Introduction: Icepick From Reclaimed Steel and Solid Brass - Diresta Inspired
Hi Instructabes Community,
this time I made an Icepick for use in a workshop inspired by the design made famous by Jimmy Diresta.
I also made a kydex sheath for protection but have not included that part in this Instructable. Please note that this is intended to be a tool and not a weapon. If you are found carrying this around in public you will have to come up with a good explanation.
Please note that I have added associate links to amazon products in this Instructable. Even if you do not want to buy a product I recommend I would appreciate if you could use the link if you plan a purchase. This won't cause you any additional cost but will result in direct support to me and my projects.
Step 1: Materials and Measurements
If you follow me here or somewhere else you have seen the 10 mm brass rod stock before. I really enjoyed working with that material and was looking for another reason to use it.
The second material used was a 6 mm (1/4") stainless steel rod I reclaimed from an old printer.
I should also mention the silver solder and solder flux
The measurements were pretty simple and based on my hand to determine the length of the handle. I tried to find a length for the awl that would look proportionate and appealing. Note that I added approx. 3,5cm (1 1/2") which will sit inset in the handle.
Step 2: Cutting Brass
This is pretty straightforward, to make it easier for you you should use a vise with soft jaws to get a solid grip on the round stock.
To get a good start you could make a small notch with a file but I felt confident enough to start directly with my hacksaw. I did this because I knew that the heavy texturing later would remove any scratches the saw might cause. If you are going for a different finish you might want to play it safe though and get a safe start.
Step 3: Cutting Steel
Since this was not hardened steel I was able to also cut it with a hacksaw. If the steel would have been hardened I could have made a quick cut with an angle grinder to solve this step.
Since steel is harder than brass I would advise to start with making a little notch so your saw gets a good grip right from the start.
Step 4: Before We Drill
Since the end of the stock I used was parted of by a lathe the center was already marked by the concentric circles. If that wouldn't be the case I would have had to use a center square to find the center.
I used first an auto punch and then a center punch to create a little dimple that would help my drill bit get started.
This dimple was made larger with a 2mm twist drill to make the hole big enough for the 6,5mm drill bit.
Step 5: Drilling a Straight Hole
Since I do not own or have access to a metal lathe I had to create the hole by hand.
I started really slowly with a hand drill checking constantly that the drill was centered and straight. I'm aware that there are a number of techniques to do this with a drill press. My drill press is however very far from being a precision instrument and it lacks the travel that would be required for most of the techniques.
In the end I managed to drill a hole to the required depth that was relatively straight...
Step 6: ...not Straight Enough Though
As you can see in the pictures even the slightest angle in the drilled hole will become obvious once the the rod is inserted.
In the end I resorted to enlarging the hole to 7,5mm and cleaning it with an end mill. I hoped that this would create enough play for me to straighten the rod during the soldering.
Step 7: Shaping I
At this stage I wanted to do a little shaping with files. This is for aesthetic purposes only and serves no practical function. The angle could have been also created with a hacksaw or with a grinder.
Step 8: Making the Awl
I chucked up the stainless rod in my hand drill and began to run the rod against my belt grinder (in reverse) to create a taper and point.
This was actually pretty easy as long as I didn't remove to much material too quickly.
Once I had the shape I wanted I switched to progressively finer belts to remove the sanding marks and ended up polishing the awl with a 1200 grit belt.
Step 9: Shaping & Texturing
I used the same technique as with my brass keychains. To create a random, rock-like pattern I used the contact wheel on my belt grinder. Since brass picks up the lines from the belt I had to find a good medium between material removal and finish and went with a fresh 240 grit belt. This is slower going and the material heats up faster but the finish is better.
Step 10: Soldering
Initially I wanted to glue the awl in with epoxy but decided to expand my skills and try silver soldering for the first time. The bond/connection would also be much stronger than with epoxy.
As a preparation I applied a flux for silver soldering to the awl and build a temporary furnace with some fire brick.
For a heat source I used a propane torch which, after doing some research, should get hot enough for this process. Before I started applying heat I also placed a few bits of solder around the joint area (which s something I previously saw in a video).
I tried to follow the advise I've read that when heating both materials one should look for changes of the solder flux. When applied first it still is semi translucent/whitish a of a gel like consistency, once it is hit with the heat it starts to solidify and becomes white. Once the right temperature for soldering is reached the flux becomes translucent again. At this stage I removed the flame and touched the metal with the silver solder right of the bat it started melting and filling the joint.
Since I had to enlarge the hole before I also had to add quite a lot of solder and then I added a little extra just to make sure.
While the solder was still liquid and all parts moving I used vise grips and pliers to position the awl as straight as possible. Since both metals conduct heat very well it didn't take too long for them to cool down and the solder to solidify.
Step 11: Clean Up
As I mentioned before I was a bit too enthusiastic about adding solder and I had quite a bit of clean up to do.
Since I was already in experimentation mood I decided to try and fade the texture of the handle over to the awl. This actually worked quite nicely although it is a bit tricky and I should have used a rotary tool at the joint area instead of the big contact wheel.
Step 12: Polishing
I'm not going down the road of inserting the pun about polishing my rod but that is exactly what I did.
For this step I used a polishing wheel in my drill press although I would prefer a bench mounted buffing wheel. Loading the wheel regularly with polishing compound I was able to round over burrs and edges and was left with a nice shiny finish.
Step 13: Kydex Sheath
To protect the icepick from damage and vice versa I decided to make a small sheath. Kydex is my go to option and I always like to improve my skills with it. Alternative options would be to make a leather sheath or maybe one from brass tube stock like the original.
Step 14: Why Do You Need an Icepick?
Thanks a lot to Jimmy for allowing me to add links to his videos showing practical and funny ways to use an icepick. So if you fancy one but don't like to go through the process of making one you can get Jimmy's Icepick here or if you prefer my version get in touch via PM and we can discuss a custom version for you.
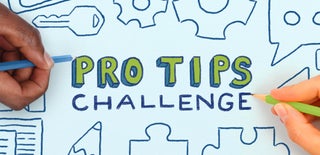
Participated in the
Pro Tips Challenge
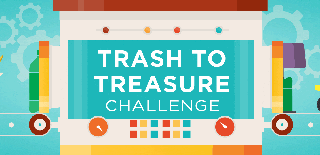
Participated in the
Trash to Treasure
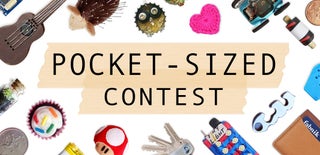
Participated in the
Pocket-Sized Contest