Introduction: Laser Cut Stacking FIFO Can Holder
I use a lot of canned goods in cooking, and I prefer to keep some stock of food at home for unforeseen circumstances. This combination means that I have a small supply of cans that need storing and preferably sorting. Cans keep for a long while, but not infinitely, so having the cans stored First In First Out (FIFO) means I do not have to check all dates to find the oldest can. I can simply pick the front can.
For this I wanted to make a storage of cans for my cabinet.
Supplies
To make the can holders I used the following items.
Materials:
- 4mm laser cutter plywood (or any preferred 4mm material)
- 2 sheets of 300x400mm were enough for one small can holder.
- Wood primer
- Wood paint in a color of your liking
- Wood glue
Tools:
- A lasercutter of at least 40W, with a bed at least 300x400 (most CO2 lasercutters)
- Sandpaper
- Paintbrushes
Step 1: Design
The design I picked is a two level storage. The cans are inserted at the top. They can roll to the back and fall down on the bottom level. Here the cans roll back to the front, where the cans can be picked up. The cans will automatically exit in the same order as they were put in, making the holder First In First out.
In the back is a small addition called the damper. When the cans fall, it is quite a hit on the holder. To prevent damage to the cans and the holder the curved piece called the damper is added. This has a radius slightly larger than the can. This forces the can to roll towards the front, taking some of the energy of the fall.
The design comes in 2 flavors. Stacking and Non-stacking. The stacking variety is tall enough so another can holder of the same can size can fit on it. A Non-stacking can holder can be placed on a stacking can holder, but it cannot receive another can holder on top of it. Different can sizes will not fit on top of each-other.
(A small change visible between my photo's and the final design is that the 'fence' of the top level has been removed. This part turned out to be the difference between the can holder fitting and not fitting in my space. Thinking about it some more I came to the conclusion that the part was redundant and I removed it in future files.)
Step 2: Files
Included are the files to cut the can holder I made here plus future sizes I might make. The design has a few parameters. The 2 numbers are the diameter and length of the can holder in millimeters. This number is the size of the cans for the can holder, with clearances. 68x72 for example is 68mm diameter, 72mm tall cans. The height of the can (in this case 72mm) has a width of 75mm in the can holder to give some clearance.
Second is whether the can holder is stacking or non-stacking. Non stacking can holders use less material but the cans stick out at the top of the can holder. Stacking holders have more material, but can receive another can holder on top. You can stack a non-stacking can holder on top of a stacking one.
You can only stack can holders of the same size.
The parts that are in one can holder are:
- 1x Back
- 1x Bottom fence
- 1x Bottom
- 2x Damper
- 2x Foot
- 2x Side
- 1x Top
The annotations of the images have the names of each component. The exact sizes can be different, but the rough shape is the same across sizes.
Attachments
Can holder 68x72 non-stacking back.DXF
Can holder 68x72 non-stacking bottom fence.DXF
Can holder 68x72 non-stacking bottom.DXF
Can holder 68x72 non-stacking damper.DXF
Can holder 68x72 non-stacking foot.DXF
Can holder 68x72 non-stacking side.DXF
Can holder 68x72 non-stacking top.DXF
Can holder 68x72 stacking back.DXF
Can holder 68x72 stacking bottom fence.DXF
Can holder 68x72 stacking bottom.DXF
Can holder 68x72 stacking damper.DXF
Can holder 68x72 stacking foot.DXF
Can holder 68x72 stacking side.DXF
Can holder 68x72 stacking top.DXF
Step 3: Cutting the Parts
The parts can be cut on any CO2 laser cutter of at least 40W. The design is optimized for a cutter size 300x400mm, so any smaller and the parts might not fit. A larger laser cutter should work just fine.
I used the laser cutter of my local hackerspace, Tkkrlab. This is a tiny 40W laser cutter, but it manages 4mm plywood just fine. On this laser, the parts for one can holder take roughly 10-15 minutes. My 68x72mm can holder require more than 1 sheet. The non-stacking can holder leaves more of the second sheet.
What settings you will need depend on your available laser cutter and materials used. I needed 8mm/s at 100% power for my material.
Step 4: Painting
The burnt edges are ugly and smell. I opted to paint the holders. I first applied a single layer of primer on all parts before assembly. This because painting assembled is difficult. After this you can choose. I chose to assemble the can holder and then paint it, but you can also first paint it and then assemble it. Painting before assembly makes sure all parts have the right color, but might interfere with the fit of the tabs. Painting after makes some surfaces that are not really visible hard to reach.
After assembly I added 2 layers of paint in the visible locations. Where I could not paint afterwards, the layer of primer should protect the wood from dirt and fluids.
Step 5: Assembly
The can holder should assemble fairly simple. All components slot together and most components should only fit one way. Only the top can realistically be placed backwards. The front should be flush.You can simply glue all pieces together in one go and have the unit dry completely assembled. It is advised to only glue in the inset portions of each part. If you glue the protruding parts, the glue will not touch anything and just stick through.
- Lay one side on the table.
- Glue the the 2 dampers in the back, and glue to bottom to the back.
- Glue the assembly of the bottom, back and dampers to the side on the table.
- Glue the bottom fence in place.
- Add the top to the side (the photo's also show a top fence, but this was later removed).
- Glue the second side on the whole assembly. Make sure all tabs line up.
- Flip the part around and add the feet to the holder. Only glue the can holder, not the feet to make sure glue is not in visible places. Use clamps to keep the feet in place when the glue sets.
- Lay the can holder on a flat surface and add some weights to it while the glue sets.
When the glue has completely set, the can holder is complete. If you only primed the part beforehand, you can now paint the can holder in it's final color. I went with white since I had a can laying around.
Step 6: Improvements
Several changes were made during the design, and some more changes might happen later. In some of the photo's the can holder before changes can be seen.
During the design the following items were changed:
- The damper was added to the design. Cans fell hard on the bottom, and I was worried that either the cans or the can holder might sustain damage. The damper was added in the form of a curved piece that has a larger radius than the can. This forces it to roll and takes some of the energy of the impact.
- The top fence was removed. This part served no purpose and added extra unnecessary height to the can holder. This made the holder no longer fit in my cabinet.
- The back was lowered so that the feet did not interfere with it.
Some more improvements that I hope to make are:
- Make more sizes to also store the larger size cans. 75x111mm is already in the pipeline for my tomato cans.
Step 7: Added Size: D76x119mm, 600mm Deep
This design is only for the non-stacking can holder. It holds cans of D76x114mm and is a whopping 600mm deep. It is designed to be made with 6mm thick sheet material, though 1/4" might fit with some minor adjustments.
Attachments
Can holder 76x119 non-stacking 600D back.DXF
Can holder 76x119 non-stacking 600D bottom fence.DXF
Can holder 76x119 non-stacking 600D bottom.DXF
Can holder 76x119 non-stacking 600D damper.DXF
Can holder 76x119 non-stacking 600D foot.DXF
Can holder 76x119 non-stacking 600D side.DXF
Can holder 76x119 non-stacking 600D top.DXF
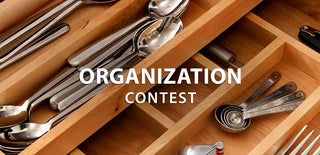
Second Prize in the
Organization Contest