Introduction: Improving a Small Engraver
Today I will try to tell about the completion of my small machine and increase the speed of its work.
Step 1: Introduction
Not long ago I was talking about buying and assembling a small engraver.
But he had some problems that I wanted to fix.
And today I want to tell you about how I finished this engraver and what I used for this.
Reference to the first part of the review - Link
Step 2: Lead Screws
Three pieces were ordered, the diameter of all the same, 8mm, but the length is different, a pair of 200mm and one 100mm.
There are three nuts, respectively, in the set for the propellers, so the whole set looks like this.
Step 3: Lead Screws Part 2
Previously, I believed that running shafts with rectangular carving are the simplest form of transmission in small machines, but practice has shown that they occupy roughly the average position between the screws with ordinary thread and the ball screw (ball screw drive).
By the way about the ball screw, in my opinion this is the best option for CNC machines, but unfortunately the most expensive one. Here, a threaded screw with a complicated thread shape is used, in addition, it is usually polished in addition, since it is part of a linear bearing.
At the same time, the nut also has a return mechanism through which the balls return to the beginning of the path to close the cycle.
Step 4: Lead Screws Part 3
In motion it looks more clearly.
Step 5: Lead Screws Part 4
It is worth mentioning, for the transfer of rotary motion to the progressive, not only the screw gear is used, but also the gear, but this variant is even less common in small machines. Gear requires a more powerful engine, but can also provide greater speed.
Step 6: Lead Screws Part 5
So in reality looks like a screw with a rectangular thread.
The set was provided with the corresponding nuts with holes for fixation on the mechanism.
Step 7: Lead Screws Part 6
In the photo you can see the difference between a conventional threaded stud, which was before the conversion and a special screw, I think the difference is visible to the naked eye.
Step 8: Couplings
Also in the last review, I complained that the usual coupling was used to connect the motor shaft and the spindle.On the one hand, this has its advantages, which I will discuss below, but there is also a big minus, for normal operation, it is required to accurately observe the alignment of the motor shaft and the spindle. The slightest discrepancy slowly breaks the fasteners and the hairpin climbs.
On one of the axes I did not manage to do it normally, I had to reel in a bit of scotch.
Step 9: Couplings Part 2
There are other ratios of diameters from 3х3 to 10х10 including intermediate variants.But it is worth considering that in my case the diameter of the shaft corresponded to the diameter of the thread, by and large it is not right, the shanks should be without thread, but that was what
I ordered.Just when picking up the kit, then be careful.
Step 10: Couplings Part 3
There are four types of couplings:
Tough
Such a coupling has a low price, great reliability and the ability to transfer a large torque, but does not completely compensate for misalignment.
Spiral
At its core is a spring, has an average cost, can compensate for a large misalignment, but it can not transmit a large torque, more fragile and because of the springing properties can increase the play and cause resonance phenomena.
Cam
It can transmit a rather large torque, but the coaxiality compensates for the worse spiral, and there is also the possibility of wear of the shock absorber.
Membrane
Compensation of a large misalignment and at the same time the possibility of transferring a large torque, but unfortunately the highest price.
Step 11: Couplings Part 4
Initially, until industrialized couplings were available, even used self-made, manufactured from improvised materials, for example a piece of high-pressure hose. Such variants are quite viable, but not technologically and less durable.
Step 12: Couplings Part 5
I ordered one clutch per engine, as I decided to remake all the axles.These couplings are spiral, it can be seen that in fact it is a spring.
For the first time I "met" with such a clutch when I was building a 3D printer and was somewhat surprised that it bends :)
Step 13: Bearing
In the original version, the free end of the running shafts was simply suspended in the air, this was permissible with rigid couplings, but completely unacceptable with spiral ones.As I wrote above, the spiral coupling is a rigid spring in its design.
This property gives a parasitic effect - backlash.
If you do not fix the end of the shaft, then you can move it within +/- 2-3mm, which is very much and will bring to nothing all efforts to improve the design.
To fix the shafts, bearings were ordered, reference to the product, price $ 4.20.
Step 14: Bearing Part 2
Such bearings are of different designs, with a through hole and a deaf, and also the options of attachment to the base. I decided to order a version with a through hole diameter of 8mm.
In my case, 8mm is the diameter of the drive shaft, if the shaft has a shank, then the diameter of the hole must match the diameter of the shank.Closed bearings are installed, therefore, dust is not threatened to them within reasonable limits.There are two screws with which the shaft fixes.
At the test it was found out, that completely backlash they do not clean, though and reduce it almost to zero.I'm not an expert, but I think that the bearing design for such an application should be somewhat different, since they are more designed for a different mode of operation, rather than a stubborn one, as used here.
But in any case it is much better than nothing.
Step 15: Improvement of the Machine
All three sets as they will be installed on the machine.
Now you can proceed to the improvement process.
Step 16: Improvement of the Machine Part 2
First I took off the shaft that moves the table. The photo shows what was and what is planned to be delivered.
Also a comparative photo of old and new couplings.
Step 17: Improvement of the Machine Part 3
Nuts.
Here I will stay a little longer.
As I showed in the previous review, plastic nuts were used, two pieces per axle, and they were separated by a silicone washer.
This design is short-lived, but provides almost zero backlash, and relatively cheap. Initially, there was a thought of replacing plastic nuts with metal nuts, but I decided that then the shafts would start to wear out. And although I was given three spare nuts in the kit, I decided that replacing the entire kit would be a more correct solution.
Step 18: Improvement of the Machine Part 4
The fact is that the play in the helical gear is almost an inevitable evil, therefore, it is reduced in many ways, for example by means of a special design and the use of additional springs.
Or use a split nut, which is essentially an analog of the two nuts that came with the engraver. In this case, the nut is tightened by an additional screw, and the play is reduced. The truth at the same time, we must remember two things, the more we tighten, the less the play, but more is needed to twist the mechanism and more wear nuts.
Step 19: Improvement of the Machine Part 5
In this case, I decided to leave for now as it is and do not pay attention to a slight backlash, maybe later I'll finish it.
New running shafts were slightly longer than native ones, 199 against 189mm, but in this case it is not critical.
Step 20: Improvement of the Machine Part 6
Started working off the table, as with the lightest object for rework. He cursed very much, because to put the nut, it was necessary to ream the hole. But not only to drill, but to slightly increase the diameter already manually. Drilled a diameter of 10mm (real 9.9), and the nut has an outer diameter of about 10.2.
Step 21: Improvement of the Machine Part 7
The most difficult part of the work, to install the nut, especially since the table was in the way. The previous nut was cut from one side.
Step 22: Improvement of the Machine Part 8
With the help of a multitool I cut out a piece of the table :) Then I unscrewed the front part and marked the fixing holes under the nut. The nut has four mounting holes, but due to the fact that the previous one had three holes, however hard it tried, it was possible to fix it only by three. By and large there would be enough and two, maybe even it would be better, but decided to strengthen it by three.
Step 23: Improvement of the Machine Part 9
Judging by the design, the nut should be inserted into the hole in a long part, but I decided differently, now it "looks" inside.As you know, this was done for a reason.
So I slightly increased the stroke along this axis.
Step 24: Improvement of the Machine Part 10
With the muffle of problems, no problems arose, removed the old one, exposed and screwed a new one.
The fact is that the motor shaft has a flatten, i.e. it is cut a little bit along the length, it is necessary to fix it so that the screws do not fall on this place.
Step 25: Improvement of the Machine Part 11
I tried the bearing, although the shaft is longer than the previous one, but it turned out to be the best, the additional length was just on the arm, the shaft must be fixed in the bearing.
In general, initially there was a thought of increasing the diameter of the hole to install the bearing, but it was so large that the size began to extend beyond the metal frame on which it was mounted.
Just in case, I increased the diameter of the hole under the shaft from 8 to 10mm.
Step 26: Improvement of the Machine Part 12
Then everything went standard.
I drilled a hole for the shaft.
Marked mounting holes, for this you must necessarily fit the table as close to the bearing as possible, so that the shaft is exposed to the necessary position.
Drill a couple of holes with a diameter of 3.2mm, cut the thread 4mm. We expose the bearing so that it does not interfere with the rotation of the shaft, tighten the fasteners. Native holes have a diameter of 5 mm, but I decided to set aside a place for maneuver, so it's more convenient.
At the end, fix the shaft with the screws of the bearing itself.
Step 27: Improvement of the Machine Part 13
But then everything went simultaneously and is simple and difficult. Simply, because I already almost imagined what I would do, but it is difficult, because for this I had to disassemble part of the machine.
But since before that I tried to do everything neatly, I had to do some of the work without disconnecting the wires. Sometimes the engine has a connector, then it's easier, but I could only disconnect the spindle motor.
Step 28: Improvement of the Machine Part 14
Next, he reworked the axis, which moves the mechanism to the left / right, here everything went as well as with the axis of the table, just a little easier.
Step 29: Improvement of the Machine Part 15
Along the way, I picked up the Z-axis engine to increase the stroke, and the new lead screw was also longer than the old one.
Raised with the help of racks from the kit to some kind of motherboard.
Step 30: Improvement of the Machine Part 16
And then he stepped on the rake. Received misalignment along the X axis, and so strong that even the coupling did not help. When fixing the shaft, it turned very hard.
I again had to disassemble everything, grind the pad under the nut and collect it back.
Step 31: Improvement of the Machine Part 17
The X-axis bearing was no problem, just like on the axis of the table.
Step 32: Improvement of the Machine Part 18
But with a Z axis came out a small overlay. Here I also wanted to get the maximum move, but I did not think that the bearing could interfere with the machined part. In addition, even with the rise of the engine at 5mm, I still have the lead screw much longer than necessary.
The second lining was that for some reason the hole for the coupling was made with a diameter of 20 mm (the clutch itself has a diameter of 19 mm), and along the X and Y axes, the hole was 22 mm, so the clutch entered literally "to zero" ... The cone drill helped, I could not think of a hole from 20 to 22mm, it turned out to be very convenient.
Already then I decided, if I interfere, I'll sip. In the photo, the Z-axis mechanism is not in the lowest position, but raised by about 10 mm.
Step 33: Improvement of the Machine Part 19
But when I installed the milling cutter, I found that everything is fine, especially since I plan to replace the cartridge, and then it will be more important for me to have a power reserve, not down.As a result, such a design came out, of course, too, not an ideal.
But in my opinion it is much better than it was. After the assembly, only the lead screw of the "head" drive was lubricated, the rest is better not to lubricate, as the dust will stick and eventually it will only get worse.
Step 34: The Software Part.
On this "hardware" rework of the machine was completed and I moved to the "soft" part of the project. But here a small surprise was waiting for me. Turned all at once and even without problems, if not for one nuance.
For some reason I thought that speed should increase by 2 times, and it grew 8 times!
Even in the process of inspection and alteration, I noticed that the thread is applied four-blade, this is clearly seen if you look at the end of the screw. In the photo you can see the four beginnings of thread turns.
Step 35: The Software Part 2
Just in case, I'll explain. Four-thread is a multi-threaded thread. Conventional screws and, correspondingly, nuts have a single-threaded thread, i.e. the whole thread goes like one thread. At multi-threaded threads it turns out as if at once several "threads". This solution allows you to make a large thread step while retaining great strength, since there are several turns in the clutch at once.
Step 36: The Software Part 3
It turns out that the old screw had 8 times less feed speed, although at the same time it had 8 times the feed force at the constant applied torque. It turned out slowly, but strongly. In the last review, I complained that the machine is very slow. True, except for an eight-fold deceleration due to the other thread pitch, I also had a two-fold slowdown due to the fact that the stepper motors have a step of 0.9 degrees against the more common ones with a step of 1.8 degrees.
In the photo, you can see how many turns of the old screw thread are on one turn of the new one.
But the old screw had one more advantage, it did not really need the braking mode of the shaft, it was possible to move the mechanism only by the engine, because of the small step, it would not work without moving the shaft.
Step 37: The Software Part 4
On this, as it were, in general terms and everything, a small demonstration video of the work after the alteration.
Step 38: The Software Part 5
You can also see how it worked before the alteration.
Step 39: The Software Part 6
Screenshot in the process of work. For the test, I took a demo file from the PCB engraving program.
Step 40: The Software Part 7
Photo result. Here one can see one of the problems of engraving. The slightest unevenness leads to too deep incision or vice versa, to the passage above the workpiece. And this I tested on a piece of laminated chipboard, which is very smooth, unlike fiberglass. Those. the material must be prepared very carefully. For example, when trimming with scissors, the fiberglass is deformed and aligned with the same problem. But the minigraver is great for drilling boards, though at the same time you need to replace the cartridge with a normal one, but this is in the future.
Step 41: The Software Part 8
The photo is closer. The cutter was not very sharp, therefore, the cutting edges are visible at the top left. In addition, the tip of the milling cutter should go to zero, in my case it was not quite so. But the milling of the boards is also not suitable in all cases. If you make a board of any low-voltage device, then everything will be fine.
But if you plan to make a device with a high voltage, then there may be problems, and if a galvanic isolation is required, it is better to etch the board, since the breakdown between the ranges is dangerous.
Step 42: Finish
And now that you finally got me.
Positive - Increased freewheel speed, higher reliability.
Of the negative - Noticeably more noise, though small, but looser, less traction.
References to used parts.
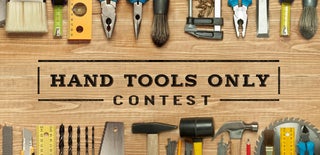
Participated in the
Hand Tools Only Contest 2017
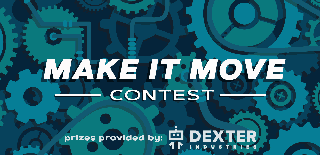
Participated in the
Make It Move Contest 2017