Introduction: Marblevator, Mechanisms.
"Marblevator, Mechanisms" is the latest in my Marblevator series of marble machines and features the quickest marble lift mechanism I've ever designed. My fascination with gears, mechanisms, marble machines and history formed my inspiration for this model.
UPDATE: added "Base 2.stl" with a slightly longer track.
The model incorporates two antique mechanisms; a "Peaucellier–Lipkin" straight line mechanism (vintage 1864), and a "Whitworth" quick return mechanism (vintage 1800's) that, when combined as they are in this design, provide a straight line slow ascent, and a straight line rapid descent. In this model, these combined functions are use to slowly raise a bucket containing a marble (an 8mm ball bearing) to the top of a short, built in, track, dump the marble onto the track, rapidly lower the bucket to pick up the marble at the bottom of the track, and then repeat the process.
I've included a sketch illustrating the method I used to compute the bar lengths for the straight line mechanism. If you have any questions about the illustration leave a comment and I'll do my best to answer.
As usual, I probably forgot a file or two or who knows what else, so if you have any questions, please do not hesitate to ask as I do make mistakes in plenty.
Designed using Autodesk Fusion 360, sliced using Cura 3.3.1 and printed in PLA on both an Ultimaker 2+ Extended and an Ultimaker 3 Extended.
Step 1: Purchase, Print and Prepare the Parts.
Marblevator, Mechanisms requires a 300 rpm gear motor (33x12mm 300RPM Metal Mini DC 6V Gearbox Gearwheel Motor Mini Reduce Speed Geared Electric Motor), a 1.5 vdc power supply, and an 8mm (3/8") ball bearing.
I printed "Bucket.stl" with .1mm layer height and 100% infill. I printed the remaining parts at .15mm layer height with 15% infill. I printed two "Bolt, 4.2mm shoulder.stl", four "Bolt, 8.4mm shoulder.stl", four "Arm, DB.stl" and one each of the remaining parts.
Prior to starting assembly, test fit and trim, file, sand, etc. all parts as necessary for smooth movement of moving surfaces, and tight fit for non moving surfaces. Depending on the colors you chose and your printer settings, more or less trimming, filing and/or sanding may be required. Carefully file all edges that contacted the build plate to make absolutely sure that all build plate "ooze" is removed and that all edges are smooth. I used small jewelers files and plenty of patience to perform this step.
Marblevator, Mechanisms uses threaded assembly, thus a tap and die set ((M4 by 0.7, M6 by 1) may be required for thread cleaning.
Attachments
Step 2: Assemble the Upper Arm (Arm CD).
Position the first "Arm, DB.stl" onto "Arm, CD.stl" as shown.
Position the second "Arm, DB.stl" onto the first as shown.
Secure the three arms together with the first "Bolt, 8.4mm shoulder.stl" as shown.
This is the upper arm assembly.
Step 3: Assemble the Lower Arm (Arm CE).
Position the third "Arm, DB.stl" onto "Arm, CE.stl" as shown.
Position the fourth "Arm, DB.stl" onto the third as shown.
Secure the three arms together with the second "Bolt, 8.4mm shoulder.stl".
This is the lower arm assembly.
Step 4: Assemble the Mechanisms.
Position the upper and lower arms together as shown, then position "Bucket.stl" into position as shown and secure the bucket and arms together using the third "Bolt, 8.4mm shoulder.stl"
Secure the remaining two arms together by positioning "Arm, Wheel.stl" as shown then secure the arms together using the fourth "Bolt, 8.4mm shoulder.stl as shown.
This is the mechanism assembly.
Step 5: Attach the Mechanism Assembly to the Base.
Position the mechanism assembly on "Base.stl" as shown.
Position "Wheel, Geared (64 teeth).stl" as shown.
Secure "Arm, Wheel Geared.stl" to the base with the first "Bolt, 4.2mm shoulder.stl".
Secure "Wheel, Geared (64 teeth).stl" using "Axle, Wheel Geared.stl". The axle will travel through the center hole in the geared wheel, through the free hole in the lower arm assembly, throughout the free hole in the upper arm assembly, then into the threads in the base.
Step 6: Attach the Mechanisms to Wheel, Geared (64 Teeth).stl.
Position "Arm, Wheel.stl" as shown then secure it to "Wheel, Geared (64 teeth).stl" using the second "Bolt, 4.2mm shoulder.stl".
At this point, "Wheel, Geared (64 teeth.stl)" should easily rotate and the mechanism should work smoothly. If any binding occurs, make sure the arms are positioned properly and the bolts are not over tightened.
Step 7: Attach the Gate.
Position "Gate.stl" onto the base assembly as shown, then secure it in place with "Axle, Gate.stl".
Step 8: Final Assembly.
Press "Gear, Spur (8 teeth).stl" onto the motor shaft as shown, then slide the assembly into the base until "Gear, Spur (8 teeth).stl" aligns with the teeth on "Wheel, Geared (64 teeth).stl"
Apply 1.5vdc to the motor such that "Wheel, Geared (64 teeth).stl" rotates counter-clockwise when viewed from the front.
That's how I printed and assembled "Marblevator, Mechanisms"!
Hope you enjoy it!
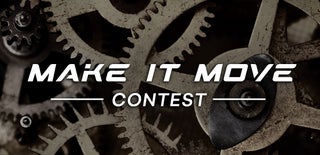
Participated in the
Make it Move Contest