Introduction: "Alina"-The Best 3D Printing Enclosure (Fireproof, Thermostat Controlled Cooling,Toxic Fume Exhaust)
Elevate Your 3D Printing Experience with Our home-made Aluminium Enclosure!
๐ Non-Flammable sturdy structure:
Say good bye to plastic covers which may warp under high temperature or even catch fire! The aluminium structure shall hold well even under accidental fire and give you peace of mind.
๐ Temperature controlled exhaust: Provides a stable and controlled environment for your 3D printing projects. Say goodbye to warping and uneven prints, as our enclosure ensures consistent temperature conditions by thermostat controlled exhaust fan for optimal results.
๐ก๏ธ Maximum Dust-Protection during storage: Protect your equipment from external elements, dust,insects and contaminants, ensuring longevity and peak performance for your valuable investment.
๐ฌ๏ธ Toxic Fume Exhaust at Your Fingertips:
Achieve unparalleled safety over the printing environment with the enclosure's fume management system. Whether you're printing with PLA, ABS, or other filaments, release the toxic fumes outside of your workshop by aluminium vent.
๐ Best Cost:
Did I say that the cost of this enclosure is reasonable than the available enclosures of similar capabilities? Fume exhaust, temperature control, Airtight frame, Inside illumination, It covers all!
Supplies
Materials: 73$ (Prices are local. May vary location wise. Comment cost of your build so I may update this section)
- Aluminium Sheets (6 nos. 30"x30" .0.3mm thick) 15$
- Aluminium Members (Channel/ square sections of approx. 1inch width,18 nos. 30"length) 15$
- 150-200 nos. 1-1/2" long, 3-4mm Dia Screws and fitting Nuts 2$
- 2 hooks for locking door 4$
- 2 hinges for door 4$
- Cello tape/ Duct tape for sealing edges 1$
- Thermostat controlled exhaust fan module (W1209 moule or similar) 6$
- Aluminium duct pipe- (4"- 6 foot) 7$
- PVC pipe elbow (Size greater than 4 inch) 3$
- Sealing Tape for door (EPDM D shape or similar, minimum 6mm thick) 5$
- LED Bub and holder 6$
- Miscellaneous (Wires,switches,etc.) 5$
Tools: 48$
- Grinder/Cutter tool 20$
- Drilling machine 14$
- screw driver/ wrench/ plier etc 5$
- scissor (to cut aluminium, normal scissors as shown in picture will do) 4$
- Misc.( Ruler, Measuring tape, etc) 5$
Step 1: Cut the Sheets
- Buy 6 numbers aluminium sheets of 30"x30" dimension.( 30" gives good space to work. You can adjust as per your need. However, if you need to move the enclosure later from one room to another, the width may need to be reduced because of available door width). You may buy a long sheet and cut it into required sizes by scissors.
Step 2: Cut the Columns and Beams
See sketch attached for cut-length calculation. Horizontal beams need to be cut before column joint to match total width. Make your own sketch if you are changing any dimensions.
- 6 number vertical columns will be full 30" long= 762mm . Don't cut
- 4 nos Long Beams- (marked as L.B in sketch) Cut beam to 738mm. (See sketch, 762-2a=762-24)
- 6 nos remaining beams. Cut beam to 722mm (See sketch, 762-2b=722)
- 8 nos bracings 190mm long each.
Step 3: Connect the Beams With Plates
Connect the beams with the plates as shown. 5 screws per side is ok.
Step 4: Connect the Corners
Connect the corners. Make sure that a screw is within 2" of corner in each beam. That will give sufficient rigidity to the corners.
Step 5: Add Bracings
Since the front side does not have a plate connection, you MUST add bracings for rigidity. Connect bracing as shown on the corners of opening. Add sealing tape around the door as shown.
Step 6: Add Door
Add door, 2 hinges, 2 hooks for locking the door, referring to the picture shown. Notice that there is a small eraser attached below the door corner so that the door does not bend vertically. It is good for long use. Cut window as required. Cover the window with Plastic for printing PLA/ABS or glued tampered glass if you want to print very high temperature materials.
Step 7: Fix Accessories and Seal Openings
Fix the light-bulb, temperature sensor, exhaust fan,aluminium vest pipe, Inlet elbow to the Structure. Notice that the inlet elbow is above ground by 7 inches so it does not suck dust. Also the inlet is channelled to the bottom of printer by aluminium sheet to keep the printer Motherboard cool. The temperature sensor is placed near the printer bed.
All openings are sealed by Duct tape for PLA/ABS print. If you want higher temperature resistivity, You may use aluminium tape but that will increase the cost. All edges and corners of the box are sealed likewise.
Step 8: Electric Connections
Make sure no connection touches the box directly. It may cause shock and/or death. Provide the light switch outside. Provide thermostat control so that if the temperature exceeds around 35 degree(temp for PLA, for ABS it shall be higher value of which I cannot confirm) then exhaust fan will turn on. For my W1209 Thermostat settings are as follows: ( P0=C,P1=5,P2=33)
Step 9: Try Printing!
Now start printing! Don't forget to cover the openings when not in use.
Step 10: Checklist:
As a bonus, Use following checklist to print good models:
Platform is aligned.
Min thickness 0.8mm for straight walls, provide raft for sticking the model to bed.
Overhang less than 12mm. Provide supports otherwise.
Raft for low contact base.
Add gluestick for adhesion.
check temperature: nozzle+bed+enclosure for PLA/ABS.
Exhaust and inlet is un-obstructed.
Check machine while printing at 5min, 20min,1 hr afterwards.
per gm of print shall take approx 4.75 min. (varies from machine to machine)
After finish, Cover all openings and door.
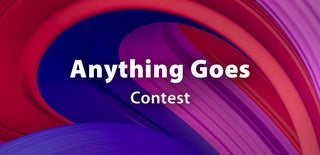
Participated in the
Anything Goes Contest