Introduction: Cordless Tool, How to Replace Nickel Cadmium by Lithium Ion
Screwdrivers, and just any other battery tool, has been produced for many years. Therefore, in the hands of users, a large amount of old batteries accumulated, as well as a dead weight of a tool sometimes accumulated. There are several ways of solving this problem:
1. Simply repair the battery, i.e. replacement of old elements with new ones.
2. Remaking from the battery to the main power, up to the installation of the power supply in the battery compartment.
3. Replacement of nickel-cadmium and nickel-metal hydride by lithium.
The first option for sure many have already passed, as well as me. It gives a result, although in the case of a branded tool it is often worse than it was originally. The price goes a little cheaper, for labor is easier and significantly.
The second option also has the right to life, especially if the work is at home and reluctant to spend money on replacing batteries.
The third option is the most laborious, but it allows to significantly improve the performance characteristics of the instrument. This is an increase in the capacity of the battery and the lack of a "memory effect", and sometimes an increase in power. But apart from the laboriousness there is a side effect, lithium batteries work a little worse in the frost. Batteries are of different design, although in general they have much in common, therefore I will tell, and at the same time show the example of one of the representatives of this category, the Bosch PSR 12 VE-2 screwdriver. The screwdriver is quite good, there is a spindle lock, two speeds, therefore it makes sense to remodel.
Step 1: What Will We Work With
It so happened that the battery packs were even three, but we will rework one, I'll leave one for another review :)
By the way, the batteries are different, but both for 12 volts, capacity 1.2Ah, respectively 14.4 Wh.
Step 2: Disassembling an Old Battery
Batteries are disassembled in different ways, but most often the case is twisted with a few screws.
Although I came across variants both on snaps and glued.In any case, you will see something like this inside.
In this case, the assembly of 10 nickel-cadmium batteries, with the usual use of batteries of the same size, but their laying may sometimes differ. In the photo one of the most common options, 9 pieces at the bottom and one in the vertical part.
Step 3: Choice of New Batteries
The first thing is to choose batteries for replacement. The power tool uses batteries designed for a large discharge current.
I briefly made a review of different batteries, at the end of which I brought a sign that could help in this matter, but if you are not sure, just find the documentation for the batteries that you plan to buy.
Step 4: I Recommend
For example, I recommend these types: For a powerful power tool - Samsung INR18650-25R, US18650VTC4, Liitokala INR26650-50A For medium power tools - LGDBHG21865, LGDBHE41865, Samsung INR18650-30Q
It should be remembered that often the claimed capacity of the battery is inversely proportional to the maximum current given. Those. the more battery current is calculated, the less capacity it has. The example is certainly rather conditional, but very close to reality.
For example, very capacious Panasonic batteries NCR18650B for power tools are not suitable, since their maximum current is only 6.8 amperes, the screwdriver also consumes 15-40 amperes.
Step 5: I Do Not Recommend
And now what can not be applied: Batteries shown in the photo, as well as all sorts of Ultrafire, MegaFire, as well as any 18650 with a declared capacity of 100500mAh.
In addition, I strongly do not recommend using old batteries from laptop batteries.
Firstly, they are not designed for such a current, and secondly, they are likely to have a wide range of characteristics. And not only in capacity, but also in internal resistance. It's better to use them somewhere else, for example, in the PowerBank to charge your smartphone.
Step 6:
Alternative, model batteries, for example for boats, squats, cars, etc. It is possible to apply, but I would prefer the usual 18650 or 26650 and the type of the presence of a strong case, as well as a more real replacement in the future. 18650 and 26650 to buy easily, and model can be removed from sale, replacing them with batteries of another form factor.
Step 7: Selecting the Battery Type for Replacement
But among other things, remember that you can not use batteries of different capacities. And in general it is desirable to use accumulators from one batch having bought immediately the necessary quantity (ideally +1 in reserve, if all the same fall across different).
Those. if you have 2 batteries on the shelf for a year and then you buy a pair of new ones and connect them consistently, then this is an extra chance to get problems and balancing here already can not help, not to mention batteries with initially different capacities.
For reworking the battery of this screwdriver, the LGDBHG21865 batteries were selected. Screwdriver is not very powerful, therefore I think that there should not be any problems. Batteries are designed for a long discharge current of 20 amperes, when choosing batteries, you should find the corresponding line in the battery documentation and see what current is indicated there.
Step 8: How Many Batteries Do I Need?
Lithium batteries have a noticeably higher capacity with smaller dimensions than cadmium batteries. In the photo on the left, the assembly 10.8V 3Ach (32Wh), to the right is native, 12V 1.2Ah (14.4Wh).
When choosing a number of required battery replacement should be guided by the fact that the conventionally one lithium (LiIon, LiPol) replaces conventional 3 pieces. In a 12 volt battery it costs 10 pieces, because usually they are changed to 3 pieces of lithium.
You can put 4 pieces, but the tool will work with overload and there may be situations when it can suffer. If you have a 18 volt battery, then there are probably 15 ordinary batteries, which change to 5 lithium batteries, but this tool is less common.
Or speaking in plain language,
2-3 NiCd = 1 lithium,
5-6-7 NiCd = 2 lithium,
8-9-10 NiCd = 3 lithium,
11-12-13 NiCd = 4 lithium
etc.
Step 9: Note
Before assembling, it is necessary to check the capacity of the batteries, because even in one batch the batteries may have a scatter, and the worse the manufacturer, the greater the dispersion.
After that, you should fully charge all the batteries to equalize their charge.
Step 10: How to Connect to Batteries
Battery connection.
To connect the batteries, several solutions are used:
1. Cassettes
2. Soldering
3. Spot welding.
1. The cassette is very simple and affordable, but is strictly not recommended for high currents, since it has a high contact resistance.
2. Soldering. It has a right to life, I do it myself sometimes, but this method has nuances. At least you have to be able to solder. And be able to solder correctly, and most importantly - quickly. In addition, you must have a suitable soldering iron. The soldering process is as follows: We clean the contact place, cover this place with flux (I use F3), take the tinned wire (better not a very large cross section, 0.75mm is enough), we pick up a lot of solder on the soldering iron tip, touch the wire and press it together with it battery contact. Either we apply the wire to the place of soldering and touch the place between the wire and the battery with a soldering tip with a large drop of solder.
But as I wrote above, the method has nuances, you need a powerful soldering iron with a massive sting. The battery has a large heat capacity and with a slight sting the temperature will drop sharply so that the solder "freezes", sometimes together with the sting (depends on the soldering iron). You will long try to warm up the place of contact and overheat the battery.
Therefore they take a soldering iron with a large copper tip, preferably well heated, then only the soldering site will be warmed up and after the heat it will simply be distributed and the overall temperature will not be very high. The problems concern the negative output of the battery, with the soldering of the plus one there are usually no difficulties, it is easier, but I also do not strongly overheat it. In any case, if you have no experience of soldering, then I do not recommend this method.
3. The most correct way is spot welding, instantaneously, without overheating. But the welding machine must be properly tuned in order not to make a through hole in the bottom of the battery, so it's best to contact the professionals. Alternatively, in some online stores a service is offered (rather, lots, with or without petals) for welding contact lugs, this is not very expensive, but much safer than soldering. The photo shows that a rag insulator is laid between the petal and the battery case. This is important, because without it you can overheat the petal and it will melt the insulation of the battery, I think the consequences are clear.
Step 11: Note
Attentive readers probably noticed incomprehensible plastic spacers between the batteries.This solution belongs to the class - how to do it right.
The tool is subject to vibration in the work and the situation of insulation damage between banks is possible (I did not see this, but theoretically). Installing spacers excludes this situation. You can not put, but it's more correct.
Step 12: Wire Connection
Then it is necessary to output the wires for connection to the protection board and the terminal block. For power wires I use a wire with a cross section of at least 1.5mm, and for less loaded circuits 0.5mm.
Of course you will ask why the wire is 0.5mm if there is no current and you can apply a much thinner wire. The wire of greater cross-section has thicker insulation and provides greater mechanical strength, i.e. it is more difficult to damage. Of course you can use any wire, I just showed the option, which I think is more correct. Ideally, the wires first zaludit on both sides, and loose ends isolate, but this is possible with the second rework of the same battery, when the length of the wires is already known. For the first, I usually take wires with a margin.
Step 13: Wire Connection 2
If you look closely, there are holes in the upper terminals of the battery on the upper photo, this is also done to increase the reliability of the connection.
The wire is inserted into the hole and sealed, in this case there is less risk of getting a bad contact. In general, solder wires, at the same time it is desirable to additionally isolate the terminals using a heat shrink tube.
As a result, we will get such an assembly. Two wires go from the positive terminal, this is due to the connection feature of the protection board.
Step 14: Wire Connection 3
The last step in preparing the assembly is rather desirable than mandatory. Since the assembly is "live", it is necessary to fix the elements relative to each other.
For this I use a shrink tube, although in this case it is more correct - a pipe. It is rather thin, but very solid, its purpose is to squeeze the whole structure.We put on heat shrinkage and with the help of a hair dryer we seat it.
The usual option with a cigarette lighter probably will not work, as it is desirable to do this evenly. In toga, we have a factory battery assembly, in appearance.
Step 15: Does Our Battery Fit Into the Case?
We try the battery in the case. In general, of course, usually it's done first, I somehow forgot this moment, but I think it's quite logical :)
Step 16: How to Fix the Battery in the Case.
Then follows the stage of installing the assembly in the battery compartment. Trivial at first glance, the operation conceals a small pitfalls.
First, we wash away the dust and dirt from the compartment. I made a mistake and wiped only the bottom part, the rest then scrubbed with a brush and fleece. Because it's easier to wash with soap and dry it.
Next, gluing the assembly. In the original version, the batteries were simply squeezed by the halves of the case, but in our case this is rarely possible, because assemblies are most often glued. Here as before, there are several options, consider them.
1. Double-sided adhesive tape
2. Hot melt glue
3. Silicone sealant
4. Nail through nails, and on the reverse side bend. :)
Since the latter option is more suitable for fans of extreme sports, I'll paint more "mundane".
1. Very simple and convenient, but since the contact point is small, it does not hold very well, but in addition you need to use a good scotch tape.
2. The variant is good, I sometimes use it myself (by the way, I use black hot-melt glue). But in this case would not advise. The fact is that hot melt has the property of "swimming" when heated. For this it is enough to forget the screwdriver in the summer on the street and get a battery dangling in the end. I will not say that this will be necessary, but this property has a glue, a fact. In addition, the hot melt adhesive does not stick very well to the massive elements and can simply fall off when loaded.
3. In my opinion the most convenient option. The sealant is not afraid of heating, does not flow with time and has good adhesion to most materials. In addition, it is quite elastic and does not lose its elasticity with time.
I used Ceresite sanitary sealant. In the photo, it may seem that he is hardly smeared, it is not, sealant is quite a lot. By the way, it should be borne in mind that most sealants do not glue to the previous layer of sealant. In addition, you can use a similar mounting adhesive in the same tubes, for example "Moment", but silicone seems to me more suitable.
In general, we apply a sealant, insert our assembly, press it and leave it to dry.
Step 17: Protection Board.
This board is designed to connect three batteries and has a declared operating current of 20 amperes.
Only now, I noticed that the board has a rather high threshold of over-voltage protection, 4.325 Volts. Maybe I'm wrong, but I think it's better than 4.25-4.27. It is also indicated that the current of 20 Amps is the maximum long-time, the overcurrent tripping current is 52 Amps.
The plate is very similar to the plates from other boards, so I will highlight some important points.
1. The balancing current, since this board does not know how to do this, here the dash
2. Maximum continuous current, for most applications it is necessary to 20-25 Amperes. On a less powerful tool is enough and 15-20, more powerful will require 25-35 or more.
3. The maximum voltage on the element at which the card disconnects the battery. Depends on the type of batteries used.
4. The minimum voltage on the element at which the board will disconnect the load. 2.5 Volts is quite small, it is better to choose this parameter the same as stated in the data on the battery.
5. The current at which the overload protection is triggered. Do not strive for transcendental values. Although this current is directly related to the maximum worker, there are usually no problems here. Even if the protection has worked, it is usually enough to simply release the screwdriver button and then press again.
6. This item is responsible for the automatic reset of the protection operation.
7. Resistance of power transistors, the smaller, the better.
Step 18: Features of the Protection Boards
'll tell you more about the protection boards.
To begin with I will answer the question - but can it be without a protection fee? No.
The protection board at least provides shutdown during overload, this is harmful both for the batteries and for the tool.
In addition, the board protects against overcharging and overdischarge. It can be said that the overdischarge can be felt by the drop in power, but this does not apply to all instruments, but in addition one can get into a situation where one element is very "tired" and the voltage on it drops very sharply. In this case, it is easy to obtain a reverse polarity, i.e. the battery is not just completely discharged, and through it will pass the current in reverse polarity. This effect is obtained only when the elements are connected in series and for some reason it is often forgotten.
Lithium batteries are very dangerous and a protection card is mandatory for them!
The boards are basically divided into two types (although in fact there are more of them), with the possibility of balancing and without. I'll explain what balancing is and why it is needed at all.
First, the option of "passive" balancing.
This option is used on the vast majority of motherboards as the easiest to implement. As the battery reaches the threshold voltage, it begins to load on a resistor, which takes over a portion of the charging current. While this battery "fights", others can recharge to their maximum.
1. One of the batteries is either charged more than others, or has a slightly smaller capacity.
2. In the case of a simple charge, the voltage on it will be higher than the rest
3. The balancer draws a portion of the charge current, not allowing the voltage to rise above the maximum.
4. As a result, all the batteries are charged evenly. The more, the better.
The second version of the balance bar, "active". It has a very different implementation and is not suitable for working with large charge currents. Its task is always to maintain the same tension on the elements. It works by the principle of "pumping" energy from a battery with a high voltage in the battery with a smaller one.
Step 19: What Are the Boards With Built-in Balancing.
We got a little distracted.
A balancing board usually contains several large SMD resistors, the number of which is a multiple of the number of channels. at 3 channels it is 3 or 6.
On them it is more often written that that of type - 470, 510, 101, etc. On the left board 4 channels, on the right - 3 channels.
Step 20: Boards Without the Possibility of Auto-balancing
There is no balance here, but there are current-measuring shunts in the form of SMD resistors with low resistance. They are usually written R010, R005.
Therefore, the board with the balance bar and without can be distinguished in appearance. By the way, the boards may not have a current-measuring shunt. This does not always mean that the board does not know how to measure current.
Simply, sometimes the controller is able to use as a "shunt" field-effect transistors.
Step 21: Separate Boards for Balancing the Batteries
There are also separate balancer boards, as well as balancer kits + protection board. This option is fully entitled to life, if satisfied with the price, but there will be more wires.
Step 22: Boards With Built-in Charger
I often find confusion about the possibility of using these cards as a charger. People usually mislead the word Charge in indicating the lot.
These cards do not know how to control the charge, they only protect the batteries. But the illiteracy of sellers or the curve of the translation does its job and people continue to make mistakes.
But there are also "all-in-one" boards, although they are not designed for high currents and are not suitable for power tools.
Step 23: Description of Protection Board and Components
On this board there are eight key transistors, or more precisely four pairs. Applied transistors AOD514 and AOD4132 they respectively have a resistance and a maximum current of 5.9 mΩ 46 amperes and 4 mΩ 85 amperes.
On the left is a current-measuring shunt. This option is more preferable than SMD resistors, which sometimes have the property of "burn out" due to large impulse currents.
Transistors on the boards are installed in pairs for a reason. The fact is that powerful field-effect transistors have a "parasitic" diode in their composition and to disconnect the current in both directions they must be put two. In this case, two transistors give a total resistance of 10 mΩ (5.9 + 4) and a maximum current of 46 amperes (considered the weakest).
But since there are four pairs of transistors, it turns out - 2.5 mΩ and 180 amperes, which is very good for such a motherboard.
Step 24: Description of Protection Board and Components 2
The board does not have a central controller and is assembled on rather primitive circuitry, channel voltage monitors and further the scheme reducing everything to the control of FETs. It's simple, but it works. Although probably now I would have chosen something more "advanced". In addition, the board does not have a balance bar.
You ask, like so, because I wrote above about the advantages of the balance bar. The balance is good, and I recommend buying boards with it.
But I also think that normally-selected batteries in the balance beam do not need much, from a strong fall, it will not save, but problems can add. There were cases when a defective balance rocker disembarked the battery. In addition, most manufacturers of power tools do not put balancers in their battery packs.
In addition, the board has contacts for connecting the temperature sensor (and above in the photo from another store there is an example of such a card with a temperature sensor).
Thermal sensor is good and in my plans to figure out how to connect the native temperature sensor of the screwdriver battery. Presumably it is necessary to drop the RT resistor, replace the resistor RY by the nominal value corresponding to the new sensor's rating, and solder the new sensor to the RK contacts.
Step 25: Mounting the Board
Since the board can heat up during operation (although not very much), I decided to make a gasket to protect the batteries from excess heat. In addition, it will protect the batteries in the event of a rupture of the FETs and through-passing the board (this happens, but extremely rarely, therefore, rather, theoretically).
I took the edge of the fiberglass and removed the foil.
Then, using the same silicone sealant, glued the gasket to the battery assembly, and then glued the board itself. The design is of course terrible, but in this case it is the simplest and most reliable solution.
Step 26: Connecting the Board
The connection scheme was on the store page, but in fact it is practically the same as the connection schemes of the other boards. The accumulators are in series, minus to the board, the first middle point counting from the minus is B1 +, the second is B2 +, the third is B3 +.
But since there are only three batteries, B3 + is the plus of the entire assembly. The second wire from the positive terminal goes to the load. The negative line of the load (as well as the charging wire) is connected to a separate contact of the board.
Step 27: Connecting the Board 2
Then we connect the wires. The order of connecting the wires can be critical, I usually connect first the minus of the assembly, then the plus, and only then the midpoints starting from the minus pin (B1, B2, etc.).
There is information that the wrong connection sequence can burn the controller, I wanted to add to the review, but did not find any references. In addition, we need to solder very carefully, so as not to close the contacts, otherwise there will be a sad picture.
Perhaps this is one of the most difficult, for a beginner, stages in the rework . I first cover the pad with a solder pad, and then solder, so it's easier. Ideally, the wires are then fixed with a sealant so that they do not hang.
Step 28: Locking the Terminal Block
Before connecting, you should consider locking the terminal block. Initially, it was kept by batteries, but since there are no batteries, it will have to improvise.
For fixing, I measured the inside width of the protruding part, and then cut out a piece of plastic of the appropriate width. The truth is still a little lost and cut out a little less, I had to reel off the tape :)
Usually, both wires are soldered off, but in my case, the negative wire was long enough and I did not remove it, but replaced only the positive one. By the way, since the terminal block is made of plastic, and the terminals themselves are quite massive, here either we apply the same principle as when soldering the batteries, or simply bite off the old wire 7-10 mm from the end of the terminal and solder a new wire to it.
The second option is not worse, but much easier.
Step 29: Locking the Terminal Block 2
1. Solder the plus wire assembly to the terminal board. Heat shrinkage is rather perfectionism, there is nowhere to go short, but I wanted it neatly.
2. We insert the terminal block into its native place, we hammer (or very strongly press) the plastic retainer, which I cut out above.
Step 30: Connection of the Terminal Block
Solder the negative lead from the terminal to the board and cover the board with a protective varnish. But the latter is no longer perfectionism, but quite a useful thing, since the board is under voltage and can be operated in conditions of high humidity.
If you do not cover the board with varnish, corrosion of the open parts of the tracks and the leads of the components is possible. I use the lacquer Plastic 70.
Step 31: Final Assembly
On this with the battery everything, we put the springs back, fixators and collect in a pile. Beforehand it's better to turn over the whole structure and tear out anything that could accidentally get inside, I had it cut off the wire insulation.
At the same time, you can wipe / lubricate the mechanism of fixing the battery in the screwdriver.
The rework has been completed, the battery is working, but since the native charger has not yet been reworked, it has connected it to the laboratory power unit.
I built the power supply myself, I can also publish how I made it.
Step 32: How Can I Charge.
For charging, you can certainly use a common charger type Imax. But I consider this option uncomfortable. In addition, the connector for balancing the screwdriver batteries is sometimes output. The thing is certainly useful, but as for me, it's a little extra, and besides it's not always safe.
In my opinion, it's enough to just pick up the batteries once and then just charge it without balancing. Either buy a protection board with a balance, and sticking out the connectors is an increase in the chance to short them, break it, and this is more likely an option for a home.
Step 33: How Can I Charge 2
For a more realistic application, it is better to either alter the native charger, or completely replace its "stuffing".
The first option is technically complicated, since the lithium battery charging algorithm differs markedly from the cadmium battery, and besides some native chargers and call it the language does not rotate, only the transformer, the diode bridge and the heel of the parts inside, there is no control at all.
For example, Bosch also has an "advanced" version, with a controller.
Step 34: How Can I Charge 3
As a second option, you can use the native transformer of the charger, its diode bridge and a piece of PCB as a terminal block.
For rework it is necessary to buy a board of the type such as in the photo. Or any other that can stabilize the voltage and current. Usually these boards have at least two trim resistors. But in this case, even three, the third adjusts the threshold for the indication of the end of the charge.
If the photo, then the first - the voltage, the second - the indication, the third - the charge current.
Step 35: How Can I Charge 4
You can also use other cards, for sure many of them have seen in the expanses of Aliexpress.
The first is simpler, only the current and voltage are regulated, the charge indication is fixed, the LED goes out when the current falls below 1/10 of the set charging current (standard lithium charging algorithm).
The second as a matter of fact as the first, but in more "advanced" variant, the battery voltage and a current of its charge are displayed.
Step 36: How Can I Charge 5
All the above options use the native transformer of the charger, but if it does not, the converter simply needs to be supplemented with a power supply unit, for example. but it is worth considering that the PSU should be at a voltage higher than the end of the battery charge, the difference is about 3-5 Volts or more.
Those. in this case 15 volt PSU is not suitable, but usually such power supplies have an output voltage adjustment of ± 20% and can be slightly raised.
But you can just buy a 24 volt power supply and do not adjust anything.
Step 37: How Can I Charge 6
If you only have a 12 volt power supply, and you need to charge the battery as in the review, then you can use a universal converter, for example, this one, though, and it costs more.
Step 38: What Can Be Improved
You can add an indication of the battery charge, for example, sound or sound + light.
Either measure the voltage with a small voltmeter, or even put a hybrid voltmeter + sound.
Step 39: Another Option for Improvement
Personally I prefer simple options, voltage measurement with indication of several LEDs.
And the last option I already did.
Step 40: As I Like.
Almost the same option is used in one of my screwdrivers, or rather in its batteries. Such a display option is very convenient to use.
Step 41: Well, What Does It Ultimately Work? Working!
A short video of the result of the rework. The video shows that in severe cases, protection occurs. The battery was already a little discharged, therefore in the protection mode at the second speed the protection did not always work.
With a fully charged battery, this happens more often. But it also shows that the protection is triggered correctly, load, shutdown.
After that I release the button, press again and the screwdriver works.
Step 42: More Questions?
A few useful links.
1. The protection board that I used is a link, the price is about 9 dollars
2. Batteries that are well suited for such applications.
I apologize for my very bad english. Perhaps the article is not all clear, my native language is Russian, but I tried.If you do not understand something, ask me, I will be happy to answer all your questions.
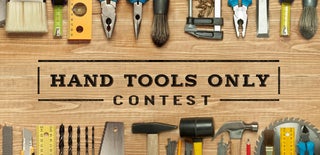
Participated in the
Hand Tools Only Contest 2017