Introduction: Fallout AER9 Laser Rifle (3D Printed)
The AER9 Laser Rifle is quite possibly the most recognizable object from the Fallout series. It embodies everything about the game, The "World of tomorrow today" feeling, the thought that everything is going to be possible in just a few years, a great war that applied these mentalities to weaponry.
Printing one has been a thought of mine ever since the AEP7 Laser pistol, now about 2 years ago. It wasn't really that it wasn't possible, it would just take a ridiculous amount of time. After one too many requests from people, I finally decided that I might as well do it, and here we are. A completely 3D printable version of the AER9 Laser Rifle from Fallout. Because I like making it difficult for myself, I made one with a working reloading mechanism. Also I added laser and laser sound to it, to make it even better. This model is about as accurate as I can make it.
Now not everyone might like the challenge of the working reloading mechanism and I have to be honest. I thought it would be simpler when I was designing it. It is quite a difficult (but rewarding) addition. Because of the difficulty, I have also added the files to make a Laser Rifle without the reloading mechanism.
The Laser Rifle is over 850mm long (3') and weighs about 1.5kg. It took well over 70 hours to print and double that for all other assembly steps. I will also have to warn anyone that wants to make one of these, this is a difficult project. The non-reloading version is a massive job printing and assembling. The reloading version requires additional skill and a bit of improvisation to assemble. Only start on this if you are sure you can handle it. If you do finish one, I assure you that it is worth it.
Step 1: What You Will Need
To make an AER9 Laser Rifle, you will need a few things. What you will need regardless of version is:
Necessary materials
- 3D printing Filament, at least 1kg, probably a bit more;
- Aluminium tube, 12-13mm OD, 185mm long;
- Aluminium strip, 2x10mm and 2x20mm, about 200mm each;
- Plastic glue;
- Silver (nickel), green, yellow, red and black paint;
- Sandpaper;
- 2 small cross headed screws (1-2mm thread OD) for the back;
Screws, nuts and bolts are counted by hand in the CAD model, so I might have missed one or two. Please consider this when ordering.
- 3x M3 screw, 10mm (DIN 84);
- 3x M3 countersunk screw, 6mm (DIN 963);
- 6x M3 countersunk screw, 10mm (DIN 963);
- 8x M3 countersunk screw, 16mm (DIN 963);
- 6x M3 hex cylindrical screw, 10mm (DIN 912);
- 1x M3 hex cylindrical screw, 16mm (DIN 912);
- 1x M4 threaded rod, 22mm;
- 2x M4 threaded rod, 28-30mm;
- 1x M4 threaded rod, 36mm;
- 2x M4 nut (DIN 934);
- 1x M4 hex cylindrical screw, 10mm (DIN 912);
- 2x M4 hex cylindrical screw, 16mm (DIN 912);
- 3x M4 hex cylindrical screw, 20mm (DIN 912);
- 3x M4 hex cylindrical screw, 40mm (DIN 912);
Tools
- A 3D printer, capable of support material, roughly 140mm x 140mm x 140mm;
- Basic pliers, screwdrivers and hex keys;
- Files (diamond files work great on plastic)
- Paper color printer to make the decals;
- (Optional soldering iron);
To make the Reloading mechanism, you will need additionally:
- 2x 8mm round steel rod, 110mm;
- 2x LM8UU bearing;
- 4x 624ZZ bearing;
- Rubber band (1mm OD), at least 0.5m in total;
- 2x M3 hex cylindrical screw, 6mm (DIN 912);
- 2x M3 hex cylindrical screw, 8mm (DIN 912);
- 5x M3 hex cylindrical screw, 10mm (DIN 912);
- 3x M3 grub screw, 4mm (DIN 916);
- 1x M3 grub screw, 8mm (DIN 916);
- 2x M3 grub screw, 16mm (DIN 916);
- 2x M4 threaded rod, 58mm;
- 7x M4 nut (DIN 934);
- 8x M4 washer (DIN 125-1a);
Optional materials to make it sound and laser work:
- Arduino Uno;
- Arduino Wave shield;
- Speakers;
- 5V red laser module (12mm OD version preferred);
Step 2: 3D Printing
Now it is time to start your printer. In the downloaded files, there are the STL files for the 3D printer, PDF files for the decals and diagrams, and the schematics and code for optional electronics. You can download the Laser Rifle files by following the link below:
http://ytec3d.com/aer9-laser-rifle/
My parts were printed (except for one part) on an UP! plus. The exception is "AER9 body front" which was printed on on my Mendel V2. The parts were printed in PLA at layer thickness 0.3mm. This way it took me about 70 hours of 3D printing. UP! printers are not known for being particularly slow, so depending on your settings, it may take longer.
To print these files you will need a printer of at least 140mm cubed (or an UP! plus) that is comfortable with support material. All parts are designed for 3D printing, which means they either need no support (45 degree overhang) or they have a 90 degree support. There are some small exceptions to this, most notably in the stock, where you will have the big round holes to support. Other than that, most parts only require relatively simple support.
One part may be slightly too big for your printer, depending on the settings, the "AER9 body front". In the Z-axis, it is possible to scale it down by 1-2% to make it fit. It will not impact the shape too much. Please only scale it in the Z direction (scale the height) and not in X and Y (both sideways directions) or the "body front" will not fit the other pieces.
Step 3: Pre Paint Assembly
Before paint, a few of the pieces need to be glued together. I found glue for hard plastic to work best. It cures in under a minute and is fairly strong. The pieces that need to be glued together are: The front and middle body, the seesaw, the stock and the handle pieces.
The body and seesaw are fairly simple, with only two pieces, so the photo's are guiding here.
The stock requires a bit more work. It consists of 4 stock pieces, 3 mounting plates to add strength and 2 sets of cylinders. Figure out which mounting plate goes in what cavity before gluing, they only fit in one cavity. 2 pieces of M4 threaded rod, 1 22mm and 1 36mm can be used to align the cylinders. The 22mm goes on the small set of cylinders. The 36mm goes on the large set. You can use an M4 screw to cut the threads in the cylinders before mounting the threaded rods. Test fit everything, and when it looks like it will fit properly, glue everything together.
The handle consists of 2 sets of 2 plates. There are tiny clamps that can be used to hold the pieces together. Glue each set of 2 plates together, but do not glue the 2 halves together, or the switches can't be mounted later. I also used putty to get rid of the printing lines on the handles when they were glue together.
Step 4: Painting
Painting can be done in many ways, so there is no one right way. It is however the most important stage. Mistakes made earlier can be covered here, and mistakes made here will show later. Here is how I did it.
First I used coarse (60-80 grit) sandpaper on all parts to get rid of most of the printing lines. Places that could not be reached by the sandpaper were sanded using a set of diamond files. I worked the plastic until most of the printing lines and flaws were gone. I also used putty where the parts could not be sanded (like the bottom of the part, where lines are the weakest).
When the parts were sanded, I used a filling primer to prime all the parts. Filler primer leaves a thicker layer of paint that can be sanded with 400 grit wet sand paper. With plenty of water the parts were sanded. This left a surface almost void of printing lines.
Next a spray can of silver paint was used to paint all Rifle parts. I made hooks out of steel wire to hang the parts from.
The remaining colors were painted with bottles and tubes of paint, with a paintbrush. The green body of the rifle is the biggest colored piece to be painted. Use more than one coat to properly cover the surface.
Painting the MF cells was more fun. They have a dark red base coat, and they need to be yellow. Yellow has poor coverage, so about 10 layers still only partially cover the cell. Black and silver however have full coverage in 1 coat, so extra care was used with those colors to not go over the yellow.
Step 5: (The Reload Mechanism)
If you have the working reloading mechanism, you'll need to assemble and test that before assembling the rest. I can't put enough words here to properly explain the complexity of the system, so I made a video of the mechanism coming together. I also have a few images that show general assembly and where the rubber bands go.
Step 6: Assembly
Putting the Laser rifle together is also a task too big for for simple text to suffice. I would need to add at least 5 more steps to properly explain it. Therefore, to shorten this Instructable, and make it clearer for everyone, I made a video of me assembling it. No electronics, no tube, but just mechanical assembly.
A few words before you watch the video. Only the grip and the stock are held in place by nuts. All other screws are tapped straight into the plastic. The hole in the handle was taped with an M3 thread cutting too because it is too fragile to be cut with just the screw.
The video is 12 minutes of me assembling the thing. It serves as a reference, but it is not particularly exciting. I hope that it helps anyone trying to assemble one of these.
Step 7: Custom Parts
Included in the download files there is a PDF of a bending diagram. On this diagram, you can see how to bend the release handle, the reloading handle for the reloading and non reloading rifle, and the tube clamp.
Bend the aluminium parts so they look like the parts on the bending diagram. There is not really much more to it.
Step 8: Weathering
Weathering adds character and a story to any prop, and is very important especially for a fallout prop. This rifle is supposedly over 200 years old. It needs to show this. Before you start weathering, it is brand spanking new. When you are done, it needs to look like it spent half of its life in the dirt.
I use a disposable paintbrush, paper towels and black acrylic paint for this step. Apply and incredibly small amount of black paint to the tip of the brush. Then brush against a piece of wood or plastic until you only keep a tiny amount of paint on the brush. Then, dab whats is left carefully on the part. If you use too much, immediately use the paper towel to wipe of the excess. Black paint in coats this thin sets in seconds, so be quick. Repeat until you have the thickness of weathering you want. This step may take quite a few hours. I spent about 12 hours getting the coat of muck the way I wanted it.
The photo's show the result after 8 hours. I wasn't satisfied and a few days later I added an additional layer to the prop, that does not show in the photos.
Step 9: Decals
Decals give character to any prop. It is the fine detail that (combined with any weathering) makes a prop feel real.
The decals were printed out on paper using a color laser printer. I do think that an inkjet would do a better job, because the laser printer leaves a glossy color, but it still came out usable.
There are 2 different decals. The lines, that can be completely cut out, and the letters and shapes, that have an extra background. The lines are fairly simple. Cut them along the edges, and glue them on the prop using a glue stick or a small amount of general glue.
The decals with background are a bit more difficult. The background of what is printed needs to be merged with the background of the prop. I took a photo of my prop, added this as a background to the sticker in Photoshop, and printed it out. It was good enough on the first try. You color may not match to decal sheet I have provided. I did leave a decal with a white background, so any photo editing software can get rid of the background. Take a photo of the area that the decal needs to cover, and add it to the background of the decal. it may take a few tries.
My sheet for the MF cells was first based on the one from Volpinprops. This however contained a mistake that I did not like (the value of the MF cell). The therefore made my own version and added it to the download file. Mine will stay the wrong way, but the one downloaded is correct.
After the decals were stuck on the prop they were weathered the same as the prop itself to make them match the prop.
Step 10: The Tube
The tube requires a bit of creativity and depends on what is at hand. I used thick rigid coax cable to make this tube, but any rigid material should be fine. As long as the tube is between 6mm and 7mm thick (maybe 8 with some extra work), bendable and rigid.
Aluminium clamps should already have been bent a few steps back, so use those to clamp the tube down. The location has not been added to the 3D printed parts, so you'll have to drill them yourself. A small drill can be used to make holes where the clamps are mounted. Then with small screws, the clamps can be fixed in place.
Chances are that your tube is not the yellow it needs to be, so use yellow paint to make the tube (you guessed it) yellow. It may take a few coats. After you have painted the tube, use the same technique used for the rifle to weather the tube.
Step 11: The Optional Extras
The optional extras are, as the name suggests, optional. You can add it if you want to, but it is not necessary for the Laser Rifle. In my case, I added an Arduino uno with Waveshield and a 5mW red laser, with a trigger. I do not have a full set of instructions, only a rough code, a schematic and a simple explanation (so there may be gaps in the explanation).
The Waveshield is a way to get decent quality sound on an Arduino. Any explanation I could give would be poor at best, so I will redirect you to an Adafruit tutorial below. My circuit was made the same way as theirs, and any addition is on top of that.
https://learn.adafruit.com/adafruit-wave-shield-au...
The additions to the circuit are: A mosfet to drive the laser (technically not necessary, but out of courtesy), a trigger switch circuit and an on/off switch. This circuit was built on a piece of prefboard, small enough to still fit in the Laser Rifle body.
For speakers I used a set of Laptop speakers, compact and fairly loud. I drilled holes on the underside of the muzzle for the sound of the speaker. I also his the on/off switch under the muzzle. The trigger is a generic spring loaded tumbler switch with a flat lever. Here is a link, though it is in Dutch and doesn't have much information.
The code is a mauled version of the standard Wave library example: 'daphc'. basically, it looks for wave files on the SD card and plays every one, in a loop. By adding a trigger to activate the function and only having one file on the SD card, it plays the same file every time the trigger is pulled. An output for the laser was added, making it light up ever time the trigger is pulled. Additional coding magic is added to the code to make it interrupt the sound if the trigger is pulled again before the sound file has ended. Also if you hold the trigger for 9 shots, the laser will stay on (for photo's). Quickly pull the trigger a few times to make the laser turn off again. The code is messy, inefficient and complicated to read, but I it'll work just fine.
To make it work, follow the Adafruit guide on the Waveshield. This includes installing the library to your Arduino IDE. Add the sound file in the download files to an SD card (no other .wav files can be on this card). Upload the code to your Arduino and if you did it right, your Waveshield should play the Laser Rifle shooting sound every time you pull the trigger.
My version was a bit quiet. The amplifier on the Waveshield is not powerful enough to produce massive amounts of sound. If you want to make yours really loud, I suggest using a bigger amplifier (since laptop speakers are more than capable of producing a lot of sound).
Step 12: Final Thoughts
As said before, this prop was on my mind for almost 2 years now. When I made the Laser Pistol I already knew roughly how much work was required to make the rifle. My guess back then was about 80-100 hours of printing. I determined that it would be too much work and (combined with the relative little interest in the pistol) decided not to make it. In the years, I got quite a few people asking questions about me making a laser rifle. At some point I thought that I might as well do it, not having done a prop in a very long time. It was going to be a slow project, me only working on it when I had little else to do.
This was roughly 3 months ago. Fallout 4 was announced a month into the project, and I immediately determined that there was a new Pip-Boy for me to design as well. I first started and finished the Pip-Boy, because there were more people working on that. The Pip-Boy did amazingly well and I again put all my resources on the Laser Rifle. Painting, weathering and assembling it. All in all I spent an estimated 200-250 hours on this project. All in weekends and evenings.
This leaves me to the conclusion. Before I started this project, I knew it would be a massive undertaking, and I was right. Printing-wise, this is my biggest project to date. Painting was also a huge job. All in all, this project was probably as big as I am going to do. It has been an extremely rewarding journey, but I think I am done with the big props for now.
Is anyone still reading?
There is something I want to run by the Fallout fans / makers reading this. Ever since I started this, I have been pondering the thought of making a Fallout Power Armor. This is a project simply too big to do as a single part, so it would probably become a multi part project one piece of armor at a time, a bit like the projects of XRobots. This is a massive project going into hundreds of hours of printing, prop making (panels should not be 3D printed) and painting. All would be open source. All designs and specs shareable will be shared. I will only do it if there is going to be enough interest, but that is why I am leaving it here. Leave any thoughts in the comments or on the forum of my website. Other prop suggestions are also always welcome.
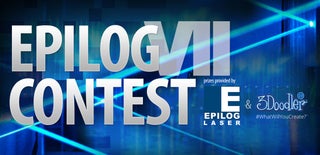
Participated in the
Epilog Contest VII