Introduction: Stained Glass Sea Turtle Lamp
Hello! It has been way too long since I have published an Instructable, so for my long time subscriber's... sorry its not an airplane! I hope you enjoy this dive into my first stained glass. When I started this project I was thinking it was something I would be able to knock out over a couple weekends, but since life never stops it took a little over a year working on it here and there. All in there are about 170 glass pieces and took maybe 100 hrs for the completed project. This Instructable covers the basics of stained glass including the making 3d patterns, cutting, and soldering before jumping into how to make this lamp!
Supplies
Tools
- Safety Glasses: because broken glass is going to be everywhere
- Glass Cutter (with cutting oil)
- Grozing Pliers: used to flake off small pieces of glass to clean up and reshape an edge
- Running Pliers: used to crack glass along a line scored with the glass cutter
- Sheet Metal Pliers: useful for making narrow strips of glass
- Channel Locks: when the grozing pliers don't have the power, channel locks do
- Ruler
- Pencil
- Sharpie
- Scissors
- Razor
- Hot Glue Gun
- Soldering Iron (Hakko FX888D with a large flat tip): the more power the better, you will be melting large amounts of solder at a time. There were some large joints that even this iron struggled with.
- Disposable Paint Brush: for brushing on flux and patina
- Fume Extractor (or work in a very well ventilated space, the flux will release particulate into the air once heated)
Supplies
- Colored Glass: Sold in craft stores or online. I find it much easier to buy in person since you can see how it reacts to light, and its texture
- Stained Glass Solder (60/40 Solder aka 60% tin & 40% lead) there are some non-leaded options as well but they have different coloration and working characteristics, I haven't tried them.
- Stained Glass Flux (Novacan Old Masters Flux)
- Stained Glass Patina (Novacan Super Brite Copper Patina)
- Paint on Glass Frosting (Folk Art Frost Effect)
- LED Light Strip with Dimmer
- Electrical Wire
- Brass or copper rod
- Disposable Gloves (Stained glass solder is lead after all!)
- PATIENCE
Step 1: Types of Stained Glass
To my knowledge there are 2 main ways of making stained glass. The traditional method uses lead came which is like an I-Beam of lead that is bent between each piece and soldered at the ends. This method is typically used for architectural class like doors, windows, churches etc. The other method and the one used on this project is foil tape. In this method the glass pieces have their edges wrapped with a metallic tape, which is then able to be soldered directly too. This method has traditionally be used for smaller pieces and 3 dimensional shapes, like the famous Tiffany stained glass lamp shades.
Step 2: Shaping Glass
Glass for stained glass is shaped using a glass cutter, and a series of pliers that are able to help refine the shape. The glass cutter has a oiled cutting wheel that scratches the top of the glass as it is moved along the surface with moderate pressure. The cutter will give the sheet of glass a weak point that the glass SHOULD crack along. Once scored with the glass cutter, running plies are used go apply pressure on from beneath the scored line, and from the top of either side. The resulting tension in the scribed part of the glass cause the glass to crack locally, and then propagate along the line. Working from both sides of the scored line and alternating after you hear small cracks forming can help on curved shapes. If you are lucky the broken edge will be square and perfectly follow the scribe. Since we can't make a whole turtle with luck we will need something else. That something is a grozing plier. This plier has a curved jaw with teeth on it that you use to grind the sharp edge of the glass against to make it flake off. For me its a tricky tool and works okay at best.
I have found that normal channel locks are also very effective at shaping the glass because you can easily crack off pieces with their very strong grip. If you are making long straight pieces a sheet metal bending pair of pliers with tape on the jaws (to prevent scratching) works great as a way to break off a narrow strip.
In the end you will need to find the tools and methods that work for you! Not covered here but definitely an option that I often see used is a water lubricated diamond grinder. It allows you to sand the edge with a spinning drum. They look like they would be very effective for making curves, and tighter fitting shapes. Unfortunately they are pretty pricy so let's just agree that a grinder is cheating. Got it... Good.
Step 3: Taping
Taping is the process in which the individual pieces of the stained glass piece have their edges wrapped in a copper foil tape to provide a surface for the solder to bond to. The copper tape ranges in width, but is typically 7/32 or 1/4 inch wide though other widths are available for difference thickness of glass. The tape must be wide enough cover the full edge of the glass and wrap both on the face and back. The tape backing comings in a variety of colors including copper, silver, and black. The selection of the tape color should match the planned patina for the solder. That way if the glass is translucent the inside of the tape that would be visible is the same color as the solder.
To tape a glass piece first wash it with a degreasing agents to remove the cutting oil (dish soap or rubbing alchole work well) Then starting in a corner or wherever is convenient on the edge, center the on the edge of the glass. Wrap the entire edge with the tape with a slightly overlap the start of the tape. Cut the tape with a sharp pair of scissors. The foil is now ready to be folded onto the face and back, relief cuts will be needed in sharp corners to allow the tape to lay flat. There is a slight amount of stretch to the tape, so it will generally conform to gentle concave edges. Once the relief cuts are made fold the edges over so that they are all bonded to the face and back. Lastly, using a plastic scraper (gift cards work great) gently squeegee the tape to flatten it to the surface.
The crazy thing is that taping is the most time consuming part of the whole project!
Step 4: Soldering Safety
With the pieces now cut, cleaned and taped they are ready to solder. When soldering consider all the appropriate safety precautions. Safety glasses as always, because the flux heating can cause the solder to splash. You will be handing solder which for this application typically has lead, so wear gloves when handling it. Don't do anything that will produce dust (sanding, filing, whatever other bad ideas). Clean your work surface regularly and be sure to wash up immediately after working.
Next is ventilation, which leans heavily on my readings from the manufacture Hakko and the manual for their fume extractor. Different products produce different risks so be sure to research the specific produces you are using by looking up their safety data sheet (SDS or MSDS). Flux will produce smoke when it is heated in the soldering process. It can be mitigated by working in a well ventilated area and using a fan to blow it away from you, or thru the use of a fume extractor. For soldering a HEPA filter is appropriate, since smoke is composed of solid particles suspended in the air. On the same note, lead doesn't vaporize in meaningful amounts at the temperatures used for soldering. The risk associated with it is not in the form of smoke but in solder residue. There is a lot of creditable studies on using lead solder in the work place (government and independent), its an interesting read and one topic that is worth becoming comfortable with before jumping into the hobby.
Step 5: Soldering
To solder, first ensure that all the tape on the pieces you are looking to solder are clean. If you taped pieces of the course of months, you may need to clean the tape with a light abrasive to remove any surface oxidation. Then secure the pieces you are looking to solder. If you are doing a large 2d piece find a way to secure the outside boarder, otherwise the pieces are likely to shift and the pattern will stretch in a direction. This can be done with a boarder of pins into your work surface, or hot glue, you name it, it just needs to be stable, and easily removeable. Then using a small disposable paint brush brush a small amount a flux over the area to solder. I like to make a few small dots on each piece so that I can "tack" the project together with several small dots of solder before going back and soldering the whole line. It is nice because if you find you need to shift pieces around they aren't held by much. Set your soldering iron to the appropriate temperature, I found that setting the iron to 650-750 deg F worked well for me but it will depend on the solder you are using. Next with the soldering iron touch the foil and start feeding solder onto the tip. It will start to melt and pool. From here you can either remove the tip and let it cool as a tack, or continue feeding solder and start slowly moving down the joint. The goal is to have the bubble of solder that is above the glass uniform and smooth. To help smooth it out after if it laid down, you can rerun the soldering iron over the joint to re-liquify it. This will generally smooth it down, though if the part isnt flat on the table, then solder may be able to drip out or run to the low point. Once the entire front of the piece is soldered, it is flipped over and the reverse side soldered. On this side it is important to move quickly enough as not to melt the solder the whole way though and undo the work you did on the front. With the back done the part is compete, the piece should then be washed with soap and water to remove the flux/solder residue.
Step 6: Coming Up With a Pattern
The step of any project is figuring out what it should be, for this I started by googling sea turtle pictures. For the sake of finding something easy make a pattern from I found that cartoons helped to accentuate the shape and features.
The pattern for the shell stated with a top view, and a side view. Having never cut glass at this point I decided that I would use straight geometric shapes to make the shell, much like the way paper craft sculptures are done. I started on the spine of the turtle making the templates from poster board. Once I was happy with the shape I would tape the piece in place and move on to the next one. Working one row at a time I eventually make it to the edge of the shell. I numbered all of the pieces and took pictures from every angle so that once I cut the tape that was holding the pieces together that I would hopefully be able to put it back together. With something like 40 pieces per side I knew I knew I was in for quite the project but boldly decided to go for it.
I have included PDF files for the pattern in each relevant step, with the piece numbers matching the pictures. When printing them be sure to select the option to not scale them to the page so that they will not be scaled when they print. I would recommend printing them out on a thicker paper, like resume paper, so that you can tape them together to check fit prior to cutting glass.
Attachments
Step 7: A Turtle Requires a Strong Backbone
With the pattern for the top of the shell laid out it was time to get after it. I started cutting the pieces for the spine, and quickly discovered how hard it was to cut textured glass. The score in the glass is straight and the break sometimes went along a completely different line. Eventually I found the technique that worked for me with the running pliers, or using the sheet metal pliers to crack along a score. With center pieces cut out, I hot glued them to the template to hold them in place while so they could be tacked in place with a little solder.
Step 8: Diamonds: High Fashion
The process for making the next row was much like the first except for now there was nothing to glue the pieces to. I found it easiest to flux both mating pieces just where you are going to tack them, and then apply a blob of solder to the main part of the shell. With the blob there you can remelt it with the soldering iron in one hand, and then place the piece in position with the other. Once you are happy with the position remove the soldering iron and wait for it to cool. You can then tack the other side of the piece and it should stay.
The important thing here is to only get the flux were you are actually soldering if you aren't doing the complete line. The reason being that the flux will dry, and once dry it can be hard to remove/solder over. If you do have extra flux on it, just wipe if off with a wet paper towel before moving on.
Step 9: Apparently Patterns Require a Gap Between Pieces...
This is where things started to get tricky. Usually if you are making a 2 dimensional stained glass pattern you would use pattern scissors to cut between the pieces. They have 3 blades and actually remove ~1/16th of an inch of paper between the pieces of the pattern. Think of it like they cut on both the inside and outside of the line, leaving you with what is outside on both sides. Well... my pattern didn't include any gaps which turned into a headache. Because the edges of glass are never straight or smooth, the pattern grows with every line of pieces that you attach. This wouldn't really matter if it was something 2d since it would just get bigger, but on something 3d this means that the corners no longer aligned. So every piece had to be trimmed down ever so slightly to get "back on pattern". Even worse is that the left and the right side of the shell became ever so slightly different that they required their own pieces be fitted to each. It was a pain staking process but the project must go on!
Step 10: Triangles!
This row proceeded much like the last with small tweaks to each piece to try to keep it close to the pattern
Step 11: A Lot More Triangles
The final row was were the rubber hits the road. I was trying to ensure that the last row would result in a flat surface across all of the glass pieces. That way when I started on the pieces that make up the bottom of the shell I would have something easier to work with. I can't say that it really was flat, but it was fairly close, and somethings that's all you are going to get.
Step 12: All Illusions of Symmetry Are Gone
At this point I had completed the top of the shell and the last layer was a fairly flat. Unfortunately by this point the left and right side of the shell were too different to really be able to try to make a pattern that would fit both. So for here on out the left and right sides were going to be different, and I would need to make twice as many patterns.
To pattern the bottom I started taping poster board strips around the bottom and angled the cuts on the ends to bring them into position. Taping this all together, I could see that the edge was again no where close to flat. However, at this point I needed to make the bottom flat so that I could easily make a base to attach it to the wall. To flatten the bottom edge, I took the entire pattern still taped to the turtle and ran it on a 12inch disc sander to sand the paper flat. It worked okay but the paper flexed and needed to be cut straight between each corner. It was very tedious, but worth it to finally get to a flat surface
Attachments
Step 13: The Wraparound
With all the templates for the first layer under the shell complete. All of the pieces were again numbered, cut out, and tacked in place. Once I was happy with their placement they were completely soldered into place.
Step 14: Flippy Flappy
Since the project was now going swimmingly it was time to make the flippers.... The front flippers went fairly easily since they were just a simple arc. The rear legs were a flight. The wavy edge for the toes was very challenging and I broke at least a handful of them before finally managing to break it along the line. The key was to tap the scored glass with the back of the glass cutter to try to get the crack to propagate before breaking along the line with the running pliers. I found that making that cut first and then trying to make the rest of the flipper after was the best way to tackle it.
Attachments
Step 15: Sea Turtles Have Huge Noggins
The next step was to pattern the head. This one proved to be the most challenging pattern to make for the whole project. The sharp curves and small pieces required to make the eyes and mouth provided a challenge, since the visible part of the glass "shrinks" once they are taped.
Attachments
Step 16: An Illuminating Experience
With the head soldered on the outside it really felt like I was close to the end and a lighting check was irresistible. I originally thought that the small nightlight style bulbs would be good for inside the head and body, but they proved to be too directional of a light output. As a result I ended up switching to LED light strips and an LED undercabinet light.
Step 17: The Ship in a Bottle Approach
The bottom of the shell is black to prevent the light form the shell from overpowering the blue backlight beneath the turtle. Soldering the backside of these pieces was some of the trickiest soldering on the whole project, but since it's the inside it doesn't need to be pretty. Which is good because after tacking everything to the edge,I had a little mechanics mirror inside and was trying to solder upside down. It was impossible to know if I had managed to hit everything, so I just kept going until it felt solid.
Attachments
Step 18: A Trip to the Beach
I spent way to long shopping for the perfect glass to project a wavy light pattern to mimic the sea. I eventually settled on very textured translucent blue glass, that when illuminated at close range with an LED gave the right effect. I didn't end up making true patterns for any of the pieces in this step because they are all just rectangles the length of the piece that that butt up against, and 1 inch tall. The base pattern provided has the length of each edge, and thus can be used to make each. These were the easy pieces I had been looking for the whole time!
Attachments
Step 19: Test the Waters
Eager to see what the back glow effect would look like I threw the whole led strip into the turtle to see!
Step 20: Hang Ten
To allow the turtle to be hung on a wall for display a ring was needed. A SOLID ring at that. The finished turtle weighs about 10 lbs. To make sure that it could be supported safely I used a soldered a brass rod rod onto the base layer of blue glass. I ran the rod down a couple joints in in the layer to ensure that it wasn't just held on with the foil tape. The result was a ring that became one with the lead skeleton of the turtle.
Step 21: Lead Free Solder!
The blue backlighting is illuminated by a series of white LED light strips adhered to a piece of aluminum to form a heat sink. The strips are stagger to ensure that there aren't noticeable bright spots where all of the bulbs align. The nice thing about the LED strips is that they can be cut to nearly any length, and that they are very easy to bridge between. As a result the only wire feeding in is the black wire that is attached to the heat sink with wax thread to provide strain relief. The other strips are then powered by jumping between them with the white wire. I am not going to go into to much more detail on how to work with these strips, since there are numerous Instructables and videos showing the process. Suffice to say they are an awesome product that offers unmatched ease of install and customization. Just imagine what someone could do to the water affect with and addressable led strip!
Step 22: The Light Finally Came On
The head of the turtle was done much the same way. I took all of the light strips that would be going in the head and jumpered them all together so that I would only need to pass one wire from the shell into the head. To help position everything I transferred the LED strips from their backing onto a piece of wax paper. This allowed me to position them inside the head, and the carefully peel the backing out from under them leaving them in place. The result was perfect, and evenly illuminated turtle head.
Step 23: Hide the Light Bulbs
Unfortunately once all the lighting was installed in the turtle, it became obvious that you could see the individual lights inside of it. It can even been seen in with the illuminated turtle head, which had a much more opaque glass than the body of the turtle. Needless to say I wasn't pleased with this result and started searching for solutions. I found a few glass frosting options both in spray and brush on form. Since I would need to get inside of the shell and head I opted for the brush style. It took about 9 coats of the frosting to finally hide the lights inside the shell. Despite the desire to apply thick coats, thin coats were required. It was water based and would liquify previous layers if applied to thickly. When it was finally finished I was thrilled with the result. The overall color didn't change but the shell was now opaque, even though some of the glass was translucent.
Step 24: LEDs Dont Burn Out... Right?
To power the lights in the head, I had to drill a hole through the shell. It was a nerve racking operation because cracking a piece here would surely mean hours or removing solder replace the panel. To do it I used a diamond bit in a rotary tool with lots of water as cooling lubrication. Eventually I was thru and able to pass the wire. Then came attaching the head to the main body. I debated all sorts of clever ways to try to keep the inside of the head accessible incase there were ever any issues with the lights inside of it. Ultimately opted against any of them, trusting the supreme reliability that LEDs are touted for. Time will tell if that was a mistake, because now they are soldered inside of the head...
Step 25: First Steps
Finally the all of the soldering, cutting, taping, and more taping was done! The turtle was nearly finished. I took to opportunity to clean up some solder drips inside of the shell, and to neaten up a few of the first solder joints that I had made on the project since they were not as clean as the later ones.
Step 26: A Touch of Gold
As much as I liked the look of the silver solder lines, I was looking for something a little warmer and less bold. So I used a copper patina to change the solder from silver to an aged copper color. The process is pretty simple. The cleaner and smoother the solder joints the brighter the resulting finish. Just brushing the solder joints with soapy water results in a darker finish, while polishing with compound results in a bright shiny finish. After that all that is required is brushing on the liquid patina and allowing it a little time to set, it is then rinsed off with water. Here I had to be super careful to not get any on the glass frosting which dissolves in water!
For this opted to just brush clean the surface it so that the solder wouldn't be the focus of the piece.
Step 27: Finally Home
If you made it this far thanks for sticking with the read. I hope that you found the project and its presentation enjoyable.
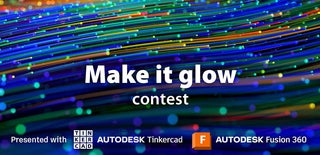
First Prize in the
Make it Glow Contest