Introduction: Lego Imagination Station
There is nothing original or unusual about the concept of a "Lego Table". People have been putting Lego tops on IKEA Lack Tables since the dawn of time!
I am sharing a fairly simple idea here. It's a minimalist table, that wont look out of place (or garish) in a living room or indeed, child's (or grown-ups) bedroom. It also provides storage space, for Lego, instruction booklets etc. There are 2 drawers, which is great, if like me, you have 2 children!
It's the action that happens on the table top where the creativity really lies. You are providing a footing for whole worlds to be created and destroyed... Incredible....
Supplies
MATERIALS
One Sheet of 15mm Birch Plywood (~€40) (This could in fact be any 15-18mm sheet - OSB,MFC,MDF,WBP - its all about the aesthetic.
Various Screws (~5€) - I survived this project, with screws I had lying around. Everyone has a box of misc. screws. Screws generally 12mm (drawer slides) - 20mm -
4no. Lego Baseplates - I used Generic Strictly Briks Classic Base-plates 10"x10" for Building Bricks 100% Compatible with Major Brands) (~20€ if using generic)
Drawer Runners (~6€) Smith & Locke High Quality Metal Drawer Runners 246mm 2 Pack (I bought from screwfix) - Any Drawer runner will do, the key is the length.. 246mm is around the absolute limit.
Glue (~€5) Tube of "No More Nails"/ "GunOPrene" / "Liquid Nails" - Panel adhesive - will give you the grab and filling capacity to hold the panels - I used gorilla glue - which wasn't ideal!
Varnish (~€5) - I used Ronseal Matt interior Varnish - - Just got to keep that birchply safe.
TOOLS
Pocket Hole Jig (Optional) - This was the first time I used one - Interesting experience. If not using - simply pin, and fill.
Table Saw - Or some saw that is capable of clean straight cuts
Router - You need some way of chamfering drawer fronts (could be table-saw) and cutting channels for drawer runners (again could be table-saw)
Router Table (Optional)- To assist with cutting channels for drawer runners - Simple jigs can remove the requirement for this.
Step 1: Designing
DOODLING
After a bit of doodling - I moved to Sketchup (see image above) . I made a very simple proof of concept model, that gave me a gauge for some key dimensions.
After this, I move back to work with my "known" criteria.
I know the size of Lego base-plates.
I know the thickness of Materials.
DRAWING
This is what generates the detailed design. It's all based around standard available sizes, in particular, the dimensional criteria of 4 no. shop bought generic Lego base-plates stuck together. This gives us the dimensional building blocks for the rest of the project.
other things to note : drawer handles are just cluttersome - here the drawers are pulled via a gap and chamfered drawer front - with careful consideration given to not trapping fat fingers.
It is through drawing, that we get to grips with exactly how to build.
MATERIALS
I would eat birch plywood if I could. Beautiful pale timber veneered faces... the delicate grain pops with a little touch of varnish. The precise engineering of the laminated layers visible to the world, it's a glorious material, overused across the world for architects kitchens, and underused for almost everything else.
Another big choice is Thickness of material. - 15mm is just about the minimum that will work, and be suitably robust - 18mm would work also. I went for the slightly more delicate & lighter & economical 15mm.
Note: there are a few NON VISIBLE components where I was able to utilise scraps of 12mm WBP - I wouldn't necessarily have bought this for one project alone, but it meant i was saving some sacred birch plywood.
Step 2: Cutting List
As Mentioned - 4 Lego base plates stuck together using Lego scraps, generate the dimensions of the entire project.
It is from this that I generate a cutting list, noting all the components, the idea is to do all the annoying cutting stuff first, and then have a nice simple assembly job.
One thing to note here, because we are essentially cutting the finished article, you need as clean a cut as possible. I have a TERRIBLE table saw , If' I'd even call it that, which was purchased in a popular German supermarket chain! I did buy a good 80 tooth saw blade - Which gave me a SUPER CLEAN edge, which barely needed a rub of sandpaper.
If i didn't have a table saw - I would have taken this on with hand saw / jig saw and sharp plane.
There is not that much cutting!!
Step 3: Assembly of Body
Once all the pieces are cut, it's a simple assembly procedure. The only pieces of any difficulty to cut, are the legs, which will require jigsawing, and a bit of sanding and clean up. - Use a Superfine, super-sharp jigsaw blade, so as to not splinter the beautiful birch!
The way the table goes together is common sense.
POCKETHOLE
To avoid visible fixings, I purchased my first pockethole jig, the image above shows my first attempt at pocket-holing. note i could have simply glued and pinned these joints from the face. Birch ply, is fairly good at taking dots of standard colored beech filler!
There are 12 total pocket holes, and they are a pain in the butt to stop sliding, without a right angle clamp! I suggest doing a bit of reading on pocket hole "tips of the trade".
Step 4: Assembling Drawers
The Drawers are fairly simple utilitarian boxes. No need for pocket-holes, as none of this is visible.
I used a 1/2" router bit to route the bottom edge of all my "drawer sides" which meant that my drawer base just slotted in. When it was dry assembled, I glued and Screwed.
I Used a 1/2" 45 degree Chamfer bit to route the "finger edge" on the top of the drawer fronts.
See the Frankenstein screw driver assembly used to screw the drawer fronts to the drawers, from the inside.
Again, i used a 1/2" router bit, to make #6mm notches for the drawer runners.
The size and depth of notch is all down to the drawer runner. (See d1,d2,d3) dimensions d3 - is the trickiest dimension to establish, in the end, I "eyeballed" it!
Step 5: Almost There - Gluing Down the Base Plates
Finally, a good use for my weights!!
LESSON LEARNT
The key is the choice of glue - I should have chosen something more "grabby" - I'd recommend Cartridge Tube based adhesive - it has enough body to fill the hollows of the Lego base plates. I used Gorilla Glue - as it was the only glue I had - hence the requirement for the weights!
LESSON LEARNT
Half a millimetre of creep in my assembly, meant that I had to sand the edges of the Lego base plates - what a pain!! - Give yourself 1mm tolerance all round!!
I had shop bought laser cut letters, see the first image - I was going to put my kids names in each drawer, in the end I decided not to. No good reason, just actively disliked the font!!
Step 6: One Coat of Varnish & Remove Splinter Opportunities
A Rub of 240 Grit sandpaper to gently ease the edges, and protect small hands & a coat of Ronseal Interior Matt Clear Varnish - Brush Applied. I really thought it started to look great.... just needed some more Lego on top.
Step 7: Epilogue: Happy Kids
MAKE NO MISTAKE - There is nothing worse than stepping on a Lego piece!
This is an important piece of Living Room Furniture. This has kept Lego pieces off the floor, and will protect "unshod" feet for many years to come.
Wolverine & Superman, fighting the Lego friends girls, who have stolen a boat. All while an unmasked Batman watches in horror. This is Gold, & this is just what a Lego table facilitates!! Pure unadulterated IMAGINATION.
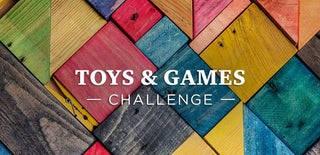
Participated in the
Toys and Games Challenge