Introduction: Crutch Holder Project
Hi all,
I am a passionate tinkerer and DIYer, and having bought a 3D printer not too long ago, I wanted to use it to help the people around me! My grandmother suffers from arthritis and has to use walking sticks to get around, and I often saw her really struggling to pick her crutches up off the floor, because they kept slipping off the table or counter she had been resting them on.
I decided I wanted to help her, because it often causes her a lot of pain to bend down and pick them up, especially due to her arthritis. After looking on the market for existing crutch holders and testing many different products, I kept finding problems, and all of them seemed to be either very fragile or very difficult to use. I decided that I wanted to design and make a solid and reliable product that would be able to grip onto any kind of table or counter and hold the crutch firmly in place.
One of my main design considerations was that the design be both quick and easy to use, as these were some of the main shortcomings of the designs that I had tested. I also had to make sure that the design required minimal force to operate, because arthritis sufferers such as my grandmother often have trouble squeezing and gripping objects. After multiple tests (and many failed attempts) I decided on having the crutch holder fixed to the crutch pole, because during testing, it came out as the most user friendly position.
I have tried to make the design as 3D printable as possible, ensuring that not many other supplies are needed, and I have designed it so that all the pieces can be printed using a standard 200mm-200mm-200mm printer with plenty of room to spare. The crutch holder is compatible with most types of crutches, as it has a hinge which means it can be attached to crutch poles with different diameters. The crutch holder also uses a spring loaded mechanism, which allows for quick and easy use, and one of the main advantages of the mechanism is that it allows the user to attach their crutch to the table in under 5 seconds. It also works with many different types and widths of table.
Supplies
-Black or grey 3D printing filament( I recommend AMZ3d as they are relatively cheap and of good quality, and are readily available on amazon)
-Neoprene adhesive sheet(this was the one I used - https://www.amazon.co.uk/ADHESIVE-BACKED-NEOPRENE-SPONGE-RUBBER/dp/B00IKMR5H6 )
-4x small 5mm diameter steel balls, to be used as ball bearings( I had some lying about at home, but can be found here https://www.amazon.co.uk/Chrome-Steel-Ball-Bearings-Pack/dp/B002SRVV74 or elsewhere very easily)
-Small black or coloured elastics(loom bands perfectly good)
-1 tube of super glue(I recommend Loctite)
Step 1: Printing the Parts
First, you must 3D print all of the necessary parts. For those new or less confident using 3D printers, you must first download a slicer software(I use Ultimaker Cura, as it is free and easy to use) and then set up your printer on Cura. Once this is done open and position the .stl files and position them on the print bed. They can be printed at 10% or 20% infill to save plastic, and can be printed at a speed of 60mm/s, however you may need to adjust these settings depending on the type of printer you are using(I usually use 20% infill as I find print strength and quality is greatly increased in comparison to 10%). I often use a skirt(a thin line going around the model) as a border, in order to get the filament flowing out of the nozzle, however this is not strictly necessary. I would recommend using a heated build plate if possible, because this increases the chance that the bottom layer will be well printed and it allows the print to properly adhere to the build plate.
Once printed(this may take a while, granted!), remove any supports with a pair of thin plyers, and check the model to ensure that it has no structural defects. Try and sand down the model where supports may have caused the plastic to sag somewhat, especially around the hinge as this will need to move with relative ease. Also make sure you remove all of the supports around the ball bearing sockets, as these need to be clean for the ball bearings to move smoothly.
Note - When printing the cover.stl piece, make sure that you print it at 100% infill or the piece may not be as strong as needed, especially for the rod used in the hinge.
Step 2: Foam Cutting
First off I would like to explain what the purpose of the foam is:
While performing tests on the product, I kept encountering a common problem with all of my tests - How will my product successfully grip the surface of the table? After my fair share of failed attempts, I settled on adhesive backed Neoprene foam, because not only was it cheap and readily available, but because it was also, quite simply, the material that performed best in all of my tests!
In order to cut the foam, I used two methods; Laser cutting and plain old scissors:
For the laser cutting, I created a template on 2D design which I then exported to a .dxf file(one that a laser cutter can read). However, in order to get the cut right with the right depth(without burning the foam too much), I had to conduct several tests (to know what speed and power to use for the laser). This is very important, as it means you will get a nice clean cut if you use the right settings(I used speed 20, power 30). Once this is done, use the .dxf file provided and cut out your main shapes. These shapes can also be done with scissors by tracing around the model and cutting around the line, however I found it quite fiddly, because the adhesive back kept sticking to the scissors on the curved lines.
The scissors are used to cut small strips which will be stuck to the inside "clamp"(the part which secures the device to the crutch using the hinge).This can be done with a ruler and a good pair of eyes, as well as a bit of trial and error.
Step 3: Spring Mechanism
Mechanism: When I first started out with ideas on how to create this product, I assumed that finding the main mechanism in order to raise and lower the platform clamps would be easy. How wrong I was! Throughout the course of my trials, I went through 38 different versions of the product, and I still think that there is a lot of room for improvement!
In the end, I settled for a spring loaded mechanism. It uses ridges in the central mast (the long part that moves up and down) in order to "lock" the piece into place in regular increments.
For the spring, I broke apart 2 click pens and removed the springs from the tips. I then trimmed my 2 springs to roughly 2.5 cm each (though this is an approximate measurement).
After that, I used the 2 printed pieces(2 x rotary spring moving.stl) and inserted them into the desired positions(make sure that they slide easily in these positions, and if not, sand down the sides of the moving parts).
Next, I put the springs in to the spaces, and put the central mast in as well( bear in mind that as the cover is not on yet, and if you try to move things, the springs could jump out!).
Note - I have included a picture of one of my tests for the spring mechanism, as well as a video of one of my earlier prototypes. These are just examples of what is going on to make the mechanism understandable.
Attachments
Step 4: Sticking and Glueing
Hopefully up to here you're doing ok, so now it's time to put most of the model together.
First off, put the two hinge parts together and check that they fit properly and smoothly.
Now this is where the cover.stl piece comes in; First, position the springs and the rotary spring moving. stl parts in the correct positions (they should just about hold their positions without the central moving part present).
Now place the hinge in the right place. Now, you will notice that the cover.stl has a rod in the centre. This has to go through the hole in the hinge. Place the cover on the hinge and over the rest of the piece so that it covers the springs and the rod goes through the hinge pieces. whilst holding the cover firmly down with a thumb, check that the hinge works properly.
If you feel confident that it works, go ahead and apply some cyanoacrylate glue(superglue) to the underside and stick it down. Remember to let it set for at least 5 mins or more depending on the type bought.Make sure not to get any glue near the springs because the glue could stop the design from properly functioning.
Now you can test the spring mechanism. Place the central clamping part into the trapezium hole and move it up and down. It should work much like the video of the red prototype on the spring mechanism step, with the product going up and down in regular increments.
Now for the neoprene rubber! this part if relatively easy, however you only have one shot at it, so make it count. First, carefully peel off the adhesive backing on your cut out parts until you are left with the neoprene and a sticky coating on the back of it. Now carefully stick it to the 3D printed parts, and press it down firmly once done. remember to do so for all 4 pieces- The top and bottom of the table grip and the insides of the hinge clamp.
Step 5: Ball Bearings
I decided to use ball bearing in order to have the model slide smoothly up and down when adjusting to the width of clamp desired. After trying many different options, I chose to have them in a cavity in the central clamping part .stl.
In order to insert them you must have all the other steps completed (apart from sticking the cap on). Remember that you may have to sand the ball bearing rectangle part sightly for it to slide smoothly up and down.
First, insert the bottom 2 bearings into the bottom two sockets, and hold them in place with 2 fingers. Then, slowly, lower this bottom half into the top opening of the central clamping part .stl. Then, repeat the same process with the other 2 top bearings.
Check that the model part can slide up and down (all the springs and the cover should be on at this point!). The model should move up and down in increments (due to the springs) and should slide relatively smoothly. Now, you can glue the cap on at the top with cyanoacrylate glue (superglue).This stops the slider from escaping!
Step 6: How to Use
All made! Now all you need to do it to learn how to use it (Them, as you'll need 1 crutch holder for each crutch). In fact, it's very simple; all you need to do, once all the glue is dry, is:
First attach it to the crutch. All you have to do is decide on the height you want the product to be fixed to on your crutch, and simply clip the hinge around that spot. Then you can use the small elastics (doubled up for strength) to secure the grip by slipping the elastics into the keyholes on either side and thus hold the entire contraption to the crutch.
All you need to do now is clip your crutch to a table. As long as you can reach the top and the bottom of the surface, it should work! All you need to do is press down on the central column(where the cap.stl was stuck) to open the "jaws" of the clamp, and then simply squeeze slightly from the bottom and top sides to close the jaws again. The beauty of this system is that it can be used by people with arthritis, like my grandmother, as it requires minimal force to operate, unlike many other such devices.
I find helping people using design extremely rewarding, and hope to continue helping people this way. My grandmother now uses this system regularly, and is very pleased with it!
Thanks so much for reading and happy making!
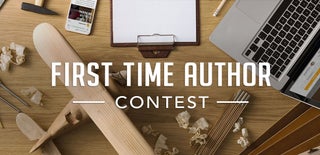
Participated in the
First Time Author Contest