 10-15 minutes. When you start to see it bubbling, it's doing its work.
Using a scraper, scrape the entire piece clean. For those hard to reach areas, a stripping sponge or hard bristle brush works well.
Step 4: Time to Get Dusty!
Tools and supplies Used: Rotary Sander, 80 Grit sanding disc, 80 Grit paper, Sponge sanding block
Once the paint/stain/varnish/shellac has been removed and the item is wiped clean, you'll still have a slightly stained piece. You'll want to still get the wood as naked as possible so that when you're applying the fresh stain later, you'll have a more even coat. In the case of wood, stripping isn't always the best way to get get naked, you'll need to rub it down as well!
This is probably the most time consuming part of the whole process. WEAR YOUR MASK!!! If you're breathing in all those dust particles, it can make for a very sore set of lungs, and even lead to future problems as well.
Start our with your rotary sander and an 80 grit disc to get all of the flat areas of your piece. This item in particular had years of wear and tear, so some areas needed a lot more attention than others. If you haven't sanded before, the lower grits are best to get through that wear, as well as removing any residual stain or otherwise. The higher grits are for smoothing out the lifted fibers of the wood, and getting it ready for finishing.
For those harder to reach areas, or rounded corners, use a piece of 80 grit sand paper and either just your hands or s sponge backed sanding block to get into those areas.
Step 5: Movin on Up!
We're not done with the sanding yet! Now it's time to get that surface nice and smooth... Still using your rotary sander for the flat areas, and either your hands or a sponge block for those hard to reach areas, start moving up your sand paper grits from 80, up to either 120 or 150, and then finally 220. Once you're finished the entire piece, giver a dust off with the palm of your hand, and it should feel baby smooth.
If you have rougher hands like me, use the back of your hand over the entire piece (it's a little more sensitive than your palms) to detect any spots you may have missed smoothing out the surface. If you find a rough patch, just use a few swipes of your higher grit sand paper to smooth it out.
Step 6: Don't Eat the Glue...
Now it's time to fix any of those joints that have become separate by age. If you noticed any parts of your piece that may have come unglued, or there is a loose joint, you'll want to fix those at this point.
Using wood glue, (I used a woodworkers syringe) squeeze some glue into the cracks in the joints. Once all joints are glued, clamp the joints for long enough to let the glue cure. Mine takes a short time before I could continue, so I was able to get started back on the project a couple of hours later...
Step 7: Conditioning... Makes It Oh So Soft
Tools & Materials: Painters rag or sponge, gloves & wood conditioner
Now it's time to condition your wood. With most woods, especially pine, when stain is applied they can turn out somewhat blotchy or spotty. Also, the end grain (where your wood has been cut and the cut surface shows) will tend to soak up more stain than your long grain (the smooth surface of the wood). One tip is to sand those end grains with a higher grit sandpaper than the rest of the item, or if you mix up a little polyurethane with some mineral spirits (about half and half), you can apply that to the end grain as well prior to conditioning or staining. If you have a good conditioner, however, it helps quite a bit as well.
First rub the conditioner over the entire item. Let sit for a couple of minutes, and then wipe off any excess to allow it to soak into the wood. Then, within 15 minutes, start applying stain (if you're not applying stain within that timeframe, wait until you are, as the conditioner won't have it's full effect).
Step 8: Lets Get Messy!
Tools and supplies: Tack Cloth, Applicator rag (painters rag), wipe off rag (for excess stain) and gloves
I like a gel stain, as it tends to give you a more even coat. It also tends not to soak into the wood as much, so if you do somehow make a mistake and need to go back to sanding, it doesn't take as much effort to clean up the wood again.
Here, I used Verathane Espresso stain. The main reason we like this colour is that we have very light finishings to most of our home, and the contrast of a dark furniture with the lighter colours makes for a very nice contrast throughout our home. You obviously may have a different choice of colour stain, but the instructions will work the same. With this one in particular, it only needed one coat.
First, Glove up! Stain can be a pain (see what I did there?) to get out from under fingernails, and off skin, etc. so gloves are the "handiest" solution. Second, ensure your item is clean of dust and particles. I like to use a tack cloth, (they cost about a buck a piece) as they will get every particle on an item, even in the nooks and crannies. Next, stir your stain (you should never really shake a stain anyways, but even so, you'd have a hard time shaking up a gel stain) for about 3-5 minutes to ensure that it is evenly mixed. You're now ready for application!
If you have a large piece like mine, it's usually easiest to concentrate on one side at a time. Begin by balling up the rag you're using for application, dip in your stain, and then begin applying to your item by rubbing the stain across the grain of the wood. Let the stain sit on your wood for about 2-4 minutes so that it has a chance to soak in evenly, and then using the other rag, wipe off the excess stain, again ensuring you're wiping with the grain. If you do see a darker spot here and there, wipe a little harder, as this is most likely excess stain that you didn't get off in the first pass.
Repeat this process to all sides. Now, sit back, relax, and let the stain dry. If you do need another coat, wait for about 2-4 hours before applying. You're starting to see the final product! Looks good, doesn't it? Now your stain should set for about 24 hrs to ensure full dryness before applying a top coat of protectant. I know you're excited to apply, but if you don't let it cure fully, your top coat could peel or lift, and that's the last thing you want after so much effort, right?
Step 9: Mmmmm, Shiny!
Tools and supplies: Verathane triple thick clear finish, Sponge Brush, gloves (just in case), spray bottle with mineral water, 600 grit wet/dry sandpaper, sponge sanding block.
It's hard to imagine your piece looking any nicer, but trust me, that top coat will do the trick! Myself, I prefer to go with a semi-gloss rather than a high gloss for a variety of reasons, but I tend to think that looks the nicest finished. Unless you're working on an item that demands a high gloss finish like a guitar, a piano, or you just like to see your face looking back at you on every surface, then this is the way to go. A satin finish can also be nice, it just depends on your preference. This was actually my first time trying out the Verathane triple thick clear finish, and I was very pleased both in the application, and the result.
First, Glove up! more for your own sake then the item, but any kind of finish is never nice to get stuck on your hands. Next, again, give your entire piece a wipe with a tack cloth. Don't worry if you see a little stain on the tack cloth, it's just literally getting all surface excess and dust off before applying your finish. Dust is your enemy here, (so try for a dust free work area for application) and can give you a nasty look to your finish. Plus if you're picky, you don't want to have to go back and start over, but I will give you another trick...
Now, stir the Verathane thoroughly, and finally, start your application! Dipping the sponge brush into the Verathane, don't get too much on it, as we all have a tendency to want to wipe off the excess on the side of the can. This can create bubbles in the coat you're putting on, and if not fixed immediately, can ruin your finish later on. Now, a side at a time, apply a thin coat of the finish to the entirety of the piece applying "with" the grain. If you can't tell whether the finish has been applied, use a light to see if the surface looks wet. Do not touch with your fingers, as this will blemish the piece.
Once the entire piece has been coated, sit back and relax while it has a chance to dry. Regardless of what the instructions on the can said, this finish actually drys very quickly, and I found a second coat could be applied within an hour or two with no poor effect.
Once the piece is dry, regardless of how careful you were you may notice a couple of rough spots. That's what the wet/dry 600 grit sandpaper is for. Give the rough area a quick spray with the mineral water, and using the 600 grit sandpaper and sponge block, LIGHTLY go over the rough spot a couple of passes. You'll notice that the water will take on a milky appearance. This is the finish coming up, but not to worry, you'll be putting more on. Thoroughly dry the area, and then give another wipe with the tack cloth to remove any dust left behind. Now you're ready for another coat of Verathane. I typically like to apply at least 3 coats to ensure the piece has a nicely protected surface.
Now let the finish cure for about 24-48 hours before handling. Although it may appear dry, it still needs this time to cure in a dust free area.
Step 10: Onto the Hardware
Tools and supplies: Protective eyewear, Bench grinder with sponge sanding disk, drill and wire brush drill attachment
This chest in particular had some awesome hardware that was on it, including iron strap hinges, a decorative lock plate, swing hasp and decorative handles. When I removed them in the beginning, I noticed that they had a fair amount of rust and gunk in behind where they were on the surface, so I decide to clean them up a bit. While I was doing this, I noticed the brushed steel look that was coming up on them, and thought that it might look pretty cool as a contrast to the dark finish on the chest. So, rather than painting them black again, I decided to leave the look of the brushed steel.
Lets get started. Turning on your grinder with the sponge sanding disc attached, on a diagonal line move each piece of hardware across the spinning sponge to remove any rust/paint gunk. Make sure that you are moving it across the same line of movement no matter where on the piece you are cleaning/polishing, otherwise, the brush lines look a little off. You'll want a consistent brush line across the surface. BE CAREFUL! If you haven't used a grinder before, rubbing one of your fingers across the surface while it's spinning is not a nice feeling.
Once you've removed as much as you can from all of the pieces, turn to your drill and wire brush attachment to get into the more difficult areas you couldn't reach with your grinder.
I was extremely pleased with how these came up!
Step 11: Reassembly (no Batteries Required)
Tools and supplies: Screwdriver, original screws and hardware
Now that you're item is dry, and your finals are polished, reassemble. Then sit back, and admire your handiwork.
I've got to say, I was really happy with how this entire project turned out. It now fits in with our entire home, and looks right out of a magazine. It has a bit of an antique flair, but has received a ton of comments just in the last week that we've had it in our living room.
I hope this inspires you to try your own item, or to save a dingy one from the scrapyard. If you do, don't forget to use a coaster!
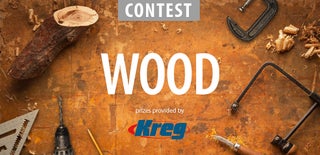
Participated in the
Wood Contest 2016
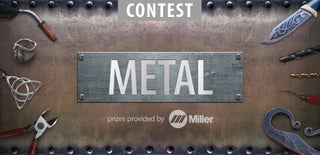
Participated in the
Metal Contest 2016