Introduction: Making a Titanium Marking Knife for Woodworking
Hi there,
a while ago I've ordered some smaller pieces of grade 5 Titanium. There are various Titanium alloys each with different properties for different applications. They range from almost (commercially) pure Titanium Grades to alloys that can contain Alumin(i)um, Tin, Vanadium and other elements.
Titanium has some very interesting properties: It is very light compared to steel, it isn't magnetic, it is very corrosion resistant and it can be anodized with heat (or electricity) among many other things.
There are however risks involved when working with it. When I reached out to find out more in the maker community I was told by those with experience that they would only machine it with the use of a flood coolant. This is mostly due to the risk of ignition of the metal chips. Another suggestion was to avoid dust collection when grinding or working with powderized material titanium.
When grinding the material on the belt grinder I noticed the very bright sparks (bright white) but more about that in the grinding chapter let's get to it!
Step 1: Stock and Design
When I decided that I wanted to experiment with Titanium I began looking for stock on e-bay but wasn't lucky. So I ended up buying directly from a Titanium manufacturer in Germany. For a piece of 4x17x417mm I paid around 20€ + shipping and although it was pricey it wasn't as expensive as I thought it would be.
Next was the task of scribing a simple design on the stock as a guidance for cuts and grinds.
Since Titanium, reportedly, doens't hold an edge as well as a steel blade I decided for a use that does't require heavy cutting. Marking knives are used by woodworkers to scribe very thin and accurate lines into wood. These lines are thinner than most pencil lines and are the basis for precise work.
I tried to keep it simple using mostly straight lines but for the blunt end I used a washer for a nice round over.
Step 2: Will It Hacksaw?
Will it hacksaw? Short answer yes it will but your saw won't like it. Even with lots of cutting oil and regular cleaning of the teeth and avoiding pressure on the pull stroke the blade was pretty much useless after cutting through the stock. Alternatively you make a quick cut with an angle grinder but I tried to avoid that due to the amount of white hot sparks that would fly through my shop.
It'll also take quite a while longer to saw through than mild steel stock but is better to work with than hardened steel.
Step 3: Drilling
Before I started this project I did some tests on a sample piece. I learned quickly that I would ruin my regular metal drills pretty quickly. Not only was it more difficult to properly mark and center punch on Titanium the drills just didn't make much progress and I stopped before doing any damage.
This led me to buy a carbide tipped 6mm (1/4") drill and this did the trick along with plenty of cutting oil. The drill produced a clean hole and the only thing I had to look out for was regular chip removal. These shavings are very thin and can ignite due to the friction/heat. They wont explode in the face but an unplanned fire in the workshop is never a nice thing to deal with.
I didn't include it here but I used a regular 8mm drill to give the holes a slight chamfer. This basically worked in the same way as a countersink would but would be cheaper to replace if it went wrong.
Step 4: Grinding
This was the part I was most anxious about if I'm honest. As you can see the grinder and Titanium produce a lot of white hot sparks.
I used my Multitools Products MTA-362 with ceramic belts for the major stock removal as the ceramic tend to cut much cooler than comparable AlOx belts.
Needles to say that full PPE, except for gloves, is required! After a short time I got the hang of it and found that Ti is pretty similar to steel when grinding. A big difference to carbon steel was the heat build up though. Titanium has a much lower thermal conductivity than steel. This means friction heat isn't transferred as quickly as in steel resulting in the ground area getting very hot without you even noticing. As a result I burned my fingertips a few times (too often) before really understanding the grind/quench cycles. Despite this I found that the material would not heat up to blue as quickly as steel would.
I went through all grits I had available as I intended to produce crisp edges and satin finish before polishing and heat anodizing.
Step 5: Finish Wet Sanding and Cleaning
As a last step before polishing I went and wet sanded all faces with 2000 grit sandpaper. This produced a very shiny, not yet mirror, finish.
After this I took it to my buffing wheel and polished all faces with a fine polishing compound.
Once everything was polished to my liking I thoroughly cleaned the entire blade with acetone to remove any dirt, oil or fingerprints.
Step 6: Heat Anodizing
I tried this method before on another test piece and it is relatively simple. The blade is hung on a piece of wire (ideally Titanium wire, steel in my case) and suspended. Next I took my propane torch and started to heat the blade from the top. As I said before Titanium has low thermal conductivity so the heat doesn't travel as much in the material. This is good in this case as it makes it easier to control the colors. My objective was to create dark blue and violet colors at he blunt end and draw & fade them into a gold & straw towards the tip.
Once I reached a cherry red at the end I stopped and let the blade cool down slowly in the air.
One thing I noticed when editing the video was that there were small Titanium particles floating as dust particles in my shop. I was able to see them burn in the flame and a few seemed to have made their way onto the blade which resulted in a few small dots on the blade.
Step 7: Finished
So this it, no oil or other finish needed due to the properties of Titanium. The colors fade really nicely and I think I have found my new favourite material to work with.
As you can see in the pics I also made another tool and a small kydex sheath. Both are now gone to their new owner.
I'm currently planning to make a small batch of these so if you are interested in getting one please contact me via pm!
Cheers
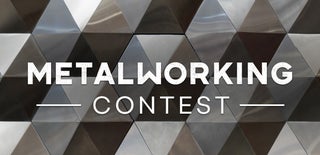
Runner Up in the
Metalworking Contest