Introduction: Wide Plank Floor DIY: Rough Cut to Tongue and Groove
As Winter progressed in Michigan and outside projects turned to inside projects A massive idea came to fruition. Lets finish the basement! Which has been slowly transformed from a moist rock 100 year old, but 8 feet tall basement into a water proofed framed canvas complete with subfloor.
I may make a few instructables about the whole process, but the floor was the Gem of the whole remodel.
This Ible will cover the process of turning rough cut 150 year old white pine planks into a custom one of kind soft wood floor. Full of character, color, warmth and a personal relationship with 500 board feet squared,planed, ripped, cross cut, shaped, sanded, installed,nailed, and sealed by 3 men and during a cold @$$ winter!
Step 1: Picking the Lumber
We Contacted local saw mills and priced out different varieties of lumber. Oak, Maple, Walnut all great woods and make beautiful hardwood floors. But 500 board feet was too costly to have it kiln dried and we didn't have time to wait for air drying. In the end I contacted a local excavator that I had purchased white pine from in the past. He still had a few piles of stickered planks that had been air drying for 1.5 years.
The boards ranged from 10-15 inches wide and all about 10-11ft long. And were any where from .825 to 1.5 inches thick. The floor would need 350 sq feet of finished boards but purchased 500 ft for waste. For $250.00
The main concern with this DIY project is using good wood that is dry and wont warp. Soft wood dings easily and will develop a warn look much fast than hardwood. However it is a dream to walk on and in a low traffic area is suitable I think. Historically white pine was used in many floors through out the houses in many of New England's historic homes so i hear.
The wood was covered with a tarp and had a foot of snow and ice on it but we dug down and loaded up the trailer. We then stacked and stickered the planks in the basement to acclimate before milling. Using a moister meter purchased of Amazon we check random boards to get an idea of what we were working with.
Boards ranged from 15-25% which got me worried So to keep the boards from cupping and changing as they dried we took ratchet straps and kept the pile locked in from moving. Set up fans and worked on other projects for the next 2 weeks.
Step 2: Squaring
After 2 weeks of the house smelling of a lovely pine smell, and rotating fans around the moisture meter gave us some better numbers and we were ready to square up the 50-60 planks. And this is where the labor requirements for this project start to sink in...
Each board was passed through the basement window outside to the workshop. The planks were stacked on saw horses. Then a square board was used as a straight edge and screwed into the board being cut. A joiner would do this for you if you have one but this is one way to do it on a table saw.
50-60 boards later we had one of the 6 sides of every plank square. To minimize waste we came up with the final board sizes of 5 and 7 inches wide. So a 10+ inch rough board would be two 5 inch planks. A 12+ inch would be a 7 and 5 inch plank and 14+ would be two 7 inch boards. I think we may have had a 16 inch board that made three 5 inch planks.
Placing the cut/square edge against the fence and running an assembly line all the 5's were cut to 5.25 and the 7's to 7.25. To get to that point was a solid day of work. A fresh Dewalt 30 tooth blade was helpful and cut the pine like butter on the trusty crafstman 3hp table saw from the 1980's.
The saw dust pile grows daily and is cleaned up at the end of each day or at least contained.
Step 3: Planer Time
After all the boards ran through the table saw and became square it was time to plane. I purchased a Dewalt Planer DW734 12.5 Inch planer. It was in my mind the best planer for small projects I could afford . Although this project I would not call small it was still a valuable tool and worked well.
The lumber thickness ranged from .8 to 1.5 inches thick. Most floors are .75 inches thick and the air floor nailer we were scoping out was designed to do floors of that thickness so .75 would be our final plane thickness. But it would be many many many passes with every board to achieve that thickness. At 1/32 per pass maximum you better pack a lunch.
You also will need a dust collector because of sheer amount of shavings that will be generated from mulipule passes on the planer. After searching on Instructbales we came up with a cyclone that would dump the shavings in a 50 gallon drum while using the shop vac. Cant recall the exact users we tried recreate but I will add a link when i do!
Also this should of been mentioned before but always have safety glasses and ear protection when using the planer and really every power tool that is screaming.
You can see that full outdoor cold weather gear was required but staying moving all day keeps you warmer.
Its hard to see in the picture but having a feed/exit table is helpful for avoiding snipe. The boards will be cut to length and any bad sections will be cut out so if we had some boards that got away from us it was fixable.
Note. This was round one of planer. We would do every board a final time after the tongue and groove step. This is so that any abuse the boards take while being milled can be corrected on the final planer pass.
Step 4: Tongue and Groove
After all the boards transformed from rough cut slabs to clean looking "store worthy' wood. It was time to set up the shop for tongue and groove. Using a 1/2 inch router and multi tool station from a 1980's popular mechanics project that my dad had built, it was time once again to handle every board a few more times. One more reason to use 3/4 inch planks for the floor was the T+G bit for the router was made boards at 3/4. IT was destiny..
Finger boards were set up on 2 faces. 1 to keep the board to the fence and 1 to keep the board down to the table. This ensured a more consistent cut. I believe we ran all the boards through good side up and all the tongues first and grooves second. This was another all day project. The shop vac was taped up in a way to suck all the chippings away. Which was needed because the cut wouldn't be as clean with out dust collection it appeared.
Our backs were sore and bodies ached but some major mile stones of the project had been completed.
Behind the guys you can see the MTN of sawdust and shavings from the planer!
Step 5: Cut to Length
Next was time to cut to length and to cut out really bad knots. We wanted to use longer lengths of boards but would fill with shorter ones to make a floor with out a pattern but still balance. Short and long pieces mixed together in similar amounts throughout the floor.
The miter saw was calibrated because prior to this step didnt seem to be cutting square. And sure enough it was off a degree. Every board was once again inspected and handled and chopped. Most knots we did save but some were really bad and had fallen out. This step took time but went faster and was less labor intense than previous steps. After all the cuts it was time to move the wood back into the basement and let it acclimate again for a few days. I think we took a few days rest as well.
Step 6: Prepare the Sub Floor
The sub floor had been laid a few years ago and just need a few screws added in places and to be swept and vacuumed. A roll of red flooring paper was purchased and would be rolled out in 3ft sections and stapled before the wide plank floor would be laid. The boards were checked with the moisture meter and after planing and acclimating seem to all be under 10% moisture which I read was a good starting point for a solid wood floor.
The air nailer we purchased was from Harbor Freight. Not all tools are created equal but i will say harbor freights air tools are reliable, do good work and for me hardly miss fire. I have a brad nailer that was $17.00 and has fired 10,000 nails with only 3 or 4 jams. Just keep it oiled and good to go. It would of been about even to rent a nailer or buy the HF so why not add a tool to the arsenal..
Step 7: Layout and Nail!
To avoid issues from the planks expanding in higher humidity times of the year we made sure to leave a 3/4 inch gap around the room on all sides of the floor. The nailer shoots a cleat nail or staple through the tongue of the board. So we decided to start on the wall and work from the hallway side of the basement across. We had final board widths of 5 1/2, 7 and a few 6 inch boards. Running a row of 7's then 5 1/2's then maybe two rows of 6's. It was always changing but the end look was a balanced floor with a mix of short and longer planks and a mix of widths.
We continually checked with tape measure to ensure that our rows were not wondering. If for example the row was tighter at one end and looser at another. The next row would be placed in a way to smooth out the difference.
The nailer was set at 85lbs pressure and a cleat was placed every 8 inches. Most the planks behaved but some need to manhandled to fit how we wanted it. I was surprised at how fast we moved and half the floor was done in a half a day. We continued later in the day and finished nailing the floor. Some planks needed to be custom cut to fit around the stairs, posts and the last row on the furthest wall had to be ripped to a size that we didnt have, like 4 1/2 I believe.
Using a scrap section of groove and a hammer was helpful for the tighter fitting sections. Some garden knee pads also were a nice treat for scooting around all day. The nailer has its limits and 2-3 rows had to be face nailed because the nailer handle would hit the wall and not reach.
Teamwork in this whole project was crucial for keeping the momentum moving. It can be easy to start a project and before finishing it, wanting to move on to something else. Take turns to break up the work and try to do each step as efficiently as possible. Beers help too.
Step 8: Wait....Then Sand and Clean
After nailing was over we decided to take a few day break and do other things to let the floor acclimate some more and find its home before finishing. We spent some time walking the floor over and over. The floor was solid but had some give and made a few creeks in spots. We are calling this character...
This floor is full of character. Knots, bug holes, tints of blues reds grays. Lengths of clear wood and lengths of anything but. There is even a slug from a bullet fired who knows how many years ago. Thank goodness it was lead and didn't chip the planer...
After admiring the planks and floors uniqueness it was time to finish it.
Using 120 grit, a dusk mask, and the orbital sander the whole floor was sanded. Mostly to get the high spots and any marks made from the planer. Soft wood sands really quickly and after 120 grit was used on the entire floor, 180 grit was used to get it ready to be finished.
The floor was gently vacuumed and using denatured alcohol and a clean rag the final small remaining dusts were collected. I think you can use mineral spirits to clean up sanding dust and oils in the wood but I had denatured alcohol on hand so thats what I used.
Took a lunch break and prepared for applying polyurethane as the finish for our pine plank floor.
Step 9: Poly TIme
Originally we wanted to use stain on the floor, but after seeing the planks all laid out we decided to just go with a clear coat.
Which I am glad we did because pine can be hard to stain and achieve an even color. On that scale with that porous of wood it would require a coat of pre stain, or shellac. Then it would be staining, then clear. Ehhhh no thanks. We were ready to finish this sucker and not spend any more money. Great decision in this circumstance.
My brother did the whole first coat. Using an applicator pad and 2 gallons of floor grade oil based polyurethane the floor was coated. Working in a 3ft wide section, starting at the end of the hallway and then working his way around the room to finish at the stairs. Coat one was complete. The wood was sucking the poly up pretty fast, but from past issues of applying too much poly at one time we kept moving and would do multiple thin coats. Too thick of a coat will not dry properly and will remain gummy and useless.
Standing on the stairs observing was helpful for getting a different angle to view spot of areas that needed to be touched up.
The floor was allowed to dry for 6 hours and then recoated. We did not sand between coats. We used a minwax polyurathe that stated sanding was not required between coats if you re coated in under a certain amount of time. We had two fans strategically placed that were turned on and let run over night. When the morning came we checked out our work...
Step 10: Final Highlights
After the long journey the floor was complete. Trim was still needed to cover the gap on all the walls. Pictures of that to come.
After doing a floor from scratch and seeing the whole process from start to finish I dont know if I would ever try it again. Maybe 150 sq feet but not 350 sq feet of floor. Its a lot of work and even with 3 people it took weeks. If you have already milled lumber tongue and groove and ready to go for flooring it would be no issue. But if you are glutton for punishment or have a wood shop with a next level planer and a next level router/shaper this project is very doable.
Like they say having the right tool makes the job.
Thanks for checking it out!
Jake, Mason, John
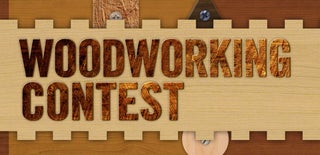
Participated in the
Woodworking Contest