Introduction: Hexagon Shelf
Hexagons are the best and I had a blank wall in my livingroom. Putting one and one together, I wanted hexagonal shelves in my livingroom. The ones I made have a stained wooden outside, and a white inside. The hexagons are designed to be assembled without screws to keep the structure. The shelves have a wooden back used for reinforcement and mounting.
I had previously already made a set of three, so the three made here needed to be a good match to the ones I already have.
Supplies
To make 3 shelves I used:
- 18mm Solid finger jointed panel 30x200cm (This is I think the right name, but in dutch we call it "timmerpaneel")
- 9mm plywood sheet 61x122cm
- 6mm dowel pins
- Woodglue (I used polyurethane woodglue)
- White paint, primer and Oak wood stain (use whatever paint you fancy)
- Caulk plus finishing materials like soapy water
- Screws and plugs for mounting the shelf
The tools I used:
- Table saw
- Miter saw
- Jigsaw
- drill with 6mm wood drill bit for the dowels
- drill for the mounting hole and countersinking bit
- 2 small ratchet straps
- 1 glue clamp
- Paint tools
- Caulk gun
- Hammer drill with right stone drill for the plug (for mounting the shelves)
Step 1: Cutting the Sides
The shelves are each made from 6 pieces of wood, each cut to 30 degrees on either side. A miter saw was used to cut the whole board in 9 strips with roughly 18.7cm on the short side 20.5cm on the long side. If you are making your own, the exact dimension is not important, only the angle and that all planks are the same. Mine needed to match a previous set, so I needed to be precise here.
Each cut the board is placed against a hard stop which my saw has, and then the cut is made at the 30 degree angle. The board is then flipped, placed against the stop and cut again. This step is repeated until you have the desired amount of pieces. Be sure the plank does not move while cutting. With angled cuts the saw tries to move the plank sideways, ruining the cut.
My board was 200x30cm, which yielded me with 9 strips of roughly 20x30cm. I want my shelves to only be 15cm deep, so with a table saw I halved each plank. This gave me 18 planks in total, making 3 shelves.
Step 2: Cutting a Slot
To hide the back board of the shelf, a slot needs to be cut in the wood, roughly half the depth of the plank (in my case 9mm). It needs to be at least as thick as the back board, which in my case is also 9mm. I made an 11mm wide, 9mm deep slot. This slot is on the side which was cut, so the clean chamfered side becomes the front. Make sure the slot is in the short side, else your slot will be on the outside of the shelf.
The table saw is set to 9mm tall. The fence is set so the cut is around 8mm from the back edge of the plank. Then each piece is carefully cut on the saw. The fence is then moved to make another cut with the furthest edge 18-19mm from the back edge. The final cut is placed somewhere in the center. I was left with two thin strips of wood which I removed with a chisel. if you are willing to make another cut you can simply remove all the material with the saw.
Step 3: Dowel Holes
The shelf is held together with dowel pins. Each plank has three 6mm dowel pins per side.
To make the holes more accurate I made a 3D printed tool to align my drill. I have included versions of this tool with 5, 6, 8 and 10mm holes. I used the 8mm one with a metal bushing, but if you are careful the tool should last at least a few shelves. The tool needs to be oriented with the side with the holes on the printbed.
If you cannot make this tool, you can simply drill 3 holes in each side, and then use dowel center pins to mark the dowel holes in the other side of the plank before drilling.
Step 4: Making the Back
The back is made of plywood. This back provides strength and place to mount the shelf. Measure the inside of the hexagonal shelf, and mark this shape on the wood, with enough allowance to fill the slot in the planks. A jigsaw was used to cut this shape out of the plywood once. This piece was then used as a template for the other two. As luck would have it, the 3 pieces required fit perfectly on the piece of plywood I had left, but your results may vary.
Step 5: Assembly
The shelf can now be assembled. I covered the floor in paper so the glue would not stain the floor.
Pick six pieces and test fit them with the back. Fix any issues you find here. Then disassemble the pieces and lay them out. glue each dowel pin in one side of the plank, then add glue to the other side and place the two pieces of wood together. Make two halves of the shelf, with the dowel pins prepared in both sides.
Glue the slot in the back of one halve, and place the back in this slot. Then glue both planks on the halve with the back. Last glue the slot in the other halve and place this over the assembled halve.
Lay the shelf with the back on the paper and use ratchet straps or plenty of clamps to tightly hold together the shelf. Then with another glue clamp, the frame can be pushed around until all sides are the same length and shape.
Allow the glue to dry for however long required.
Step 6: Cleaning It Up
Polyurethane glue foams and hardens. The excess oozes out from the seams. This excess glue can be removed with a chisel. depending on the glue used cleanup is not required.
Step 7: Mounting Plate
The back is mounted straight against the wall. If there was nothing behind the shelf, the wood of the back would bend. For this, a small piece of the plywood waste is used to make a mounting piece in the top back of the shelf.
This piece was cut from a bit of wood which already was used for the back, around 8cm tall. This piece was glued in place and mounted with 3 screws to hold it in place while the glue set. The screws can also be replaced with clamps or weights.
A fancier person would make this mounting plate so the shelf could be mounted blindly, but for this project I kept it simple.
Step 8: Staining the Wood
The style I chose uses a stained wooden outside, and a painted inside. First the outside it stained. This way the paint can cover up the pieces that were not supposed to be stained.
Step 9: Painting the Wood
Painting for me consisted of the following steps.
First the backs received a single coat of primer. This was simply to seal the wood.
Second the fronts were masked with masking tape on the chamfers. The inside also received a single coat of primer.
The primer was sanded to smooth the surface.
Caulk was used to seal all the seams on the inside. The back and side were caulked, then the excess was removed and then the seam was smoothed with a finger dipped in soapy water.
Last two coats of paint were used to coat the inside of the shelf.
The masking tape was then removed.
Step 10: Mounting
The shelves are simply mounted with screws through the back to the wall. For this two holes were marked and drilled in the back, then countersunk.
A screwdriver was used to mark these holes in the wall. A hamerdrill was used to make holes for the screws (8mm in my case). 2 plastic plugs were pushed in the holes and the shelves were mounted with 2 screws in the holes.
Last the screw heads were painted with the same paint as the back to mask the heads.
The shelf is now ready for use carrying all your fancy belongings.
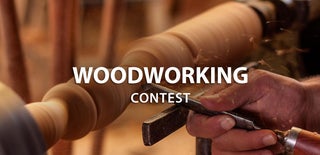
Runner Up in the
Woodworking Contest