Introduction: Water Drop Epoxy Lights
Hi, I'm a passionate 16 year old tinkerer, and I love creating designs that make people happy, so this design was for my sister, who loves fairy lights!
The design is inspired by the humble water droplet, with the goal of bringing a bit of nature to brighten up the home. I intentionally tried to incorporate bubbles into the epoxy in order to make the light feel warmer with more diffuse scattering of light rays.
Supplies
You will need:
-a string of fairy lights( I got mine here - https://www.amazon.co.uk/Shatchi-6226-LED-BATTERY-... )
-3D printer & printing filament( I tend to use AMZ3D PLA as they are quite cheap and make good quality filament)
-Clear Epoxy(roughly 25 ml resin + hardener for each waterdrop you wish to make)
-silicone rubber(i used polycraft rubber, link here- https://www.amazon.co.uk/Polycraft-GP-3481F-Silico... )
-rubber bands & blu tack
Step 1: 3D Printing the Droplet
To make the droplet, you will want to print the glass.stl file twice, and then stick the two 3D printed halves together to make the full droplet. I have also attached the .solidworks file, in case anyone wants to change the file to suit their needs or make any desired adjustments.
to print the .stl file, you will want to open your 3D printer slicer(I use Cura), and then set the layer height to 0.1mm, infill to 40% and speed to 30mm/s. You can increase the speed if you prefer, but i found that 30mm/s gives really clear results, with a very good surface finish.
once the 2 halves are finished, stick then together with superglue(cyanoacrylate glue) and very lightly sand the bumps and irregularities which may have occurred during printing, however do not worry about sanding away the layer lines, as they add to the overall light scattering effect of the epoxy once the lights have been casted.
Step 2: Silicone Rubber Casting
First, you are going to want to prepare your mould. Find a smooth flat waterproof surface (I used a tupperware lid), and then secure the 3D printed droplet point downwards using blu tack at the base to keep the model upright.
Next, place a used toilet roll over your now upright model( or a paper roll, as I did first time, though a toilet roll worked much better) and seal the bottom of the roll with lots of blu tack(I did not put quite enough and this caused the silicone to leak later on). Your mould is now ready to be cast.
Measure out the required quantities of silicone(for my silicone it was a 10 base:1 catalyst ratio), mix it thoroughly and tap the side of the recipient to remove any bubbles that may may have formed during mixing. Next, slowly pour the silicone in a thin stream into the mould, making sure to keep the pouring slow and even to remove more of the bubbles that may have been formed, whilst also preventing additional bubble formation. This is important as is prevents the mould from having pockmarks once solidified.
leave the mould to set for the next 24 hours, until the silicone has a smooth rubbery texture.Once it has set, carefully remove the toilet roll/paper roll, and then remove the mould from the smooth surface(the tupperware box). Once this is done, remove the blu tack from the bottom of the mould to reveal the end of the 3D print.
Now, carefully and with a sharp stanley knife/craft knife, cut down along each side of the silicone until you can remove the 3d print from inside it. make sure not to cut all the way through the mould. once you have removed the 3d print, close the mould again and secure it with elastics around the mould.
Step 3: Casting the Epoxy
First, you will want to wear protective gloves and a face mask, because epoxy is a sensitiser, and so repeated exposure to the VOC's emitted can sometimes result in an allergic reaction forming.
Now that the mould is ready, you should mix the epoxy parts together in the designated ratios, and then gently pour it down the spout of the mould. Depending on the type and thickness of the epoxy, you may need to open the mould slightly wider manually in order to get the epoxy to flow properly. I did not remove the bubbles from the epoxy because I liked the end result with bubbles, however if you want to have no bubbles in the epoxy, you should use a hot air gun or a vacuum chamber to quickly remove all bubbles formed, and then steadily and gently pour the epoxy into the mould. Fill the mould up to the spout, and then push the light through the top opening until it is about 2 cm deep into the mould. Leave the epoxy to set until hard (anywhere from 30 mins-24 hours), then carefully remove it from its mould and use a stanley knife to remove excess epoxy and trim off unwanted details.
repeat this casting process as many times as you want to create the water drop lights, and then put them up wherever you wish! I really enjoyed working on this project, so thanks for reading and happy making!
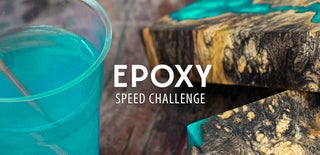
Second Prize in the
Epoxy Speed Challenge