Introduction: From Rusty Old Rasp to Shiny Kiridashi
Hi,
in this Instructable I would like to present you a simple way to turn an rusty old rasp into a shiny and sharp Kiridashi style knife.
Please make sure you watch the video and follow me on YouTube to see more of my projects (which not always make it to Instructables).
Step 1: The Material
I was stopping by a fuel station to get some coffee whilst on my way to the workshop. On the parking lot they have a big skip (open container) for people to dispose of their metal scraps. This is actually quite common where I live since many small communities and companies get a little extra income through selling those scraps.
Anyways as I walked back to my car with a coffee in my hand I noticed something lying outside the skip and I went to investigate. What I found was an old and rusty wood rasp and too be honest I had to think twice before I went and picked it up.
While driving to the workshop I though about projects I could use this rasp for. Due to the rust this rasp was too far gone to be restored and used as a woodworking tool.
So if you've been following some of my older project you might know that I like knives so I decided to try and turn this into a marking/utility knife.
Step 2: Cleanup
So before doing anything else I had to get rid of most of the rust. The easiest way to do this for me to clamp an electric drill to my table and used a brass wire wheel to remove the rust.
If you own a drill press that would work too and also if you used any other sort of wire wheel.
An alternative would be to submerge the rasp in vinegar for a few days. This should give you better results but since I wanted to get on with things I used a mechanical method.
Step 3: Annealing
Since I was planning to remove the teeth of the rasp and also to make grinding easier I decided to anneal the metal.
This process basically consists of heating the steel to the critical temperature and then letting it cool down slowly.
Since I do not know what steel exactly has been used in the file I simply heat the metal to a point were it is no longer magnetic. I then place the rasp on a fire brick and let it cool slowly.
Step 4: Pulling the Teeth
Part of the design I wanted was to remove the teeth but keep the dimples on the rasp. I do believe that this rasp was made with at least some degree of human involvement due to the irregular placement of the teeth.
This is a very nice feature that adds a lot of character and therefore I wanted to keep the dimples.
At this stage I also kept the dimples on the flat side of the blade but more about that later.
Step 5: The Design
The design was fairly simple!
Most of the shape was already given through the shape of the rasp. The only two thing I had to do was to find an aesthetically pleasing angle for the cutting edge and round over the other end.
If you are doing this project I suggest you try around and find something that fits your material. In this case the angle is around 35°.
Step 6: Shaping
An angle grinder is really the only tool you will need to shape the blade. Use a thin cut-off wheel for the cutting operation at the cutting edge and follow this up with a flap sanding disk to shape the rasp to whatever shape you like.
Step 7: Grinding the Bevel
This was a great opportunity to improve my freehand grinding skills. It helped a lot that for this project I had to grind a chisel grind (which means that there is only one bevel instead of two on each side of the blade).
I started with a 40 grit belt for quick stock removal and moved up to 120 for a slightly better finish.
It was at this time were I should also have ground the underside of the blade flat. You could of course keep the dimples on the flat but I found that some of the dimples would break into the edge and a flat bottom helps a lot with sharpening.
Step 8: Hardening
This was actually surprisingly easy despite me dreading this step every time I make a knife.
The first part of the heat treatment consisted of heating the edge to around 840°C which can be judged by the bright red to orange color. Another way would be to test the steel with a magnet and once it is no longer magnetic it is ready for quenching.
In this case I used a vegetable oil for quenching and as far as I understand most vegetable oils should be suitable.
Step 9: Test and Clean Up
Once the blade has completely cooled down I used a file to test whether the hardening was successful. If the file skips over the blade without biting we can consider it a success. Be careful though as the blade is now very hard but also brittle. (If you want to you can get fancy with special files that will indicate the actual hardness of your blade)
I used a 180 grit belt to remove any scale that had formed during the hardening process and prepare for the tempering process.
Step 10: More Cleaning
So this is what I mentioned earlier. I did notice that there was quite some rust in a lot of the dimples that I just couldn't get rid of with a wire brush.
This is were I soaked the blade in some white vinegar for several hours and used an old toothbrush to get rid of the rust. Once I couldn't find any further rust I removed all vinegar with water (Since then I read that some people are also use baking soda to neutralize the vinegar).
Step 11: Tempering
I mentioned earlier that the blade is quite hard but also brittle. To address this problem I placed the blade in an oven for two hours at approx. 220°C and let it cool down slowly after that.
This removes the brittleness at the cost of some hardness.
If you know what kind of steel you are dealing with you can actually look up its properties and be more accurate with regards to temperature and time.
Step 12: Final Clean-up
During the annealing a thin layer forms on the surface of the blade. In this case it was a yellow straw color (The color depends on the time and temperature during the annealing).
I went up to a 240 and then 400 grit on the belt grind for this step. This will already create a nice finish but since I wanted to try some other techniques I then went to wet sanding by hand.
Step 13: Sharpening and Polishing
This was a rather long but also satisfying process during which I went from 80 Grit (for the bottom of the blade) and 600 grit for the cutting edge to a 2000 grit strip of sandpaper.
For convenience I cut the sandpaper into 5cm (2") wide strips and glued them to a pane of glass. This ensured that the sanding surface was absolutely flat.
My preferred liquid for wet sanding is window cleaner which seems to work better that just water. Some other makers also suggest soapy water.
For best results I changed the direction of sanding every time I stepped up a grit. This helped me to see the scratches from the previous grit very easily.
Once at the 2000 grit you have actually turned an old rusty rasp into a shiny sharp mirror.
Don't forget to deburr the other side of the bevel, this was done for this blade during the polishing of the underside.
Step 14: Testing the Knive
I tested the blade on several items as shown in the above pictures as well as the video.
Being happy on how this turned out would be a big understatement.
I hope I was able to inspire you to make something for yourself and look forward to your comments.
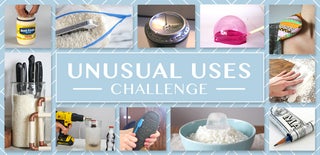
Participated in the
Unusual Uses Challenge 2017
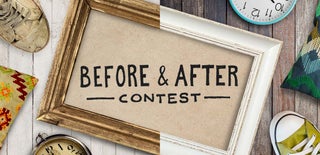
Participated in the
Before and After Contest 2017